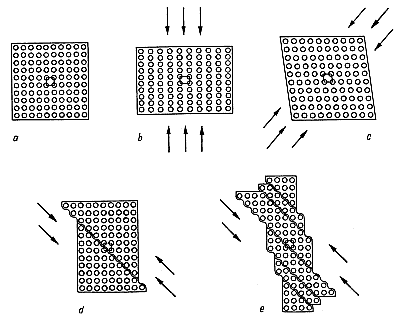
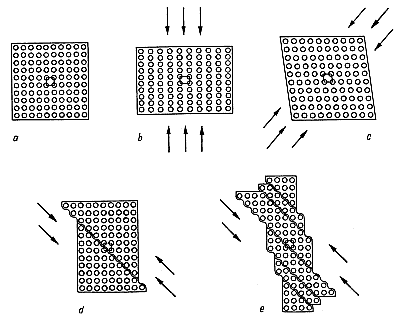
Metal Rolling and Drawing
Rolling can be thought of as a local, or isolated, deformation process during which thickness is decreased, length increased, and width remains unchanged. Drawing is different from rolling in that the pressure of drawing it not transmitted through the turning action of the mill, but instead depends on force directed locally at the area of compression. This means the amount of possible drawing force is limited by the tensile strength of the material, a fact that is particularly evident when drawing thin wires..
23 Minute Read
The phenomenon of deformation of a metallic material is a complex collection of many processes happening simultaneously. In order to describe it, we will consider these as discreet actions, but keep in mind that in fact they are all happening at the same time and influencing each other.
Our study here must be continued to relatively basic information:
- What occurs inside a single crystal?
- How is the crystal structure altered?
- In which ways is the entire piece of metal deformed?
Fundamentally what occurs in individual crystals and in the lattice structure is the same for all stresses. The changes on a larger scale, in the whole sample, for example, are dependent on the method of deformation being used. Forging is different from drawing, and bending is not the same as riveting. Because the effects of stress at the crystal and grain level are the same, one example will sufice for all forms of deformation. We'll use rolling to illustrate the process.
Elastic Deformation
Elastic deformation was already described in the discussion of the stress-ductility diagram. Any plastic deformation causes an elastic deformation in the whole block of metal as well as in each individual grain. Elastic deformation, you will recall, describes the effect of a metal returning to it's original shape when a load (or force) is removed. Even in this case, however, close examination will reveal that a few of the grains have begun to deform mechanically, meaning the stress has altered them to the point where they don't "snap back." The reverse situation is also true: even when a sample has been stressed to the point it has mechanically deformed, a few crystals can be found that have only been stressed elastically.
Figure 4.41 shows a simpli?ed view of the changes within a grain during elastic stress. Imagine the atoms as spheres joined by elastic bands. As illustrated in 4.41b, the space between atoms is reduced in the direction of pressure while the lattice structure is widened at right angles to it. If the pressure strikes the lattice structure from an oblique angle, as in 4.41c, the rectangle becomes a rhombus, where again the spaces between atoms decrease in the direction of the stress and increase at a right angle to it. In other words, the metal is squeezed downward and outward.
If in fact each atom was linked to its neighbor by a rubber band, if the stress were removed, the lattice would return to its original symmetrical structure. This is the definition of elastic deformation.
Plastic Deformation
Plastic deformation results when stress is so great the form is permanently altered. Plastic deformation is always preceded by elastic deformation. That is, metals will first move elastically, retaining the ability to spring back. If the load exceeds the elastic limit, the distances between the atoms do not grow any further, but the entire atomic lattice shifts along preferential slip planes These planes are especially dense with atoms. In cubic metals these planes are diagonal.
To describe the phenomenon using the rubber band model, we could say that when the bands can stretch no further, they are torn off from all atoms of the slip plane, the atomic "spheres" jolt along by one slip stage. Here the rubber bands are re-attached, re-forming the mutual bonds of the atoms (Figure 4.41d). This establishes the structure as it existed before, but with the crystals now in new locations. The outward shape of the grain has been changed, but the atoms within the crystal lattice are again ordered according their crystal system.
