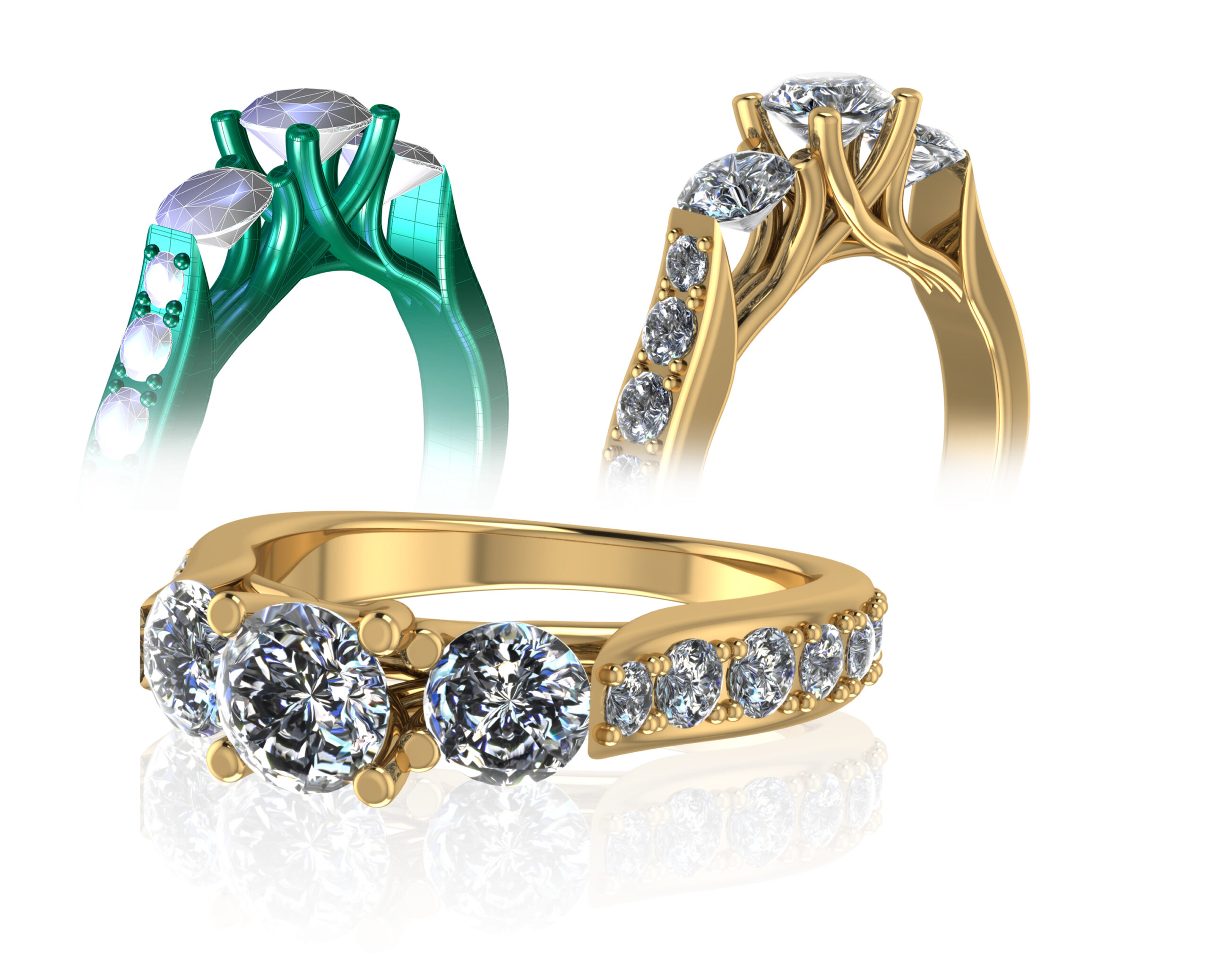
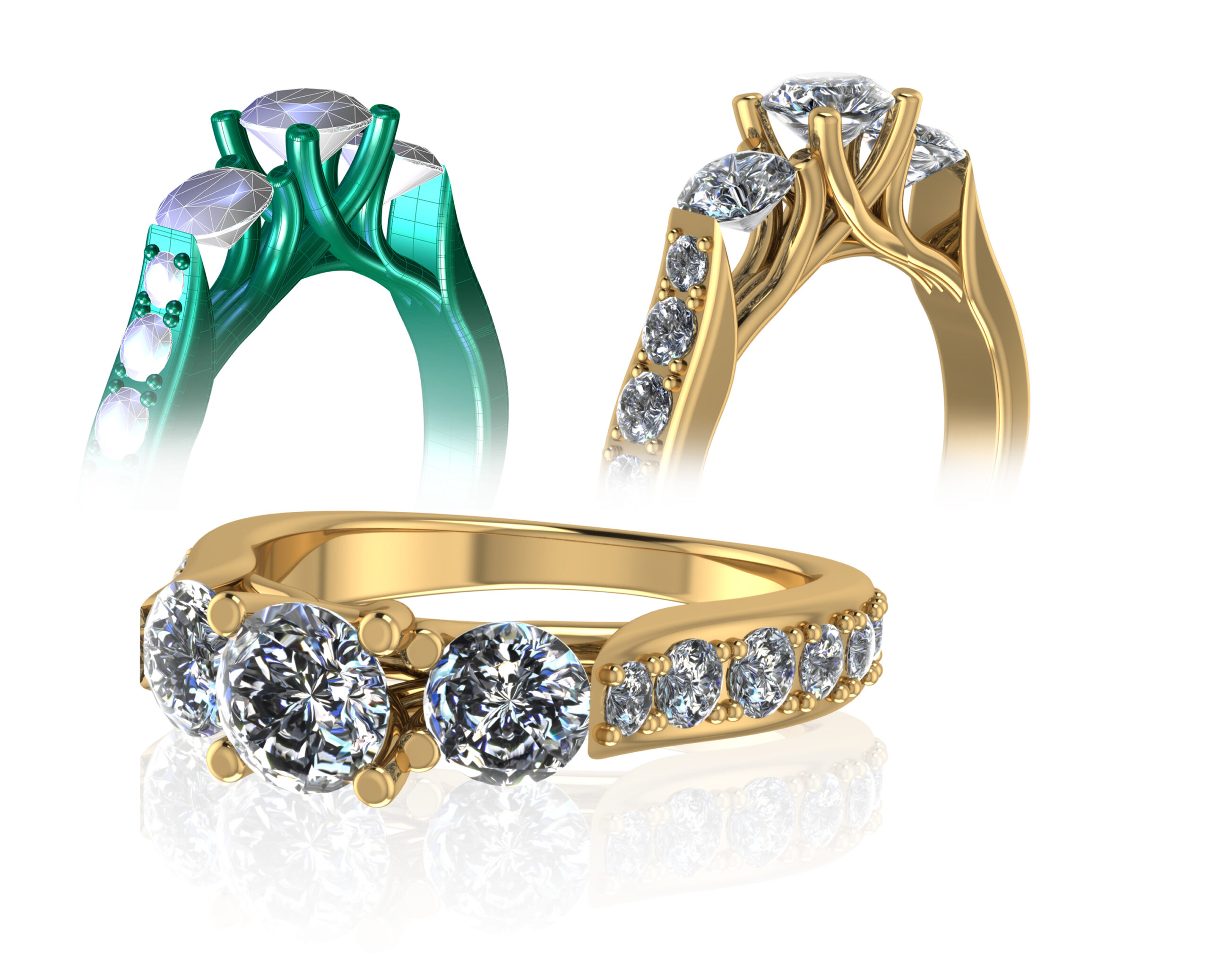
CAD/CAM Systems for Metals and Jewelry
If you are involved with computers you know how rapidly things are changing, prices are sinking and capabilities increasing. Computer use in increasing in the jewelry field and at some point, probably sooner than you think you will see computers used in ordinary jewelry stores to manufacture jewelry and its components. The following comments are intended to introduce some of the issues concerning this coming change.
23 Minute Read

If you are involved with computers you know how rapidly things are changing, prices are sinking and capabilities increasing. Computer use in increasing in the jewelry field and at some point, probably sooner than you think you will see computers used in ordinary jewelry stores to manufacture jewelry and its components. The following comments are intended to introduce some of the issues concerning this coming change.
