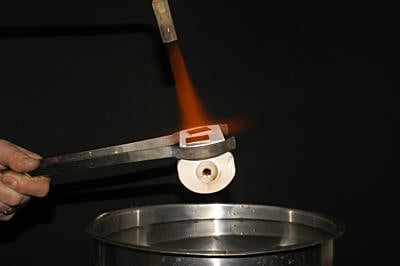
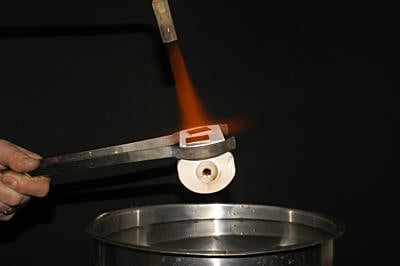
Heat Treating Metals
Heat treatment changes the microstructure of a metal or alloy. It is a process that may be applied after casting, or during or after fabrication. Since mechanical properties, such as strength, ductility, hardness, and toughness, and chemical properties, such as corrosion resistance, are in part dependent on microstructure, heat treatment can have a profound effect on them. There are a variety of reasons for heat treating gold, including, but not necessarily limited to, the following: To ease polishing, reduce wear and damage on the finished surface, increase strength, and increase corrosion resistance. Heat treatment can also be used to increase ductility after work hardening or to impart a springy quality to components such as money clips, catches, and clasps..
13 Minute Read
When I first heard the phrase "disorder to order transformation" during a conversation about heat treating metals, I must have been hungry. My preoccupied mind plucked the words from the context of the metallurgical lexicon and applied them to my kitchen, which goes from a disorderly state thanks to my kids' lunch efforts to a very orderly state as I prepare to embark on one of my frequent culinary ventures.
And, like "heat treating" a raw cut of filet mignon to transform it into a delicious dinner, heat treating metals—particularly gold alloys—can make them more delectable to work with, in this case by improving their hardness. This fairly simple procedure can add years of life to your products—without adding much time or expense to your current processes.
Photo by Gary Dawson |
I first discovered the wonders of heat treating when I was preparing a presentation on the topic for the 2004 Kraftwerks, held at the PM West/Fine Gold factory in Ontario , California . Although I hadn't actually used heat treatment much to harden metal in my shop, I had probably annealed metal nearly every day during my 30 years as a goldsmith. What could be the big deal about going the other way, I thought. Ah, the bliss of naiveté.
It was somewhat comforting to find that I wasn't alone as I observed the reactions to my presentation at Kraftwerks. Not only did I have to pitch the technique, but I also had to pitch my presentation to get anyone to attend. One of the first attendees, not yet settled into staying for the talk, asked what it was about. When I gave him the overview, he said, "Heck, I've been making jewelry for 20 some-odd years. I've never heat treated, and I've never had any problems." That was not an atypical reaction…and it was not unlike my own, prior to delving into the topic.
The research I did for the presentation opened up a new world of perspective for me. I know that there's no faithful like the recently converted, but I truly believe that heat treatment may be one of the most underutilized techniques in jewelry manufacturing. So bear with me for a little interesting science, and then reap the rewards in your own shop.
What is heat treatment?
Heat treatment (in this context) changes the microstructure of a metal or alloy. It is a process that may be applied after casting, or during or after fabrication. Since mechanical properties, such as strength, ductility, hardness, and toughness, and chemical properties, such as corrosion resistance, are in part dependent on microstructure, heat treatment can have a profound effect on them.
There are a variety of reasons for heat treating gold, including, but not necessarily limited to, the following: To ease polishing, reduce wear and damage on the finished surface, increase strength, and increase corrosion resistance. Heat treatment can also be used to increase ductility after work hardening or to impart a springy quality to components such as money clips, catches, and clasps.
How does the process work?
In "Heat Treatment of Precious Metals and Their Alloys," a paper presented at the 1991 Santa Fe Symposium, metallurgical consultant Mark Grimwade of Middlesex , England , offers a thorough scientific explanation of heat treatment. He writes that heat treatment falls into one of three categories: homogenization after casting, annealing, and age hardening (precipitation hardening or disorder to order transformation).