A gold grain, for example, is still organized according to the cubic face-centered lattice structure, even after rolling. The more slip planes available in a grain and the greater degree that the atoms shift on these planes, the more the grain changes from its original shape. If it is drawn out in one direction, as for instance when wire is pulled through a drawplate, it becomes narrower in the dimension at right angles to it as the result of numerous slip planes, as illustrated in Figure 4.41e. Such a shift of the lattice structure is only possible if the load is oriented in the direction of the preferred slip planes. A stress in a different direction is resisted by the grain because only a small portion of the force can be used for deformation. It is possible that the force available is only enough for an elastic displacement of the lattice structure (4.41b).
The lattice structure's resistance to deformation increases with the degree of deformation: the more the structure is changed and the stronger the force being applied, the greater the amount of force required to continue the deformation.
Effects in the Grain Structure
In the description of the solidi?cation process it was noted that a piece of metal is not an orderly crystal but instead consists of a multitude of small crystals (grains) which are randomly oriented. Because of this it makes no difference which direction the load is applied. Only those grains that are by chance oriented in the optimal deformation direction will give way and be plastically deformed. It's true that a single grain has an ideal orientation for deformation, but because grains are randomly oriented in a sample a multi-crystal piece of metal is equally plastic in all directions.
When a grain lying in the direction of deformation stretches, it immediately affects neighboring crystals because it is bonded to them. They are first elastically stressed, then they shift their positions through plastic deformation: the structure "?ows." If the deformation continues along a single direction, grains become increasingly elongated, eventually creating a structure made up entirely of long thread-like grains running in the same direction. This is a typical structure for metals that have been drawn or rolled. In plastic deformation, then, the originally randomly oriented sample develops a ordered grain structure according to the direction of working.
Figure 4.42 Alloy of Au 585. Large-grained sruture, seen cracking during early forming. V=125 |
As the process continues, increased force is necessary not only to push the grains along their slip planes, but to push other grains out of their way (Figure 4.42). Additional brittle grain boundary material is precipitated between the grains, stiffening the structure. This can inhibit deformation or even make it completely impossible. The grains are eventually stretched to the limits of their formability. If the stress continues, the forces of cohesion holding the sample together are exceeded, and the structure begins to tear.
For most metals, increased deformation increases hardness, tensile strength and maximum elongation and decreases ductility. That is, as you work harden metal, it gets tougher, longer, less malleable, and more brittle. Figure 4.43 charts these mechanical characteristics for copper. While actual values will vary for other metals and alloys, the tendencies and graphed curves are similar.
Figure 4.43 Changes in the properties of metal during transformation (example: copper). |
Rolling
Rolling can be thought of as a local (or isolated) deformation process during which thickness is decreased, length increased, and width remains unchanged. The sample is pressed and advanced through the rollers because friction pulls it into place as the rollers are turned. In order to understand the microscopic effects of metal passing between moving surfaces, we should first describe what happens when metal is squeezed between two unmoving surfaces.
Figure 4.44 Conic flow. |
Figure 4.45 The rolling process with the zone of flow. |
Forging Between Xed Surfaces
Stress is delivered, in these cases, at a right angle to the surface of a sample. This would be the case, for instance during forging, forming, chasing, and stamping. As shown in Figure 4.44, the metal does not distribute the stress uniformly, but reacts differently throughout different zones, some of which are affected much more than others.
- Contact between the tool and the surface of the sample produces such a great deal of friction that the metal cannot spread sideways from there. The lack of movement here extends inward to grains in close contact, limiting deformation in Zone I. This is equally true of the hammer (on top) and the anvil (on the bottom).
- The block of metal at right angles to the direction of load is bulged out by the external pressure and therefore the perpendicular force cannot affect the structure in Zone III.
- The structural changes are concentrated in Zone II which lies between the other zones, areas that are not affected by the deformation.