The Present
CAD (computer aided design) drawing and drafting systems are widely used in general industry for designing models for mass production. Their advantage lies in the speed of organization of very accurate components or elements and then their rapid translation into working 'blueprint' diagrams for the workshop. As well one only has to do the work once for a repetitive component and so there is an increase in efficiency as previously prepared standardized parts of a design may be re-used
For certain kinds of very exact translation of design into three dimensions an investment in a CAD/CAM system for 3-D prototyping may make sense. Large manufacturers in the jewelry industry have used CAD and in some cases CAD/CAM (Computer aided design and manufacturing) for some time. Computers are starting to be used in similar ways in the jewelry industry in smaller scale establishments and we will see this more and more
In the form of 'engraving computers' routers as small as 4 thousandths of an inch are used to create low level perfect relief milling and piercing for models in the lapel pin industry. Somewhere there are modelmakers whose lives were spent making lapel pins (a relatively simple but demanding relief problem) who are now on the street or have revised lives. At this point some modelmakers in the jewelry industry are starting to be replaced by CAD/CAM systems, up till now mostly at the level of lapel pin and less complex model making. Such evidence of change will increase
When using CAD/CAM there is a significant change from traditional jewelry making methods in that the designer's workpiece is made exactly as designed; there is no intermediate maker to influence design, no filtering minds between the designer and object. The computer does however act as a filter itself between the maker and the material and will thus subtly affect the design directions chosen as a reflection of what is possible to do with the system used. With time this subtle design limitation may end up distinguishing hand made unique work from factory made work in the publics mind but given how the public generally is unable to distinguish hand made from cast and factory finished work at this point I wouldn't bet on it
The designer need not necessarily have technical knowledge concerning how the object is actually made as the CAD/CAM (computer aided design, computer aided manufacturing) system can take care of many of those concerns. As 3-D prototyping systems become more commonplace it will be even less of a worry to the designer. So the actual 'creation' of a physical object is now possible for a designer who may not know 'how' to actually make an object in the time honored hand methods that goldsmiths pride themselves on. Most current 3D prototyping systems make the object in some kind of plastic (or carve it in wax) which for jewelry purposes can either be molded from directly or burned out and cast just like an ordinary wax model
Recent developments as a result of the introduction of computers include the virtual elimination of sign painters in the wake of computer operated vinyl sign cutting machines and the introduction of wax carving machines for the jewelry industry for under 4000.00 dollars (of course the computer driver and software are in addition). A number of jewelry companies use CAD/CAM now to machine steel dies for plastics injection for casting
The U.S. military is really pushing research on CAD/CAM in solid metal for aircraft carriers and for companies of soldiers on the move. This would mean they would not have to have an inventory of replacement metal parts for engines or machinery. The computer room and milling system would machine the required part on the spot from a big chunk of metal, or sinter it with lasers from powder (that sounds like a Star Trek 'replicator').
Dentists right now are beginning to use CAD/CAM for making caps for teeth. After the dentist has ground off all the tooth they want to as a seat for the cap they shine a laser around the space they have created. The digitized information about the space goes directly to the lab across town over the phone lines and a milling machine mills the tooth cap from solid gold alloy (or whatever material is being used) and the finished cap is delivered within 45 minutes to the dentist's office for installation - you never have to get out of the chair. This has implications for the waxing, casting and finishing professions in the dental industry and is the future of findings, wax catalogs and some jewelry manufacturing. The implication is the 'factory' functions are now brought in to the home or business desktop rather like what happened in the publishing industry with the advent of 'desktop publishing'
The car and machine part manufacturing industry now uses CAD/CAM extensively for 3-D prototyping. To be able to model a part, have it made almost immediately in plastic to check for actual fit against other parts has already saved them tens of millions of dollars in development costs for machine parts and design glitches.
Industrial architects building chemical plants or an oil refinery now conduct virtual walk-throughs in their structure with different body types, arm lengths, head heights and so on to eliminate poor placement of piping and controls etc. When satisfied in the virtual model the whole thing is made using stereo lithography (3D prototyping) to produce a polyethylene physical model of the whole plant, a task that use to take a team of model makers months and many thousands of dollars
These types of changes in technical advance always have positive and negative sides to them. I always remember the thousands of Turkish peasants who starved to death in the winter following the invention of aniline dye and the subsequent immediate loss of market for plant dyes.
The slide rule makers too come to mind. Imagine being trained and specializing in slide rule design and making. Within a few short years that whole industry must have been devastated, established professional organizations evaporated, proud family manufacturing empires collapsed, lives disturbed.
That is unless the company or individual was smart enough to see the implications of a two hundred and seventy five calculator being sold for the first time in 1972. They would have to move quickly to have sidestepped the disappearance of their industry.
In 1994 I asked my class of second year college students who among them knew what a slide rule was. Only 2 of 20 did, the others had never heard of a slide rule. The two who did know did not know how to use one
Parts of the jewelry industry will be just as susceptible to technological change. Take findings for instance, at some point there will be a machine on the jewelrs desk which carves out a prong setting from the solid metal or sinters it in moments ready for use (lets call it a 'replicator'). The implications for factories that currently make prong settings are obvious. As a goldsmith or manufacturer in the late twentieth century it would be wise to be informed about potential changes to your field and to roll with it. Think of it not as being threatened or drowned by technological change but instead as surfing with it.
