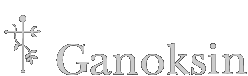
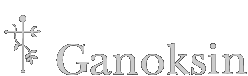
Metal Corrugation Vocabulary
Metal corrugation is a unique roll-formed process whereby a precise and specific repetitive surface pattern is achieved when processing thin gauge annealed 36 -24 sheet metal or wire. Metal is processed using special tools manufactured with corresponding matching and enmeshing fluted gears that are aligned in such a manner so that the crest of one roller fills the trough of the other. Metal corrugation is a unique process NOT to be confused with the fold-forming techniques studied and highly developed by Charles Lewton-Brain..
11 Minute Read
This article offers the width of appropriate metal corrugation vocabulary and terms to serve as a guide to metalsmiths and non-metalsmiths alike.
Corrugation
The act of contraction into repetitive wrinkles or alternate ridges and grooves. When studying nature forms, corrugation is regularly seen adding innate strength to what might be otherwise considered a frail form. Corrugation has been adopted by industry and used in utilitarian fashion for the manufacture of common objects we regularly see such as packaging materials as well as industrial applications such as roofing, siding, and drainage pipes.
Metal Corrugation
Metal corrugation is a unique roll-formed process whereby a precise and specific repetitive surface pattern is achieved when processing thin gauge annealed 36 -24 sheet metal or wire. Metal is processed using special tools manufactured with corresponding matching and enmeshing fluted gears that are aligned in such a manner so that the crest of one roller fills the trough of the other. Metal corrugation is a unique process NOT to be confused with the fold-forming techniques studied and highly developed by Charles Lewton-Brain.
Terms and Components of Metal Corrugation
- Crest: The peak of the corrugated ridges.
- Pitch: The distance measured between the center point of two adjoining crests.
- Trough: The bottom of the corrugated groove.
Understanding the Strength and Fragility of Metal Corrugation
Corrugation adds an amazing inherent strength to thin materials running with the linear dimension of the corrugated pattern. This factor enables one to use finer thinner gauge metals when producing a piece. Hand forming against this linear pattern produces a very strong piece. While corrugation is very strong along the linear dimension of the corrugated pattern, it is fragile along the opposing dimension. When compressed in the opposing frail direction, the troughs and ridges can be made to collapse upon themselves. The creative designer can achieve many exciting forms by taking advantage of these basic factors.
Metal Corrugation Tools
There are a variety of corrugation tools currently available on the market that are most useful for some of the basic metal corrugation techniques and more complicated patterning that I have developed. Some of the tools were originally manufactured for an application OTHER THAN metalsmithing. Care must be taken when using ANY tool as a breaking point can always be reached. One can typically feel when it is time to back off application of pressure so as to not damage the tool. One or multiple tools can be utilized on the same piece of metal to further add surface texture.
Metal Corrugation Observations
Observation 1:
Metal will reduce and distort by approximately 25 to 30% depending upon the tool used, heaviness of your hand, gauge, and size of metal used. To determine the percentage of reduction: Finish size divided by original size equals percentage of original size. Work in millimeters to make this task easier.
Example: 150mm / 200mm = .75
Finished corrugated size desired: 200mm divided by % reduced 75% = starting stock needed 267mm
Distortion and reduction occurs at the angle of insertion and in the direction of travel as the metal is contracted. To best illustrate the distortion observation, cut two 2″ x 2″ Squares of 34 gauge copper. Use the corner as the leading edge of one square, corrugate then compare with the remaining untouched sheet.
Observation 2:
As the gauge and width of the metal to be corrugated increases, the ability to easily corrugate decreases. Added passes of annealing and corrugation will be required to achieve the desired effect. Using the tools currently available on the market, metal up to 24 gauge can be corrugated to the full depth of corrugation available with the tool recommended for metal. Up to three passes may be required (annealing between each) to achieve full depth of corrugation when using 24 gauge material.
Observation 3:
Metal thickness is doubled (or tripled) if you decide to process folded metal. It is easy to see in the calculation below how the thickness increases as folds are added
Observation 4:
Depending upon the corrugation tool selected: metal corrugated then each crest completely crimped flat along all rows will reduce approximately 64% of its original size. To determine the percentage of reduction: Finished size divided by original size equals percentage of original size. Note: working in millimeters actually makes the calculation process easier.
Observation 5:
After corrugation and "crimping" a crest, the next crest to be crimped may expand toward the previously crimped row. Remedy: from the reverse side, the trough can be re-established by using the edge of a ruler or template form that fits the corrugation pattern.
Observation 6:
After crimping a row, the previously crimped row may expand and need to be constricted due to "pull-apart factor".
Observation 7:
After pickling finely corrugated and crimped forms, soak in hot baking soda bath to completely neutralize acid caught in crimps. Place in hot water to soak away baking soda solution. Moisture will be trapped in the crevices. Make certain the element is completely dry before processing through the rolling mill or forming using steel tools.
Observation 8:
When corrugating to create texture for die forming using thin gauge material, texture may be lost unless cross corrugation, folds and/or crimps are added prior to die forming. Corrugation will not be effected nearly as much with thicker gauges of material.
Observation 9:
The point of contact during corrugation of round wire is limited. The limitations of corrugating round, square, and thin wire strips are based upon the heaviness of your hand, tool used, and gauge of material.
Observation 10:
Metal or debris trapped in the troughs of the corrugation rollers will create an imperfection in subsequent material processed through the tool.