Forging Between Moving Surfaces
This information can now be carried over to the rolling process. As in forging, the rollers create friction at the point of contact with the sample, minimizing the ability of the metal to move at that point. The tendency for greatest deformation to take place in the interior sections can be seen in the ?ow illustrated in Figure 4.45.
Because the metal is constantly being brought into increased stress as it passes through the rollers, the situation differs from the impact of an unmoving force as described above. The area of greatest deformation lies on line FF, just behind the location of the smallest gap between the rollers. This results in the metal at the surface being pushed backwards forming a back ?ow. The metal in the area of the back ?ow moves slower and in the forward slip area faster than the peripheral rotation speed of the rolls; only the metal of the ?ow divide moves for the most part at the same speed as the rolls.
Figure 4.46 The rolling process with a thick block of metal. The core zone is not affected by the pressure of rolling. |
In addition, the pressure of the rolls is not as equally distributed over the entire cross section of metal as might be assumed from the simpli?ed diagram. Instead, the outer areas of the metal are more strongly deformed than the center of the piece of metal. It can even happen that the area in the center is almost entirely unaffected, as illustrated in Figure 4.46.
It is sometimes possible to observe this phenomenon with the naked eye by observing a leading edge of metal sheet that has been rolled. It becomes clear from these explanations that the structure of the metal is subjected to high stress and deformation during rolling, and must therefore be of faultless quality if it is to withstand the process. Or to say it another way, if you have an ingot that suffers from de?ciencies like pits and cracks, putting it through the rollers with the intention of correcting these ?aws is ill advised. The stress of rolling will only make them worse.
Equipment
The rolling mill shown in Figure 4.47 is especially designed for the small workshop. The rolling mill frame consists of four round pillars which connect the upper and lower end plates together. The bearings in which the roller's arbors rotate can travel vertically on the polished guide columns. The rolls are 45 mm in diameter and 90 mm wide. The upper pair of rollers can handle sheet from 0.01 mm to 5 mm thick. The grooved lower rollers are used to roll out square wire from 1 mm to 5 mm. The rolling mill is operated with a hand crank, a reduction gear making the work as easy as possible. The gap between the sheet rolls is adjusted with the large wheel mounted on the top of the machine; the wire rolls are regulated with two knurled knobs out of sight beneath.
Figure 4.47 A combination sheet wire roll. (Firma Eugen Dinkel, Hockdorf) Left) driven by a hand crank Right) driven by an electric motor |
The material being worked should emerge with a smooth, almost polished surface from a good rolling mill. This requires rolls of high quality steel that even after long use retain an undamaged polish. All the other parts of a rolling mill have to withstand great stresses and should therefore be made of first class materials too.
Whether a hand-operated rolling mill is suf?cient for regular use or whether it pays to have an electric rolling mill depends on the size of the business and its production program. Large production companies would not be able to manage without them. The rolling mill shown can be converted to a powered machine by mounting an electric motor into the base and constructing an appropriate power train for it.
A variation on a rolling mill called a beading machine is used by sheet metal workers to form sheet stock. With the proper attachments, this machine can be used by goldsmiths to bend up hollow bracelet forms and similar shapes. In this case, a strip of the appropriate width is fed between rollers that curve the metal into a loop as they alter its cross section, creating a compound curve. All that remains is to solder on an inside piece, or deck, to create a bracelet.
Care of the rolling mill
- Do not roll any hard and brittle materials like steel or oxidized metal.
- Remove borax residues before rolling stock through the mill.
- Dry material well before rolling it.
- Use all parts of the rolls evenly so they do not wear down in the middle.
If minor repolishing is needed, cut a piece of ?ne abrasive paper the same width as the rollers and fold it, abrasive out, over a wooden dowel that is also cut to the same width as the rollers. Tighten the rollers until they make contact with the rolls and turn the crank, holding onto the paper. Avoid using a coarse abrasive, which risks making the problem worse rather than better.
Preparing an ingot
Before being rolled into sheet, a cast ingot must be prepared by systematic, heavy forging. This will break up the crystals, which, after annealing, will be in the best condition for rolling. Only after the metal has been thoroughly compressed and prepared with annealings should it be rolled to its intended thickness. Though this appears to be an additional step, don't shy away from preliminary forging. It will signi?cantly improve the quality of the sheet and wire being made.