What smart findings companies should be doing soon is mapping their findings to obtain the 'tool paths' needed to make them in the new technologies and getting ready to publish them on CD-ROMs for creating findings and parts. You would then pay for the access code for each finding as you 'bought' it. When you realize that one can publish a CD-ROM for about three dollars this sounds like a whole new way for companies to make money (remember that 'buy low-sell high' rule'?) because of low costs. If I had a company that sold waxes I might start to look over my shoulder a bit and think about this too
Currently beyond the use of inventory systems, on-line gem pricing reports, word processing, drawing and colour stone matching there is some use in the jewelry industry of computer generated images as quality renderings when photographed from the display screen, output as a slide or printed out on color printers as they become more affordable. Lyn Strelau of Jewels by Design in Calgary scans his jewelry in to the computer directly with a desktop scanner and uses this for inventory, insurance documentation and created a computer screen 'slide show' that runs in the store when he has open houses and special events
Standard Macs and PCs can now run very sophisticated programs. Beside photographic manipulation such systems allow the user to generate three dimensional CAD designs with appropriate shading, perspective etc. and also to provide the 'tool paths' for Computer Aided Manufacturing (CAM) systems to use
Machining and milling systems for three-D prototyping in metal currently require an experienced machinist with a good knowledge of tooling to set up the appropriate equipment in conjunction with the CAD/CAM system. Other systems of 3-D translation or 3-D prototyping are available and rapidly sinking in price. Stereo lithography provides one way for the CAD design to be directly translated to a three dimensional model. In this procedure lasers are used in a container of liquid photo-sensitive plastic to build the model in the same manner as images are built up on the screen; that is that where they strike the fluid plastic they harden it as it is withdrawn from the liquid and the result is an exact model to the required scale with any hollow spaces or wire construction imaginable. An observer of this process reports that the exactitude of translation is better than is possible with even the best modelmaker.
The drawback is that the surface is very finely stepped, as in the 2D pixel dependent rendering on the screen but these steps can be easily removed before casting and advances in software are now eliminating them as a problem.
The advantage of this procedure is primarily in even results, perfect measurements and less time in implementing things like 7% shrinkage factors for precision model making for casting. New advances have made stereo lithography significantly cheaper than before and with far better resolution
A modelmaker friend of mine in Toronto informs me that some modelmakers are getting worried as the price for a stereo lithography system is now down to less than $70,000.00. This may seem a lot but several years ago it was well over a million and there is a guarantee of further price reductions. It would not take long for a system to recoup it's costs in saved salaries in the right kind of production company
One company in Calgary that has over 60 employees and makes 'School Rings' and sports awards rings now makes most of their models on computer and wax carving machines create the models for them. While I don't think that modelmakers will all be replaced I do think that some displacement will occur and that there may be pressures on some to start their own businesses or to take a demotion in position. In either case this will have some effect upon the industry. Competition at the commercial level will no doubt increase. It does however offer ways into the jewelry industry for people who do not have the technical skills to make a piece of jewelry in the standard methods. 'Computer specialist' will soon be a branch of the jewelry trade
Other 3-D prototyping systems now available include one where lasers shoot into plastic powders sintering the object (about $40.000) and one with two tools like little hot glue guns which move back and forth making the object by extruding plastic ($20.000). By the time you read this those prices will probably be halved and other kinds of 3-D prototyping will have been introduced
The user of the design program must be conversant with the needs of the goldsmith who will finish and the setter who will have to set the stones in the piece in order to provide for smooth manufacturing of the object. Ideally then the user would also have a goldsmith's education. The resulting object serves as an original artifact or a model from which molds will be made for casting the object in multiples for production. It might be useful for the industry to retrain it's skilled modelmakers where possible rather than relying on new computer trained workers without hands on experience in making jewelry
What occurred in the printing industry with the advent of desktop publishing systems and page layout and graphics programs was that at first companies handed the technology to their technical folks (the press operators) and said 'now you do it' but although the software capabilities were there the visual experience and design quality was not so they very soon had to go back and bring in designers again and now graphic design in booming as a career.
A goldsmith who also knows how to create in 3D modeling programs will be a pretty hot commodity in the near future
This situation would seem to offer a unique opportunity for art and industry training schools to educate their students in CAD systems. This would allow students to connect with industry in a new way as technique would no longer be quite the barrier it now is
Another change coming regards image manipulation. I remember a teacher of mine who I questioned about his use of a delicate sandblasted finish on a piece of jewelry (which I felt would not last five minutes when worn by a customer). At the time I was shocked when he said 'It only has to hold up for the photograph'. A couple of years ago there were rumors among jewelers doing the large US fairs (like ACC, Rosen, etc.) that some people had been juried in to shows based on slides of non-existent work, that is jewelry that was literally glued together for the shot, made in precious materials but was not actually a functional piece of jewelry except for the purposes of photography. Juries and groups have not yet faced the implications of being able to easily output a slide of an enhanced piece or to 'repair' open solder seams or pits on the slide.
