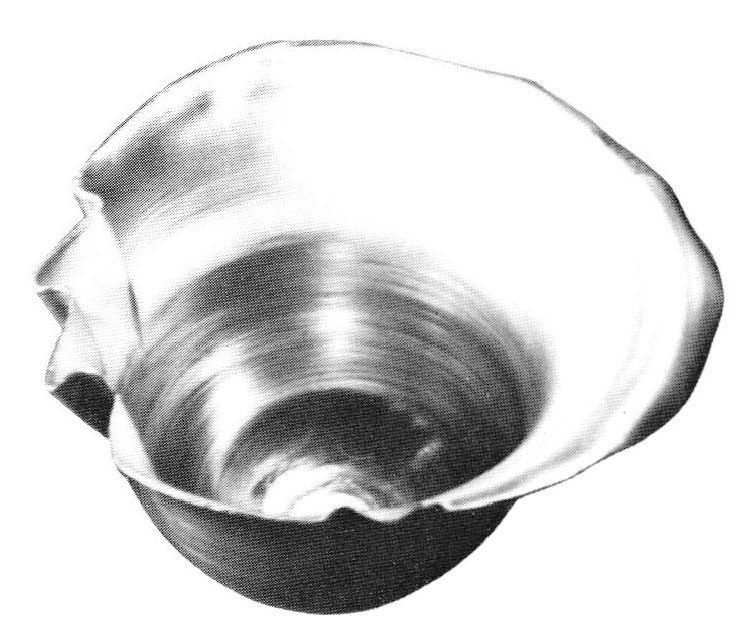
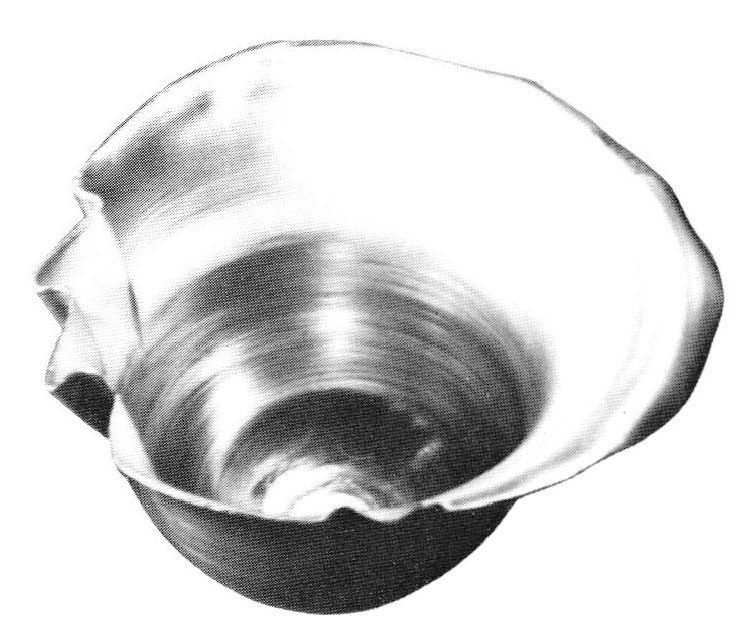
Metal Spinning Part 2: Techniques
18 Minute Read

This article is the second of a three-part series on Metal Spinning by James Seavey discussing the techniques in developing spinning skills.
The process of metal spinning involves the entire body. As with any hand-forming process, it is the skill (the accumulation of kinesthetic knowledge), not the strength, which determines results. What follows is a description of the techniques, noting variations and problem solving, which may serve as a practice guide to a metalsmith developing the skill of spinning. And once the skill has been mastered, one can begin to apply aesthetic judgement to master the art of spinning.
For the first attempt, it is best to use a flat-bottomed form about half again as high as the diameter at the bottom. The disc diameter for such a form is about two-and-a-half times the same diameter—thus for a vessel or "shell," 2″ in diameter and 3″ high, a 5″ diameter disc is about right. It would be advisable to use a form (known as a chuck) and disc size standard to an experienced spinner so that one can use tested equipment to judge whether the form comes short or requires excessive trimming back.