Rolling a Sheet
Before rolling, check to insure that both the ingot and the rollers are free of debris. Even a small piece of grit on either surface will create ?aws that can be time consuming to remove. Start by opening the gap between the rollers so the ingot passes easily between them, then narrow the gap until the rollers make light contact with the ingot. Pass the metal through the mill once without any pressure to be certain the surface is uniformly ?at. Remove the ingot from the mill and bring the rollers a little closer together. Compress the metal only a little with each pass, rather than attempt a dramatic reduction all at once. Use both hands and when necessary the entire force of the body to turn the handle.
It doesn't matter whether the piece is ?ipped upside down for the next pass. It can also be rolled back and forth without harm, but it should not change its direction of rolling without being annealed first. That is, do not rotate the work 90° unless you anneal it first. If a square sheet has to be rolled it must first be stretched long in one direction, annealed and then lengthened at right angles to the previously worked direction.
Once you begin a rolling action, continue with a smooth even stroke until the piece has passed through the mill. Stopping in the middle or cranking with a jerky motion will result in horizontal marks, or steps, on the sheet. Attempts to speed up the process by making large thickness changes between passes will result in hard work, stress on the mill, and lines that are the result of strained, irregular rolling speed. It's faster in the long run to progress ef?ciently in small increments.
Many mills allow the two sides of the rollers to be adjusted separately, which allows the rollers to be taken out of parallel if desired. In this way it is possible to roll a strip so it takes on a curve. Remember to set the mill back to parallel when you are done!
It goes without saying that metal must be annealed periodically as it is reduced in the rolling mill. Annealing too soon is a waste of time, while annealing too late risks damaging the metal through stress cracks. Though tempting, it is not recommended to judge the proper annealing sequence by feel; thick ingots are tough to roll even when annealed, and thin sheet might not feel work hardened even when it is due for annealing. Instead, use a micrometer to test the reduction, and anneal as needed. In the case of sterling, sheets should be annealed when they have been reduced by half. A 5 mm sample, for instance, should be annealed when it measures 2.5 mm, and again when it is half of that, 1.25 (Figure 4.48).
Figure 4.48 The allowable elongation when rolling and the necessary recrystalization temperatures for the important precious metal alloys. |
Rolling Wire
The process of reducing rod-shaped ingots to wire is similar to the sheet process just described, because the forces of rolling are almost identical. As before, the rod should be forged with a hammer and annealed to prepare the crystal structure for rolling. When this is done, the rod is inserted into a large groove in the wire rolling mill and given a light pass to insure a ?at surface. The rolls are then brought closer together (or the rod is moved to the next smaller groove) and it is rolled through. The piece is then rotated 90° and passed through the same hole. In the case of wire, the mill exerts stress not from just two directions, but from six because of the shape of the grooves. Annealing is required as above. The rod is passed through the mill until it approaches the desired size. For certain cross sections, the piece is then further reduced in a drawplate.
Table 4.15 Troubleshooting problems in rolling | ||
Symptom | Cause | Remedy |
The sheet is warped. | Irregular roller prressure; Center is worn. | Anneal and planish the part of the metal that has no9t been stretched enough. The roolers should be turned down to dress them. |
The sheet is warped. | The direction of rolling was changed without annealing. | Anneal and planish the part of the metal that has not been stretched enough. |
The sheet curves to one side. | The rolls have more pressure on one side: The rolls are worn on one side or the regulating screws are rightened unequally. | Equalize the screw positions. Have the rolls rurned down to dress them. |
The metal cracks on the edges. | An unsuitable ingot mold. The material has been stressed beyond it's breaking point. The material has impurities in it. There has been large grain formation caused by too-frequent annealing. | Open the cracks out broadly with a saw and anneal. Re-finish the ingot mold. Re-melt and purify the metal. |
The sheet is heavily cracked, brittle, or has mosaic-like crack formation. | Either the metal has impurities or has exceeded the breaking strength, or has cevelopedlarge grain formation. | Re-melt and purify the metal or send it to a refiner. |
Drawing
The principle of this procedure consists of reducing the thickness of a pointed, tapered wire by drawing it through a conical opening in a tool made of a hard material. The wire will simultaneously take the shape of the hole. Drawing is different from rolling in that the pressure of drawing it not transmitted through the turning action of the mill, but instead depends on force directed locally at the area of compression. This means the amount of possible drawing force is limited by the tensile strength of the material, a fact that is particularly evident when drawing thin wires.