CAD/CAM in Art Oriented Jewelry
Computers have been used in making art jewelry for some time. Vernon Reed in Texas used computers to design and program his liquid crystal displays for his jewelry. There are several imitators around including some very inexpensive work being done in Taiwan
Computers have been used for their rendering possibilities at a number of schools in the United States. The main jewelry program using computers in the US at the moment is Tyler School of Art in Philadelphia under the guidance of Stanley Lechtzin. He is extremely interested in CAD/CAM systems for the artist jeweler and has actively pursued the establishment of a center for it at the school. Tyler has been using computers for rendering for some time. They are equipped with Macintosh computers and interface with digital Bridgeport Milling Machines to complete the system. Their approach is to train and encourage their incoming graduate students to use this system.
You can get a sense of how they are using them at their world wide web site at: http://blue.temple.edu/~crafts/jmcc/jmcc.html. There are some intriguing discussions on their student and alumni mailing list discussion group which you can sign up for on the site. It tends to be pretty quiet when students are off for the summer though. There was for instance recently a discussion of the validity of 'Virtual Objects' and some suggestions that (perhaps like jewelry rendering and design) the object doesn't have to be made or to exist to be a piece of jewelry. The site is definitely worth a visit
Various innovative artist-jewelers use computers a great deal. Thomas Mann, a jeweler in New Orleans who is very successful in the United States works by combining ready made elements in provocative ways. Originally he bought these in large lots as cast-offs from the jewelry industry in Rhode Island. With growing success he found that he had to manufacture these component elements himself. At this point he has a line of repeated works which he composes using his own icons on a Macintosh. The people working for him are given print-outs of the designs to work from. His company with over 20 employees is heavily computerized with an in house relational database that keeps full inventory control and as orders come in automatically generates schedules, component orders, job directions for workers and so on. He and his five managers communicate via Email and notes to each other all day and it enables communications to run very smoothly
Mark Stannitz at RIT has used a dot matrix printer to stamp gold foil in patterns and letters. This might have applications for enameling with it or other uses. It is also possible to print directly onto laser-printer acetate (hint-don't use the wrong acetate in your laser printer or copy machine) and use it as a positive to make a photo-etching. Any printer can then take this (or even one printed on paper) and etch a magnesium plate for you which can then be rubber molded to get waxes for casting. This is ideal for things like school emblems, medallions, any mixture of text and line drawing that you need a relief model of. (hint-magnesium burns like a flare-when making a rubber mold don't try and solder it to the sprue wire)
Another way of getting your designs into a simple relief form is to take your drawing and text to a rubber stamp place where for about $12.00 they can scale it up or down and make you a rubber stamp with great detail from photo-polymers which can then be burned out and cast into metal to obtain a model. I've recently seen a photo-polymer system for jewelers for sale for about $ 350.00 for the kit
Many jewelers and artists use computers to keep track of all their business affairs. Spreadsheets have proven especially useful in keeping track of inventory, raw materials stock and performing costings on complex jobs. There are programs which can automatically reduce materials inventory by the correct amount as works are finished and then gives ordering warnings when specific levels of materials inventory are reached as well as spitting out daily job lists per worker against pending orders
A computer is only a tool but it is an information tool and as information can be tied to income it can serve a business well if used thoughtfully. For me personally the computer (and I do love my Mac) turned information into visual 'chunks' which I could duplicate, move around and compose with far more ease than before. I have memories of writing a paper with hundred of index cards on the floor moving them around and then typing them in. Another memory (all this only a couple of years ago) of typing my CV, getting to page 20 something and realizing I had to type the whole thing again carefully dreading any mistake. For this kind of thing the computer can't be beat. We've been able to put together a serious business proposal in a morning by cannibalizing parts of other documents.
The Future for Industry and Art School
It is likely that with decreasing prices for CAD/CAM systems there will be an increase in the number of models made with them. While machining methods will continue to be used this are to my mind a false route for small scale objects like jewelry. It is standard to use CAD/CAM and machining methods for large objects but I feel that this has at this point become a 'tradition' and that that has dictated the machining approach. It seems to me that stereo lithography and similar and perhaps even simpler future methods provide the best solution to jewelry scale problems. There are many ways of hardening substances, from freezing to using chemical reactions, spraying or precipitating materials, using heat and light. There will no doubt be various approaches to CAM developed
As the equipment is expensive there will be stereo lithography service plants established where models may be made using the customer's disc developed by them on their own home computers. The plant then produces the model for a fee.