Forming a necked piece using tool on either side of the fulcrum pin. Photo: Jean Baer O'Gorman
After selecting a chuck (chucks will be covered more completely in Part Three), screw it into place over the threaded head-stock spindle, being careful that the chuck seats properly without dirt or metal trimmings interfering. Be sure that the chuck runs true by jogging the motor on. If the chuck seems off-center, hold a felt-tip marking pen to the end of the chuck lightly as it rotates so that when it stops, the high point has been marked. (This can also be done with a dial gauge.) Loosen the chuck and shim the high side with a sheet or two of paper, then check again. This running out of true can be attributed to any number of causes: a chuck has been used on a different lathe (with or without an adaptor); is slightly off the axis on a machine lathe; is warped or damaged by dropping; or requires reseating due to worn threads.
Placing the disc live
Select a follow block whose diameter matches the bottom of the chuck. Too large a diameter will not allow proper contact of the tool at the beginning of the first stroke; too small, and the bottom of the shell will tend to buckle back over the follow block. The block should center properly—that is, rotate on the same axis as the chuck when clamped into place by the action of the tail spindle of the lathe.
With lathes equipped with a cone-shaped live center, a small dimple centered on the tail side of the block keeps it running true. If the center has a cylindrical pin with a shoulder, a hole which fits snugly over the pin may be drilled in the follow block, which centers the block and keeps it in place when more than one of the same shell are being made. Blocks may be made by forming the center on a rough-cut, over-sized circle of plywood, nylon, Teflon, hard rubber or similar material. It is then clamped to the chuck for which it is intended on the lathe, and the edge turned to the proper diameter. Often for forms with a flat bottom, the chuck and follow block are relieved (cut back) on the central surfaces out to within about ¼" of the edge to center the disc and to prevent marring the metal.
Centering
Set the lathe drive for the proper speed. Once again, experienced help will be of great aid. As a general rule, spinning is done between 800 and 1800 rpm; the thicker the diameter and/or disc, the slower the lathe will spin. Very thin discs are spun commercially at speeds up to 5000 rpm, and very large discs may require speeds below 100 rpm. Too high a speed can cause wrinkling and chattering and burn out lubricant. It also can cause thicker, shorter forms. Too slow a speed may harden, tear and push the shell out of shape. Yet with skill, almost any improper speed can be compensated for—or used to its own advantage.
The disc is then clamped into place between the chuck and follow block, as closely centered as possible. Experienced spinners do this while the lathe is running to save time. On certain operations it may take longer to stop the lathe, remove and load the work pieces, and restart than to do the spinning. To place the disc live, lightly hold the disc between the left thumb and index finger, centering by eye while the disc is riding against the chuck with the hand directly over the axis of rotation. Then the right hand activates the closing mechanism of the tail spindle—usually a snap of the wrist to spin the spindle wheel. The spindle moves rapidly to the chuck, clamping the disc with the follow block. The disc begins to rotate and slips from the grasp of the spinner whose hand is then pulled away. The disc must be held lightly enough so that when the follow block engages the disc, the hand is not pulled downwards; it must be centered as closely as possible to keep the eccentrically moving disc from nipping the hand.
Beginning the stroke
Do not place the disc live until the chuck and follow block have been used together a few times after each setup to insure that proper clamping takes place. If the follow block has been damaged or altered, the chuck marred or running out slightly, or an incorrect distance between the center and the tail stock causes vibration, the disc may not stay centered. This may also result from over-tightening. The danger of the disc catching off center is increased with the diameter of the disc—the risk of injury is due not to the frequency of off-centered discs, but to the greater arch of a larger disc's swing. As with all matters of safety, caution and good judgement inform the decision to place the disc live.
