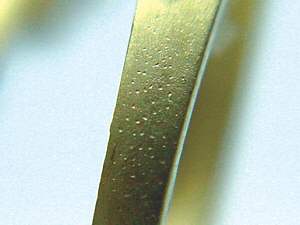
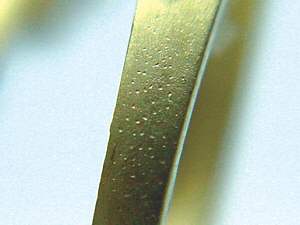
Identifying and Preventing Wax Defects
Manufacturer spend much time and money diagnosing defects that are believed to originate in the casting process, but actually occur during waxing. Many companies run in circles, changing this gate/sprue, that metal, these temperatures, and screaming at suppliers to try to fix the 'mystery' problem. While these areas certainly can be the source of problems, many defects are misdiagnosed as casting defects, and thousands, perhaps millions, of dollars are wasted in search of non-existent flaws in the casting process.
13 Minute Read
In any kind of manufacturing, there are defects in materials, process, or products that need to be corrected. But the final rework stage is one of the most costly labor steps in jewelry manufacturing, and so it is the last place you want to correct such defects.
Ideally, problems should be prevented early in the process, rather than fixed at the end. Of course, in order to prevent them, you must know what causes them. And that's not quite as simple as it sounds.
For casting, in particular, manufacturer spend much time and money diagnosing defects that are believed to originate in the casting process, but actually occur during waxing. Many companies run in circles, changing this gate/sprue, that metal, these temperatures, and screaming at suppliers to try to fix the "mystery" problem. While these areas certainly can be the source of problems, many defects are misdiagnosed as casting defects, and thousands, perhaps millions, of dollars are wasted in search of non-existent flaws in the casting process.
I see it all the time. When company leaders call me to help them overcome quality issues, the first thing I do is visit their Quality Assurance (QA) department to examine what their inspectors are labeling as defects. I make notes as to the most likely cause, based on my years of experience with these issues. Then I start working backwards to what I believe is the source, and beyond. Finally, I take the results of my reconnaissance mission and compare my notes to the QA department's notes.
In nearly 100 percent of cases, we agree on the presence of a defect. But what is discovered as the origin of the defect and recorded by the inspectors is accurate in less than 20 percent of the cases.
In this article, we will focus on defects that originate in the wax department, an area that is often overlooked. Once identified correctly, these problems are usually simple to fix, saving you money immediately.
Air Bubbles
Bubbles under the surface of the wax appear either when air is injected into the mold along with the wax, or when air in the mold is trapped during the wax injection process. In either case, these air bubbles can pop when the casting investment is vacuumed. When the bubbles pop, the void fills with the investment slurry. Later, the metal fills around these investment formations and presto-investment inclusion defects. They most often appear as small rounded holes in the castings.
You can inspect waxes for the presence of bubbles by holding them up to a small table lamp and looking through them. Light spots indicate bubbles in the wax, although how easy it is to see them will depend on the "readability" of your wax. You can then repair these bubbles by popping them with a heated wax tool and filling the exposed hole with wax. Due to the flow dynamics of wax in a mold, these defects will tend to show up in approximately the same places on all your waxes or castings of the same style.
A better solution, however, is to eliminate the source of the bubbles whenever possible. How that will be accomplished depends on whether the air is being trapped during the wax injection process, or whether it is being introduced with the wax.
Trapped Air
Air must be able to escape the mold at an equal, or faster, rate than the wax being injected or it will be trapped. These types of trapped air bubbles can be reduced or prevented by the proper application of powder in mold vents, which allows air to escape from the mold cavity during injection. It is also possible to reduce trapped air in molds by reducing injection pressure and slowing the injection rate.
Air can also be trapped in molds if the wax must flow backwards in a turbulent fashion to fill the pattern, due to way the model is gated. This type of gating configuration can cause problems in casting as well.
Introduced Air
Bubbles that are introduced into the mold along with the wax can come from several sources. One source is dissolved gas in the wax. Another is air that becomes trapped when new wax chips or dots are loaded into the wax pot: If small air spaces between the cold wax chips are covered over by a molten surface before the air can escape, it is possible for these tiny bubbles to remain trapped until they are injected into the molds.
A good way to overcome these types of challenges is to pre-melt wax in a reservoir unit and vacuum de-gas it before loading it into production wax pots. You will need a transparent lid with an airtight seal that has a fitting for a vacuum line, and a separate vacuum release valve. If you don't have these resources, it is possible to vacuum de-gas production pots. Just remember to isolate the pressure gauge on the wax pot during the vacuum de-gas process. (To do so, install a small ball valve between the gauge and the wax pot, and close the valve before starting the vacuum pump.) Also, never de-gas a full wax pot, or you will likely end up with wax in the vacuum hose.