Observation 11:
Damage to a tool with aluminum rollers can occur due to aluminum being pushed and crushed from the crest down into the trough. This may result from trying to process too large a gauge of wire stock through the corrugator, far beyond its capacity. Such damage to the roller will create an imperfection in subsequent material processed through the tool.
Observation 12:
Elements folded, in a fashion where metal overlaps onto itself unequally, then corrugated, will have evidence of a shadow pattern running the entire surface of the overlapped area. This is due to double thickness of metal corrugated in some areas versus one thickness in others. Shadow effects may not be as evident on thicker gauges of metal such as 26-gauge and may merely create an imprint along the edge of the overlapped area.
Observation 13:
To more easily open a folded and corrugated form, insert a paper wedge in the fold prior to corrugating. Use a slim or regular burnisher to open the element enough to remove the paper. Anneal the element prior to opening it completely.
Observation 14:
Uneven placement of paper used as a wedge to subsequently open a folded and corrugated element may create a shadow effect during corrugation.
Observation 15:
Elements folded in a uniform fashion and completely in half, will not experience the shadow effect due to equal depth of the material corrugated.
Observation 16:
Folds or metal thickness that is equal will be corrugated with equal intensity, while unequal folds will be corrugated with lesser intensity or not at all.
Observation 17:
Depending upon the tool selected, surface printing can be achieved by inserting paper with cutouts or inserting patterned paper wedges similar to the results accomplished using a rolling mill and roller imprinting.
Observation 18:
Folded and corrugated thin gauge metal can be opened, crimped, twisted, pulled and moved to create three dimensional, sculptural objects. As selected areas of metal are crimped together, the corrugated element has a natural tendency to close the form, draw up and create a pouch without the necessity of special tools to achieve this effect.
Observation 19:
It is a challenge to assess where a hole is to be drilled for construction of a piece prior to corrugating. A corrugated surface crushes if clamped to a drill press surface. If metal is drilled before corrugating, the opening will become misshapen by the process and will require alteration. Use a round hand file, needle file, or bur to correct the opening to round.
Observation 20:
A diamond bur set is wonderful for drilling into corrugated material if you are unable to determine where you want to place a hole prior to corrugation. With a small bur, an indentation can be created in a corrugated surface to accommodate the use of a cone shaped diamond bur. The cone shaped bur is especially useful if you wish to insert a tube into the corrugated element. Using the diamond cone bur, drill into one side then the other, as a bur will form if only one side is drilled. Continue to check the diameter of tubing against the progress made with the bur and stop when the tube will fit. Clean away any residual metal surrounding the opening prior to inserting the tubing for soldering.
Observation 21:
Soldering corrugated elements together is tricky business. When soldering corrugated elements together, the solder will inevitably want to flow down into the trough, following gravity, not the heat of your torch! Maintain a tight solder joint by whatever means works for you and what the project demands. Some suggestions to assist you are:
- A third hand to hold elements tightly together.
- Silicon carbide soldering grain to prop and position elements
together (this can also be used wet as a heat sink). - Yellow ochre or other anti-flux agent painted around the area
surrounding the solder joint but not on the area to be soldered. - Soldering block and T-pins to hold and prop the elements in position.
- Small wedges of fire brick cut to prop and hold elements in place.
- Small squares of copper used as props to lift elements up and into position. Note that this will also act as a heat sink and you must take precautions to keep from soldering these props onto your work!
- Use medium or easy solder.
- Use paste solder.
Observation 22:
When soldering crimped elements, solder will wick up into adjoining crimped crests as soon as the solder begins to flow. In joining segments of crimped elements, flux and solder each of the crimped crests closest to your solder joint. Yellow ochre applied to the crimped region surrounding the joint may be an alternative.
Observation 23:
To strengthen a crimped strip, it may be advisable and/or desirable to solder each crimp together before final assembly. When an unsoldered crimped section catches on something, it will pull apart.
Observation 24:
With a few corrugation tools, thinner widths or strips of metal may have a tendency to wander slightly on an angle while processing. Using annealed or soft metal, align the metal as desired and hold the metal in alignment while processing using a slight amount of pressure. Align the metal with the corrugation rollers and process again to intensify the pressure a little more. With a little practice, you will be able to determine what it takes to hold the metal in place and process it to your liking.
Observation 25:
When incorporating two different corrugated metals into a design, creating a second metal layer, it is better to use metal of the same gauge. The depth of corrugation will be the same on each piece resulting in perfect alignment of the crests and troughs to accommodate a tight fit for soldering or crimping the items together.
Observation 26:
Strength of corrugation runs along the liner pattern of the corrugated element. Fragility of corrugation is in the opposing direction.
Observation 27:
Any tool can be taken to the point of destruction. One can usually always tell when it is time to BACK OFF prior to the breaking point.
You assume all responsibility and risk for the use of the safety resources available on or through this web page. The International Gem Society LLC does not assume any liability for the materials, information and opinions provided on, or available through, this web page. No advice or information provided by this website shall create any warranty. Reliance on such advice, information or the content of this web page is solely at your own risk, including without limitation any safety guidelines, resources or precautions, or any other information related to safety that may be available on or through this web page. The International Gem Society LLC disclaims any liability for injury, death or damages resulting from the use thereof.
Related Articles
Steps on Making a Basic Wedge T-fold
Steps on Making a T-Fold Boat Fold
Fold Forming Tool List
Steps on Making a Chased Wedge T-fold
The All-In-One Jewelry Making Solution At Your Fingertips
When you join the Ganoksin community, you get the tools you need to take your work to the next level.
Trusted Jewelry Making Information & Techniques
Sign up to receive the latest articles, techniques, and inspirations with our free newsletter.