Since homogenization after casting is primarily used to improve workability in non-jewelry alloys, I will not discuss the process in this article. Instead, I'll focus on the two heat treating categories applicable to jewelry manufacturing: annealing and age hardening.
Although annealing may seem like second nature to most jewelry makers, grasping the science of the process is a necessary building block to understanding age hardening—the process that has opened my eyes to what a big difference a little heat can make in the durability of my work.
Annealing
This is a process most often used to restore ductility to work-hardened metal. Its relative familiarity to jewelry makers may make it seem pointless to discuss; however, there are some quirks, interesting facts, and a few tricks that may help you better understand the process and its role in heat treating objects to increase strength and hardness.
The annealing process can be divided into three main stages of increasing temperature: recovery, recrystallization, and grain growth. The process begins with a cold-work-hardened piece. As the temperature is initially raised in the recovery stage, there is very little change in the structure of the metal or its ductility, but small changes in cell boundaries can be observed under very high magnification. Heat treating in this temperature region can result in a reduction of residual or internal stress levels by a process of stress relaxation. Residual stresses are those introduced by non-uniform working or by non-uniform heating and cooling.
To put it in shop terms, many goldsmiths perform the process of stress relaxation prior to doing a traditional sizing to eliminate "spring outs"—my term for when a prior sizing seam hits the flow temperature of the solder used and the tension of any size adjustment by hammer flings the old sizing across the room. Conveniently, heating in this range allows one to locate any prior solder seams.
To achieve full annealing, the temperature must be high enough for the recrystallization stage to occur. At this stage, ductility increases to a much higher level. Cells or crystallites that occur where localized strain has been highest act as nuclei and start to grow at the expense of the surrounding material to produce new, small, strain-free grains. Growth of these new grains continues until the more fibrous structure of work hardening is replaced by this new microstructure.
As grains continue to grow in the final stage of the annealing process, ductility peaks. If annealing goes on for too long, though, grains grow at the expense of others. Gross over-annealing can lead to the "orange peel" effect of exceedingly large grain growth.
Factors that may influence the stages of the annealing process include alloy composition, the amount of cold work to which the metal had been subjected, temperature, and time. Some important things to remember about annealing are the following:
- At least some cold work is required before nucleation and recrystallization can be effective. For pure metals, about 2 percent strain is necessary. Cold work increases the number of nuclei, which results in a smaller recrystallized grain size. Therefore, products should be given a minimum of 50 percent to a maximum of 75 percent reduction between annealings, since finer grain materials tend to have better mechanical properties.
- Temperature changes have a greater effect than time on recrystallization. Per Grimwade, in practice, if annealing is done in a furnace, the recommended times are typically around 30 minutes. Torch annealing at the bench requires slightly higher temperatures because times are much shorter.
- Colored golds should be quenched for a full anneal. Nickel white golds should not be quenched directly, but instead either cooled on a steel plate or cooled to about 550°C/1,022°F and then quenched.
- High palladium alloys should be quenched directly for optimum ductility.
- When fully annealing nickel white golds, stress relieve the alloys first by slow heating to about 300°C/572°F. Stress relieving prior to fully annealing at about 750°C/1,382°F prevents fire cracking.
In theory, furnace or kiln annealing should produce the most ductile material, since one should be able to control the time and temperature much more effectively. That may be the case in many production shops, but as a matter of practical application, I have found that torch annealing can sometimes be much more effective in my shop, depending on the mass of the material being annealed.
My shop is primarily a custom studio, with more attention to one-off products than line production, so fabrication and annealing are usually done on fairly small pieces of material. The small mass of many of the objects seems to allow them to cool significantly enough between the kiln and quench water to make a difference, making the process less effective for reasons that will be explained later in this article. However, when torch annealing, I can actually follow the material with the torch from the heating platform right into the quench water, and therefore maintain annealing temperature right into the quench.