Centering
Once the disc is clamped in place, it usually needs further centering. This is achieved by applying pressure to the edge of the disc while slightly loosening the follow block while the lathe is running. The centering tool, which may be a flat hardwood stick, a flat-faced spinning tool, or even the flattest part of a spoon or tongue spinning tool, is held in the left hand. The tool is on the tool rest against the fulcrum pin so that the disc's plane of rotation is at right angles to the face of the tool and the axis of the tool is in the same plane. The point of contact between the tool and the edge of the disc is underneath the disc, towards the front (in the 7 o'clock position).
Failure due to excessive pressure at the beginning of a stroke
The spinner stands to the right of the plane of rotation and controls the tail block pressure with the right hand. With the lathe running, the follow block is loosened slightly and the centering tool pushed up firmly against the disc until the tool ceases to vibrate, and the highlights on the edge of the disc appear stationary: The follow block is then tightened and the centering tool removed. In practice, it may be necessary to "play" (vary higher and lower) the follow pressure in order to center.
Should the disc fly out of control or start to drift off-center, pull the left hand out of the way and release the tail spindle pressure. This will cause the disc to jump from the lathe, which is dangerous, but less so than when it jumps without warning. Causing it to jump deliberately prevents damage caused when what may be a valuable disc hits the tool rest, lathe bed or safety shield. This quick release of the follow block pressure tends to decrease the velocity at which the disc jumps; in fact, it may often simply fall.
Failures due to excessive pressure in the mid-point of a stroke; this may occur at a point not backed by the chunk as well
Lubricating
Lubricant is applied to the centered disc at the follow block and swept outwards to the edge. The applicator may be a short bristled brush, a wadded cloth (sometimes held packed in a tubular handle), a tubular container (as with stick wax) or a handheld chunk of solid lubricant (such as soap or tallow). The container of lube is kept handy, often in a tub or tray bolted to the lathe. The choice of lubricant depends on many variables, including resistance to breakdown under pressure and/or heat, adhesion, cleanup ease, availability, effect on finish, visibility of the metal surface and even the weather. Generally, softer metals require softer lubricants; higher speeds require harder lubricants. As with running speed, each spinner develops preferences for each case. The accompanying chart is a rough guide.
Lubrication Table | |
Metals | Lubricants |
Titanium and hard tempers of many metals cannot be spun easily. Brass requires frequent annealing. Copper and aluminum are sticky, so a porous tool (wood) is recommended | Old books on spinning recommend tallow as a lube, although it is not readily available today. Sometimes lubricants can be mixed to achieve the desired properties. Wiping with a cloth or steel wool while the lathe is running can speed clean-up |
Platinum, niobium, gold, tantilum, stainless steel | Beeswax, parafin, naphtha soap (dry), stick wax |
Mild steel, brass, bronze, zinc, hard aluminum alloys | Hard spinning soap, stick wax, water pump grease |
Copper, aluminum, sterling silver | Spinning soap, stick wax, grease, synthetic grease |
Pewter, lead | Grease, petroleum jelly, shaving soap, soft spinning soap |
Suppliers |
Stroke Pressure Diagram | |
The thickness of the line represents the amount of pressure. The direction of the line represents the sweep, which may vary | |
Beginning to Spin
The first stroke with the spinning tool is the most critical. While one wants to push the metal as far as possible on each stroke, especially with metals like brass which harden quickly, the first stroke permanently centers the disc, establishes the working base for subsequent strokes, smooths out warped or uneven discs and gives the spinner the feel of that particular metal-something extremely important on one-of-a-kind spins or at the beginning of a run.
Failure due to excessive pressure near the end of the stroke. The disc was mounted eccentrically to show that the pressure near the edge will cause wrinkles (this can be used decoratively) and not disturb the midstroke area.