Another source of introduced air that causes bubbles in wax is water vapor from condensation in compressed air lines. The pistons of an air compressor heat up during use, warming the air. This warm, humid air travels along the air pipes into the often air-conditioned wax injection room. The pipes are cooler in this room, so the water vapor condenses and collects. This water eventually makes its way into the wax pot, where it will provide hours of air bubble repair enjoyment. To avoid this problem, you need dry the air that is going to your wax pots. The use of line dryers, desiccant dryers, or a combination of the two is highly recommended.
Under certain conditions, automatic vacuum wax injectors can cause bubbles in waxes. This is a source that most manufacturing companies don't consider and wax pot manufacturers don't want to discuss. Tool suppliers might tell you that a new automatic vacuum wax injector will cure your wax injection problems and increase your production. It would be more accurate to say that a well-engineered, properly aligned and maintained, auto-clamp, vacuum wax injector can help produce waxes of consistent high quality and weight if used with properly prepared molds.
Automatic vacuum wax injectors can produce more consistent waxes in general than waxes shot by hand or conventional wax pots because the parameters are easier to repeat. In other words, once you establish the proper combinations of wax injection pressure, clamp pressure, and forward force against the nozzle for each mold or mold group, automatic wax injectors can increase your production through decreased rejection rates.
But these vacuum wax injectors can also help your operators create bubbles in the waxes. Most of these machines draw vacuum through the injection nozzle in order to remove the air from the mold. However, if you are shooting a mold designed for traditional wax injection pots-one that is vented and powdered, for example-the vacuum injector simply draws in air through the vents. (The same problem occurs with unvented molds that do not make a complete seal on the injection nozzle.) If there is an air leak of any kind, there is nothing gained from the vacuum stage of the injector's process.
In addition, during this stage, some air will be drawn through the molten wax in the injection nozzle. Small bubbles are trapped in the wax, and are then injected into the molds with no chance of escaping.
Three Pressures
An inadequate escape route for air during wax injection can also cause the wax pattern not to fill completely. When this occurs, one defect may well lead to others: The pattern doesn't fill, so the worker turns up the injection pressure. The injection pressure is so high, the worker must apply higher clamping pressure on the mold to keep the wax from leaking out the sides. And the list goes on.
The improper combination of these three pressures-injection, clamp, and forward pressure-is usually associated with non-fills and seams, but it can also add to the wax bubble problem. Too much forward pressure can cause the mold to split at the injection nozzle, allowing air into the wax stream. Because of this tendency of the mold to split, additional clamping pressure must be applied to keep the wax from leaking. This additional clamp pressure can trap air in the mold by closing off small vents.
This kind of defect is more commonly associated with hand wax injection because of its variable nature. Being able to avoid this problem is a plus for auto-clamp wax injectors. Auto-clamp systems allow you to discover, document, and repeat the ideal pressure combinations, permitting you to eliminate the three pressures from the defect source search relatively easily
Powder and Silicon Spray
Part of the wax department training that is often incomplete is the proper use and application of powder and silicon spray for rubber molds. Silicon sprays are used as lubricants or mold release agents to facilitate easy, distortion-free removal of the wax from the rubber mold cavity. Powder is used to create a microscopic path for the air in the mold to escape through the air vents during the injection process. Each of these products must be used correctly for best results.
Ideally, the powder used to allow air to escape the mold is very fine and organic (burnable), such as cornstarch or rice flour. Talcum powder is commonly used in the wax injection areas of the jewelry business because it is not as susceptible to humidity as cornstarch. However, talc is a mineral and does not burn out if it gets on or in the wax. Because it is lighter than metal, it floats to the surface of the molten metal stream and causes a grainy, rough surface on the casting.
Worse yet, many factories allow talcum powder to be applied with a "powder hammer," a piece of cloth wrapped around the talcum powder and tightly bound with string or rubber bands. Not only does this "tool" indiscriminately apply powder throughout the mold cavity, it also applies whatever dirt or foreign matter happens to be on the table where it is laid.
Another potential problem is the misuse of silicon mold release sprays. I have been to factories where the liberal application of powder is immediately followed with a good dose of silicon spray, or vise versa. The powder in the mold cavity traps or absorbs the liquid of the silicon spray, making a positive formation in the mold cavity. When the mold is injected, the wax will flow over and around these formations of wet powder, resulting in a pitted surface. In extreme cases, it can have an appearance that is similar to investment erosion or spalling.
These wet powder formations usually remain in the mold when the wax is extracted, and duplicate the same surface defect over and over if not removed. Even if the clump of wet powder stayed with the wax when it was pulled from the mold, it would likely be washed out during the investing process and show up as a negative space in the casting surface.
Just the overuse of silicon mold release spray can also produce surface defects. These defects appear as smooth, rounded, irregular-shaped negative spaces in the casting surface. They are caused by injecting wax into the mold cavity before the mold release spray has had time to dry. The wax pushes the droplets around, but ultimately forms around the droplets. I have seen this defect incorrectly identified as gas porosity several times.