While there are also now CAM centers for machining where one sends in one's disc to have the object made the machining approach would be more costly and more time consuming than stereo lithography or some of the other approaches being developed. This means that the machining approach is best in my mind for die making, steel dies for injection molding of plastic models for production and other tooling applications. The production of plastic or wax models directly will have more advantages for smaller shops.
This will allow individuals to be able to provide industry with models for jewelry production without having to have the technical skills necessary to making such a model in metal. It also has vast implications for the development of prototypes for industrial components by individuals. Free-lance industrial designers will have easy access to model making. An important employment niche opens here as does the possibility to influence industry's design level and willingness to take design risks.
The deliberate education of art students in CAD literacy has the potential to affect change in the sophistication of design that is acceptable to the North American buying public; the jewelry/metals consumer. This offers a direct and important opportunity to improve the level of sophistication in the public's acceptance of more sophisticated designs for jewelry
As art schools computerize in response to market pressures on graphic design, textiles and animation departments a unique opportunity arises for jewelry and metals departments to educate their students in CAD as well. Positioning in time is ideal for art school students to effect change in design in the industry through participation in it. It should be noted that an art school would not be churning out computer operators but rather placing computers as a tool for expression in the art school environment. Those for whom the computer is the right tool would gravitate to it; most people would continue on in standard metal education-computers are not the right instrument for everyone. But for those for whom it is the right tool the environment of an art school may provide them with different ways of approaching computer use and eventually software design
You will at some point see a computer catalog where scanned parts or photos of parts can be cut and pasted on each other, then printed out to show customers various combinations. Later on the choice will be made in your shop by the 3D prototyping system you have. There would-be, if you like, a kind of direct link between customer and manufacturer-something that does not exist often in the current jewelry trade. Many more jewelry stores will be able to 'manufacture' on site and it will change some of the work that shop wax carvers do. Professional CAD operators with their own equipment will emerge to supply industry's needs; free-lance and salaried designers both
There are also implications for sculptors; at some point scale will not be an issue, you will design it small, enlarge it on the computer, have the milling machine, or spray or extruder make the object. Like the printing industry experience where the new capabilities foisted on technicians made for a lot of bad design for a while until the technicians either got better artistically or gave the equipment over to designers with art training this may result in a lot of bad sculpture at some point for a while.
The Future for Artist Jewellers and CAD/CAM Systems
The Tyler program had chosen a machining approach to CAD/CAM. Stanley Lechtzin when asked in 1991 or so estimated that perhaps twenty artists would be using the system in the US by the end of the century. My suspicion is that it will a lot more than that. The system as used now would cost around $ 37,000.00 and require tooling and machine tool set-up experience. This approach in his view would result in a few individual artists using these systems in their work and in some people from the program becoming part of the industry as already happens to many graduates. I feel it is more useful to educate the student in basic computer use (word processing, basic spreadsheet) and in drawing and CAD programs so as to allow them to be positioned the as well as possible for free choices later in life. If one learns one CAD system then other systems will be related enough to learn them as required. With the advent of desktop three-D prototyping and CAM service companies more opportunities open for those students for whom the computer was an appropriate tool. Judging from the web site this in fact is what seems to be happening with several students working only with designs on the computer and not worrying too much about making them.
In Conclusion
The stereo lithography approach and other similar non-machining methods will become more accessible as time passes. An individual educated in CAD use for designing and rendering would be equipped for the advent of remote CAM centers to design for themselves or industry and to use their rendering skills in a variety of ways. They would also be able to access both machining and stereo lithography services. At a certain point they will be able to work for findings and wax companies designing models for publishing on disc or even publishing and selling their own designs to jewelry shops as independents. Therefore it is more logical for the widest future options to educate in terms of CAD systems in combination with a good general jewelry skills and design issues education
What will be coming is a day when on most jewelry store desks there sits a computer, screen and 3-D prototyping machine. The store owner slips a CD into the computer and shows the customer various rendered models of rings or jewelry. The stone's colors, shapes and sizes can easily by altered from the keyboard. Heads can be exchanged with a quick mouse click on a menu of photographic choices from the suppliers line. Various models can also be quickly chosen from images on a menu. The jewelry piece can be rotated and looked at from any view on screen. A color printout of the rendered jewelry piece can be handed to the customer.