Metal thickness is reduced by its passage through the draw cone. The steeper the cone, the greater the reduction; which of course means increased resistance and stress. The ideal shape of the cone and percentage of reduction are engineered into the design of a proper drawplate. By moving systematically through adjacent holes, the stress is minimized. Because of friction on its outer surface, metal on the outside of a rod is most affected by the drawplate, with the inner core remaining almost unchanged.
Tools
The most important tool in the drawing process is without doubt the drawplate. This consists of a plate of high grade steel into which similar shaped holes have been placed whose size is evenly reduced from one hole to another. Figure 4.49 shows how such a drawplate hole is made. The change in thickness occurs in the drawing cone while the cross section is shaped near the front, or smaller end, of the hole. The most common drawplates have round holes, and are used to reduce the size of round wire. Specialty shapes include rectangular, square, triangular, and knife-shaped drawplates. It is also possible to have unique shapes made up by an industrial die-maker.
Figure 4.49 The drawing process. |
The quality of the wire produced depends upon the condition of the drawplate. Only when the holes are absolutely smooth can a perfect wire be produced. The treatment and handling of drawplates begins with their storage. A quick way to damage a drawplate is to toss it casually into a drawer. A container in which the drawplates can be placed always pays for itself. Don't use a drawplate for any purpose other than drawing wire and making tubing. Despite their simple appearance, drawplates are sophisticated precision instruments and require at least nominal care.
To use a drawplate, place it between two protective plates of copper or another soft metal in a vise, positioning it so the holes to be used are reasonably close to the jaws. File a taper on the wire, feed it into the first hole where it is restricted, and grasp it ?rmly in drawtongs. These are sturdy pliers with handles long enough to allow them to be held with both hands. The ?at jaws are sharply textured so that the wire does not slip out even with a strong pull (Figure 4.50).
Figure 4.50 Drawing wire with the draw tongs. |
Wires over 2 mm thick will require the use of a drawbench, a device that connects the tongs by belt or chain to a large crank that signi?cantly increases leverage. For further ease a reduction gear train can be installed (Figure 4.51).
Automatic drawing machines are used in industrially settings to produce long ?ne wires, like the stock used in chain making. The wire to be drawn is wound onto a spool, and its pointed end fed through the appropriate hole in a drawplate. The leading end is attached it to a second spool that is electrically driven. In this way the thin wire is quickly, safely and uniformly drawn and wound onto the drum. Several drawplates can be arranged one after the other (often with a coolant bath between) to effect a large reduction with a single pull.
The last pull with thin wires uses a stone drawplate, in which drilled diamonds or corundum are set into a steel plate. These guarantee accuracy of dimension even during extended use. More recently, sintered hard metal materials set into steel plates provide similar durability at a lower cost.
Figure 4.51 Drawbench. |
Drawing Wire
Because rolling is easier than wire drawing, roll wire as far as possible before turning to the drawplate. The cross section after rolling is usually hexagonal or square, so suf?cient metal must be left to allow for the drawing process to create the desired section.
Be sure the wire is free from hard impurities such as iron particles, ?ux residues and so on. Anneal the piece thoroughly and ?le a taper about 20 mm long on one end. In thick wire the taper can be created by step rolling. Rub the wire with wax to reduce the friction at the draw cone. Locate the smallest hole the wire can be passed through then begin drawing through the next smallest hole. Grip the point with draw tongs and pull evenly, if possible without stopping. As a rule, no hole can be skipped because to do so risks over stressing the material being worked: the wire will snap or get stuck.