Age Hardening
The term "age hardening" is often used interchangeably with precipitation hardening, but it can also work as a disorder to order transformation. To understand the process, start by visualizing precipitation hardening.
Think about a two-component alloy, metal A and metal B. Upon melting and then cooling to room temperature, the alloy passes through two distinct phases of saturation. The first is near the stage of solidus, when the alloy is just becoming solid. It is at this higher temperature that metal A is more soluble in metal B, and particles of both metals are arrayed such that they can be seen under magnification to form large, regular grains. This state is referred to as a single-phase solid solution.
As the temperature continues to fall, at some point a limit of solid solubility of A into B is reached, and a second phase begins to precipitate out; particles gather both at the grain boundaries and within the grains of the first phase. As the temperature continues to fall toward room temperature, the size and number of these precipitate particles increases, with the final structure consisting of relatively large particles of the second phase in a matrix of the first phase.
If the cooling is arrested (by quenching) prior to second phase formation, a single-phase structure can be retained as a super-saturated solid. The same effect is observed if a cold-worked or even fully annealed alloy is "solution treated" (the process of heating the metallic alloy to the temperature just below solidus) and quenched, leaving the alloy in its most ductile state.
If this solution-treated, quenched alloy is later heated to a relatively low temperature for a suitable time, a second phase can be forced. This process is known as age hardening, which results in an increase in strength and hardness. There is a limit to the effectiveness of this treatment, however, and a condition known as over-aging can be achieved if aging conditions persist for too long.
How can I put age hardening to use in my shop?
There are three alloy systems important to the jewelry industry that can be age hardened in this manner: sterling silver, gold/titanium alloys, and the ternary system of gold-silver-copper.
Sterling Silver. It is recommended to solution treat sterling silver at 750°C to 760°C/1,382°F to 1,400°F for 30 minutes, quench immediately, and age for one hour at 300°C/572°F. The hardness of the sterling alloy can be effectively doubled with this process, from HV 60 in the fully annealed state to HV 120.
The only problem posed by this process is that the solution treatment temperature is above normal soldering temperatures for sterling, so only articles with no solder can be treated. Soldering after hardening sterling will over-age the material dramatically to the point of nullifying the hardening effort.
Gold/titanium. The alloy in this category particularly suited for age hardening is 990 Gold, an alloy of 99 percent Au and 1 percent Ti. It is recommended to solution treat the alloy at 800°C/1,472°F, quench, and age for one hour at 500°C/932°F. (Note: This system re-quires treatment in an argon or suitable molten salt bath to prevent contamination of the Ti.)
Gold-Silver-Copper. This ternary system is the basis for the majority of colored golds used in the jewelry industry. It is within this system that we may become familiar with the principle of disorder to order transformation. The process used to gain a disorder to order transformation is similar to that for precipitation hardening in that it involves solution treatment, quenching, and age hardening, but the mechanism is different.
To help visualize the process of disorder to order transformation, we need to begin by looking at the binary system of Au-Cu and the difference between weight percentage values and atomic percentage values. For example, in an 18k red gold composition of 75 weight percent Au/25 weight percent Cu, there is a mass difference between the two materials such that the atomic percentages are 50 percent Au/50 percent Cu. That is, for every gold atom there is a corresponding copper atom. This serendipity results from the relative atomic weights of gold and copper. (These figures are not valid for the 18k Au-Ag green gold system.)
At high temperatures, the equal numbers of gold and copper atoms are randomly sited in the lattice of the solid solution; this is known as the disordered state. Upon cooling below 410°C/770°F, the atoms rearrange themselves through diffusion to a regularly spaced, ordered solid solution.
The beauty of this is twofold. First, in the ternary Au-Cu-Ag system, the transformation from disordered to ordered state occurs within the same process as precipitation hardening…that is, the transformation from disordered to or-dered state occurs when the alloy is cooled slowly from the annealing temperature, but it may be suppressed by quenching from above 410°C/770°F. Age hardening in the range of 150°C to 300°C/302°F to 572°F then causes the ordering reaction to take place, producing hardening effects with both precipitation and disorder to order transformation.