'Virtual reality' glasses and a control glove would allow the customer to 'pick up' the jewelry, 'hold' it in their hands while looking at it and turning it around, see a close up view and so on. If the store has not yet bought the code for that particular model or combination a quick call is made to the issuing company's phone number or internet web site address, the model number typed in and an access code given. The jeweler then types that in and the 3-D prototyping system quickly turns out a finished wax model ready for burnout in the customer's size. And that even before they come out with machines that turn out the finished gold jewelry ready for setting.
You assume all responsibility and risk for the use of the safety resources available on or through this web page. The International Gem Society LLC does not assume any liability for the materials, information and opinions provided on, or available through, this web page. No advice or information provided by this website shall create any warranty. Reliance on such advice, information or the content of this web page is solely at your own risk, including without limitation any safety guidelines, resources or precautions, or any other information related to safety that may be available on or through this web page. The International Gem Society LLC disclaims any liability for injury, death or damages resulting from the use thereof.

Charles Lewton-Brain
Master goldsmith Charles Lewton-Brain trained, studied and worked in Germany, Canada and the United States to learn the skills he uses. Charles Lewton-Brain is one of the original creators of Ganoksin.
Related Articles
Master Metalsmith Miyé Matsukata
How to Make a Plique a Jour Fairy
John Iversen: Carved Color
A Hard Metal for Delicate Jewels
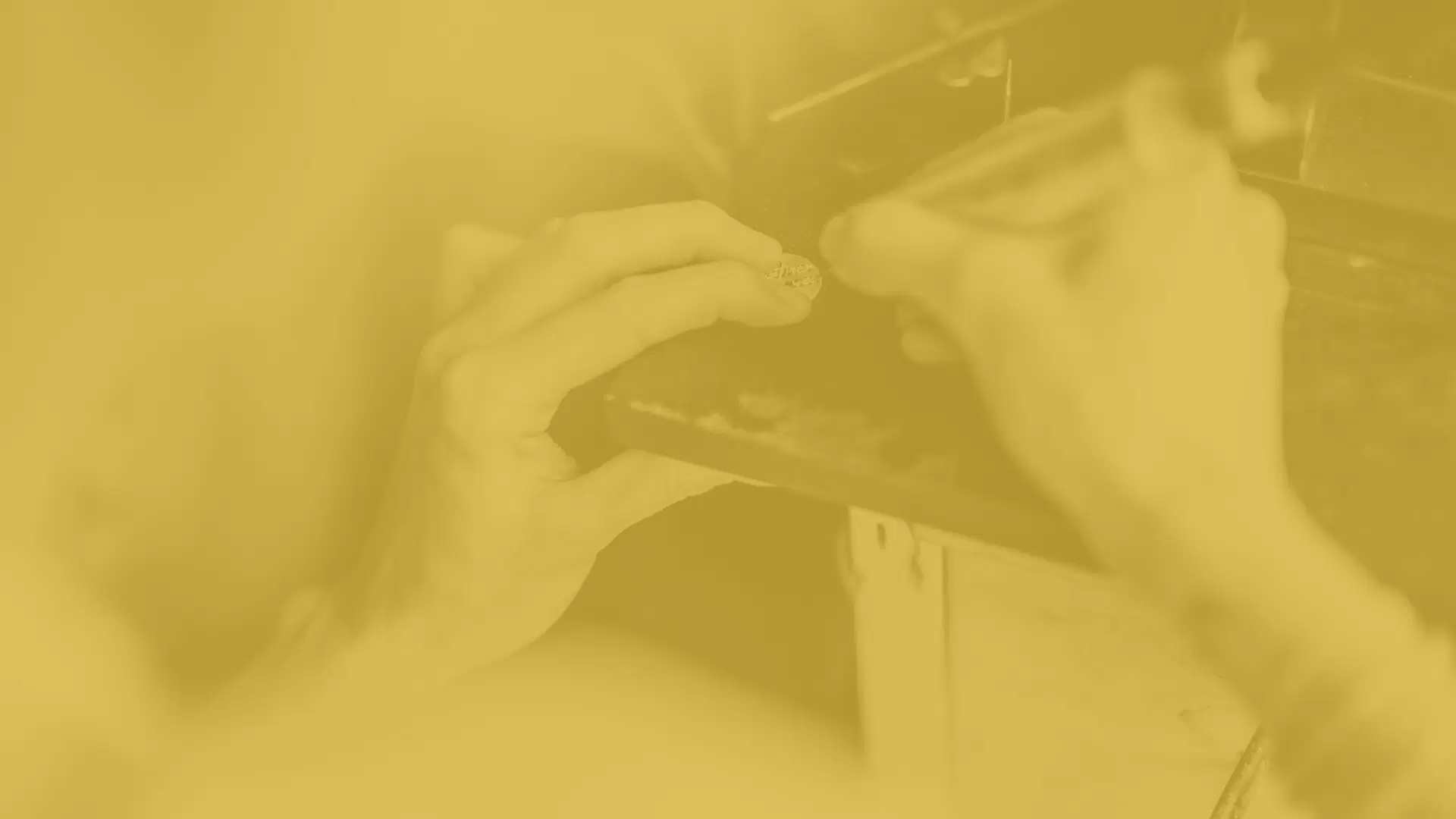
The All-In-One Jewelry Making Solution At Your Fingertips
When you join the Ganoksin community, you get the tools you need to take your work to the next level.