To reduce the occurrence of powder- and mold release-related problems, make sure rubber molds are handled correctly. First, switch to cornstarch or rice flour, which will burn out cleanly if it accidentally gets onto the wax. To overcome the humidity issue, keep the powder in a sealed container when not in use, and keep a small porous packet of desiccant in the container. Just don't forget to replace or regenerate the desiccant packet from time to time.
When applying powder, apply it only to areas where the wax and the powder will have minimal contact. While bending the mold so that the vents are open, apply a light dusting of powder into the vent areas of the rubber mold using a small soft brush. Use a compressed air gun with "dry" air to blow out the excess powder.
Release the tension on the mold so that the vents close, then spray with a very fine, light mist of a silicon mold release agent. Be certain that the spray you use has a very fine spray mist. Avoid sprays that spit larger droplets onto your molds.
Cleanliness is also critical. Install regular inspection and cleaning procedures for rubber molds. Keep workstations and wax trays clean and free of contaminants that could get in or on the waxes. While this type of contamination may not cause problems with the metal itself, it causes surface defects, increasing the work time needed to obtain a level, smooth surface on the casting. In addition, because eliminating surface defects requires the removal of metal, it increases the rate of metal loss, and increases the possibility of working down to subsurface porosity, resulting in more repair work.
Wax Tree Defects
Another source of defects is the wax tree. One of the most important issues here is the quality of the connection between the gate and the sprue. (The gate is the part connecting the jewelry wax piece to the central trunk of the wax tree. The sprue is the central trunk.)
The gate/sprue connection (filet) should be sealed and smooth all the way around. A common mistake people make is using a wax pen to melt a hole into the sprue and inserting the gate into that molten wax spot. This method leaves sharp inward angles or points in the wax, which will turn into sharp brittle pieces of investment that can break off during casting. When they do, they are pushed to the outside of the mold cavity because of the difference in density between the metal and the investment.
The wax pen can be used to create a filet around the base of the gate/sprue junction to avoid this potential inclusion situation. But a better solution is to use a small melting reservoir and sticky wax to do this job faster and reduce the chances of a defect. (Thanks to Eddie Bell of The Bell Group/Rio Grande, who showed me this trick years ago.) You still need to seal around the base of the gate/sprue to create a smooth filet, but the sticky wax supplies some material to create the filet with, as well as making the tree building function much faster.
Even using sticky wax, you'll still need to use the wax pen to seal the parts. When you dip the end of the wax gate into the sticky wax, the travel time between wax reservoir and sprue can allow the surface of the sticky wax to cool slightly. When this happens, unsealed gates sometimes snap off the sprue wax. To avoid this problem, pick up your wax pen once per row or column, and seal them.
Fixing Your System
Knowing that you have defects is easy. Knowing where the defect really comes from and how to fix it can be challenging, especially when there are several stacked causes. It isn't enough to fix some of the problems. You must fix them all.
For consistent results, you must go through your system continually to reduce or eliminate all the possibilities that can cause these types of defects.
The good news it that none of the defect prevention measures described in this article are difficult to implement. I have often observed that causes of the problems I am called in to solve are relatively obvious and may have been noticed before. But because the defects have grown slowly over time, or the workers were too busy, the problem reached a critical point. The practices that are causing the problem have become "normal" and go unrecognized or forgotten. By questioning everything and forcing yourself to become aware of all potential problems, you can stop them well before they reach the rework stage.
The award-winning Journal is published monthly by MJSA, the trade association for professional jewelry makers, designers, and related suppliers. It offers design ideas, fabrication and production techniques, bench tips, business and marketing insights, and trend and technology updates—the information crucial for business success. “More than other publications, MJSA Journal is oriented toward people like me: those trying to earn a living by designing and making jewelry,” says Jim Binnion of James Binnion Metal Arts.
Click here to read our latest articles
Click here to get a FREE four-month trial subscription.
You assume all responsibility and risk for the use of the safety resources available on or through this web page. The International Gem Society LLC does not assume any liability for the materials, information and opinions provided on, or available through, this web page. No advice or information provided by this website shall create any warranty. Reliance on such advice, information or the content of this web page is solely at your own risk, including without limitation any safety guidelines, resources or precautions, or any other information related to safety that may be available on or through this web page. The International Gem Society LLC disclaims any liability for injury, death or damages resulting from the use thereof.
Related Articles
Cracks in Jewelry Manufacturing
Production Methods for Palladium Chain Making
Production Project Proposal
Perfect Finishing Tools and Techniques
The All-In-One Jewelry Making Solution At Your Fingertips
When you join the Ganoksin community, you get the tools you need to take your work to the next level.
Trusted Jewelry Making Information & Techniques
Sign up to receive the latest articles, techniques, and inspirations with our free newsletter.