Just as in rolling, regular annealing is important in drawing. Thin wire is wound into a coil and bound with copper or steel wires. Heat the coil with a bushy ?ame, quench in water, remove the wrapping wire and pickle. Remember to dry the wire completely before continuing to draw it because moisture left on the drawplate will cause it to rust.
When drawing wires of unusual cross section, prepare the strip by making it resemble as closely as possible the ?nal shape. For rectangular or knife-edge wires, for instance, roll a wire through the sheet mill first to approximate the form. To make half round wire, solder two square or rectangular wires together for a short distance along their tips. File this section to a taper, and use it as the draw point to pull the double strand through a round drawplate. The result will be a pair of identical half round wires.
Making a Tube
Tubing is made by hammering and then drawing a parallel sided strip of sheet until its edges come together. During bending the outer area of the tube is stretched and the inner is compressed. This explains why the required starting width appears to be a size halfway between what would be calculated for the inside and outside diameter dimensions.
C = (D - s) · ?
C - the mean circumference in mm
D - the outer diameter
s - the metal thickness in mm
Prepare a strip of sheet that is a little wider than the measurement given by the formula. This will allow the ?nished tube to be drawn through several holes to make it smooth and round. File the edges of the strip at a slight angle so they will ?t well against each other when they are drawn into contact. Make a taper by cutting a point on one end of the strip. An alternate method, shown in Figure 4.52, is to solder a wire whose diameter matches the intended inside diameter to the end of the strip. This allows the tube to remain round and undamaged by the draw tongs.
Hammer the strip into a wooden V-block until its section is slightly more than half round. Direct the hammer blows along the edges rather than the middle of the strip to minimize the tendency to twist like a screw during drawing.
The strip of sheet is annealed and the edges are scraped clean, then the tube is drawn until the seam closes. Avoid the use of drawing wax because it prevents solder from ?owing. The drawn tube is closed by soldering with long thin pieces of solder. Pickle and remove excess solder by ?ling, then draw the tube through several sequential holes to make it completely round and of the desired diameter.
To make square, rectangular or triangular tubing, start with a round tube with a diameter larger than the intended result. To create a core, draw a copper wire to the intended inside diameter size and shape and coat it with oil. This wire should be at least 40 mm longer than the ?nished tube, projecting for at least 20 mm out one end. Clean this section of oil and spot solder it into the tube. After ?ling, this will be the draw point for the operation to follow.
Draw as for wire, starting with the first hole in which the tube makes contact, and proceeding sequentially without skipping any holes. Because there is more stress in this process than in normal drawing, be prepared for some hard pulling. Continue until the tube comes into contact with the core. To remove that wire, first saw off the tip where the two units were soldered together. Working from the back side of the drawplate, feed the core through the hole that formed it; this will not allow the tube to pass through. Grasp the copper wire and withdraw it. Be careful that you don't use the front of the drawplate for this because the cone shaped hole will effectively squeeze the tube onto the core and lock them together. If the tube is to be bent, leave the copper core in place until the bending is Finished, then remove the internal wire with acid.
You assume all responsibility and risk for the use of the safety resources available on or through this web page. The International Gem Society LLC does not assume any liability for the materials, information and opinions provided on, or available through, this web page. No advice or information provided by this website shall create any warranty. Reliance on such advice, information or the content of this web page is solely at your own risk, including without limitation any safety guidelines, resources or precautions, or any other information related to safety that may be available on or through this web page. The International Gem Society LLC disclaims any liability for injury, death or damages resulting from the use thereof.
Related Articles
Wire Wrapping Enamel Pieces
Cutting Jump Rings
Soumak on Metal
Using Coils To Bend Tubing
The All-In-One Jewelry Making Solution At Your Fingertips
When you join the Ganoksin community, you get the tools you need to take your work to the next level.
Trusted Jewelry Making Information & Techniques
Sign up to receive the latest articles, techniques, and inspirations with our free newsletter.