Second, ordering is found to occur in alloys having relatively simple atomic Au-Cu ratios, such as 1:1 and 1:3. Therefore, some 9k to 14k alloys respond very favorably to age hardening.
A few important things to remember when age hardening include the following:
- Copper-containing karat golds in the range of 8k to 18k can be hardened.
- Quench after annealing above 550°C/ 1,022°F for 18k and 650°C/1,202°F for 9-14k colored gold alloys to produce a fully annealed state.
- Solution treatment for colored golds is below soldering temperature, so fabricated products can be hardened.
- Solution treatment for many alloys is below the temperature at which damage occurs to many gemstones, so setting can be done in the annealed state before hardening, producing a more secure stone setting.
- Some casting alloys (especially those containing zinc) may adversely affect the ability to age harden a material.
- White golds containing low amounts of palladium harden to a minimal degree.
- Usually, white golds containing high amounts of palladium can be hardened more than low palladium alloys because they contain more copper.
What equipment is required for heat treating?
The most basic heat treating can be achieved with nothing more than a torch, but due to the relatively precise temperature controls necessary, a furnace with a kiln-minder or thermocouple is advised. One relatively simple alternative is a salt bath, wherein a composition of salts (covering the temperature range of 160°C to 1,200°C/320°F to 2,192°F) are contained in a heated iron pot. The additional benefit of salt bath usage is that it prevents oxidation or contamination of titanium in the high-gold-content 990 alloys. Safety hazards posed by this method require the use of protective clothing and facemasks.
In addition, it's important to always quench in water, not pickle. This is particularly true if there is any chance that the alloy will be milled or rolled after quenching. Since all alloys have micro-porosity or microcracking, quenching in pickle will draw the acid pickle into the metal body. Rolling squeezes the acid out onto the rollers of the mill, which eventually produces craters that prevent the creation of smooth milled products.
Why haven't I tried this before?
The claim I made in the opening section of this article that heat treatment may be the most underutilized technique in the industry may have been brash. Perhaps the technique is utilized more than I am aware. After all, we certainly know that at least some boutique and specialty alloy designers have cashed in on the benefits of age hardening. Some of the sculptural designs in the marketplace today probably wouldn't work without heat treatment.
That being said, my experience as one of the newly converted trying to spread the gospel of precipitation hardening and disorder to order transformation leads me to believe that there is a huge segment of the working goldsmith/manufacturer population that could benefit from approaching this technique. And while it is true that some metallurgists have made a lifetime of studying the pure science of age hardening, the learning curve for practical application of this method is really not that steep.
With so much to gain from such little effort, you too may want to move the disorder to order cycle out of your kitchen and into your shop. Good luck!
The award-winning Journal is published monthly by MJSA, the trade association for professional jewelry makers, designers, and related suppliers. It offers design ideas, fabrication and production techniques, bench tips, business and marketing insights, and trend and technology updates—the information crucial for business success. “More than other publications, MJSA Journal is oriented toward people like me: those trying to earn a living by designing and making jewelry,” says Jim Binnion of James Binnion Metal Arts.
Click here to read our latest articles
Click here to get a FREE four-month trial subscription.
You assume all responsibility and risk for the use of the safety resources available on or through this web page. The International Gem Society LLC does not assume any liability for the materials, information and opinions provided on, or available through, this web page. No advice or information provided by this website shall create any warranty. Reliance on such advice, information or the content of this web page is solely at your own risk, including without limitation any safety guidelines, resources or precautions, or any other information related to safety that may be available on or through this web page. The International Gem Society LLC disclaims any liability for injury, death or damages resulting from the use thereof.
Related Articles
Gold Jewellery Tarnishing
Richard Reinhardt: Discontinuous Continuity
Creating Colorful Jewelry Designs
Platinum Alloy Applications for Jewelry
The All-In-One Jewelry Making Solution At Your Fingertips
When you join the Ganoksin community, you get the tools you need to take your work to the next level.
Trusted Jewelry Making Information & Techniques
Sign up to receive the latest articles, techniques, and inspirations with our free newsletter.