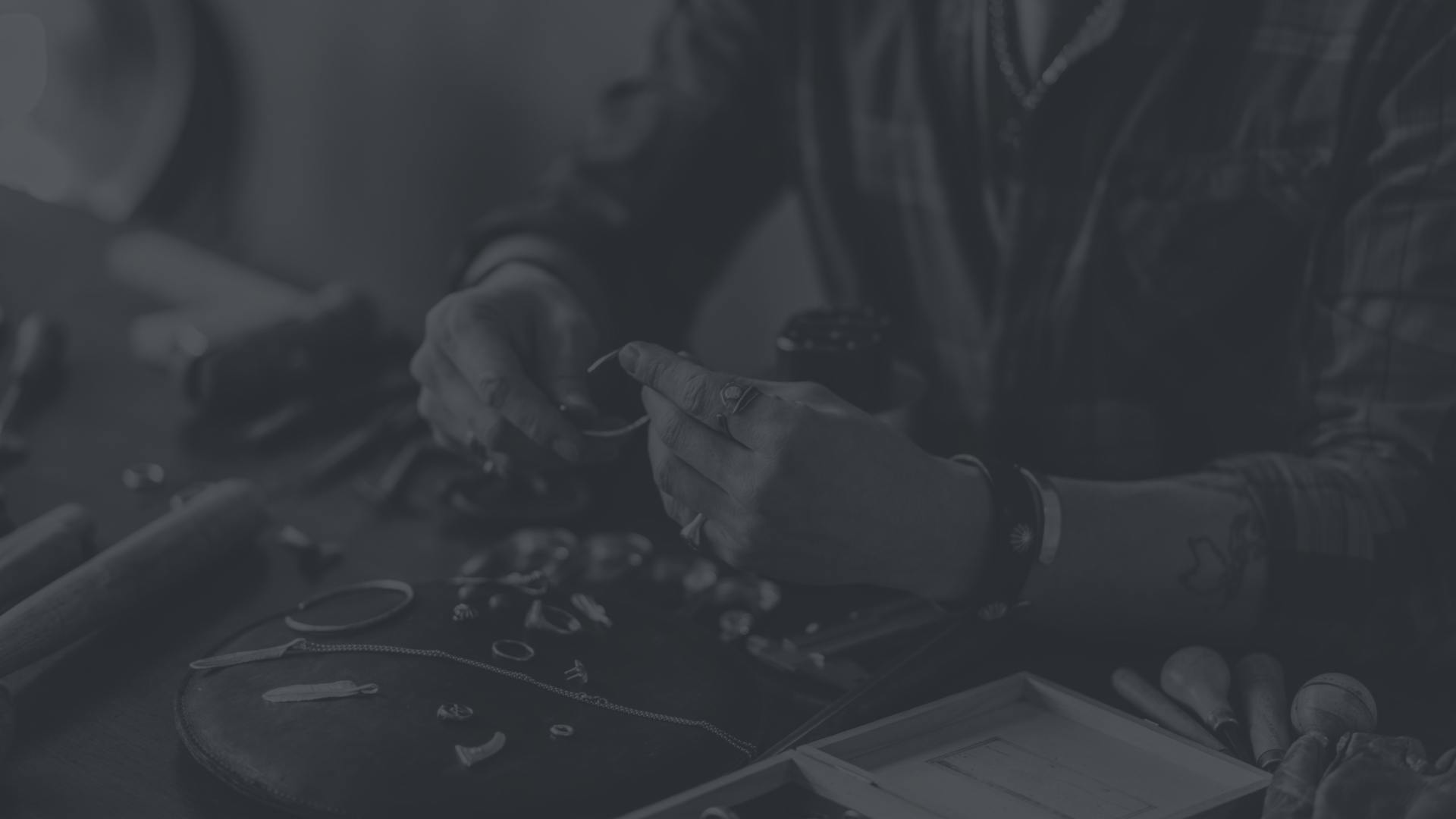
Trusted Jewelry Making Information & Techniques
Sign up to receive the latest articles, techniques, and inspirations with our free newsletter.