The sweep—the radial movement of the tool—is determined by the vertical movement of the tool handle. The tool rest is adjusted, so that with shoulder, rib cage and hip lowered, knees flexed and feet flat on the floor, the tip of the tool is positioned to the right of the disc against the follow block at seven o'clock. The tool rests against the fulcrum pin on the rest; often the left hand grasps this junction lightly as a way of steadying the work and providing kinesthetic feedback. As the body stretches upwards—shoulder, rib cage and hip raised, knees straightened and feet on toes—the tip of the tool drops in a shallow arc from the follow block to the edge of the disc, again at 7 o'clock. The force of the stroke is in the lateral movement, toward the headstock, controlled by the flexing of the spine that moves the ribs to the right, the movement of the hips and the unequal flexing of the knees and lifting of the feet. The combination of all these movements at different rates and amounts of force exerts the will of the spinner on the metal.
Spinning on air; only the bottom part with straight sides was done with the chunk. The edge was formed by cutting off random chords at the edge of the disc before spinning, and later hammering the edge
The first stroke begins at a point close to the follow block and continues towards the headstock and the axis of rotation simultaneously. The disc is thus forced against the chuck at the point closest to the follow block in a ring, in the same manner the first row of hammer blows commences hand raising. The stroke is then swept out to the edge (or a point short of the edge on pieces with a very small area clamped by the follow block), with diminishing pressure so that by the end of the stroke no pressure is exerted. This is called feathering.
If every stroke were a feathering stroke, the disc would form a cone whose sides would be increasingly concave to the point at which the metal would tear near the narrow end. To feather the beginning and end of the stroke would bring the tear point towards the middle. The first few strokes tend to be done with increasing even pressure. As the form becomes a more acute cone, the narrow end is pushed against the chuck at the beginning of the stroke in the same way that the first stroke creates a ridge or "bite" at the start. The properly controlled stroke pushes this ridge ahead of the tool; too little pressure or too fast a stroke in relation to the pressure and the bite will be lost, lessening the effectiveness of the stroke. Too much pressure, and the metal stretches excessively at the point of contact with the tool, and the edge folds backwards (towards the tail stock) or wrinkles severely. Short, corrective strokes, in a back-and-forth sweep feathered at both ends, can eliminate minor wrinkles, over stretching or fold-back. A long back stroke from edge to chuck will compress the metal so that a thicker section (gauge) may be maintained.
Another example of spinning on air, neck formed without backing. Photo: Jean Baer O'Gorman
In spinning cylindrical forms, once the cone has become quite acute, and 30 to 50 percent of the disc has been laid down (in contact with the chuck), a flatter tool can be used with firm, even strokes to lay down the remainder quickly while increasing the section. Sharper radius tools tend to stretch the metal and leave minor ridges called spin lines; blunter tools tend to thicken the section, cause wrinkles, but leave no spin lines. The final stroke is often done with as flat a tool as possible, without edges that would score the concave surfaces of the shell, and with firm pressure applied against the chuck: this is the planishing stroke. Once confidence and skill are developed, it is possible to spin "on air"; that is, with part of the final form made without contact with a chuck, thus allowing both the forming of necked vessels without special tooling and creative control of the form. It is with spinning on air that the greatest artistic freedom is achieved-similar to that of a potter or wood turner.
The back stick used to support on air spinning
On some occasions, with large discs or severe wrinkles, a backstick is used as a temporary chuck on the back side of the shell. This can be a hardwood stick or a flat spinning tool held in the left hand against a second fulcrum pin. It is pressed against the disc directly opposite the main spinning tool. This arrangement can be used to add more control to spinning on air.
Trimming
Trimming the edge may be required at any stage to even up a disc that has become distorted by uneven working or centering, by the grain of the metal—that is, the orientation of the metal crystals acquired during the rolling operations of manufacture of sheet metal. The final trim may be done just before the final flap is laid down; this is a useful technique when spinning a shell only partway on a chuck for a form shorter than one for which the chuck was designed.
The back stick used to aid in the removal of wrinkles
The trimming tool most often used is a diamond tool—a square shaft of tool steel cut diagonally at one end, held at the other in a tube or pipe handle or collar on a wooden handle. The trim is achieved by holding the tool against the fulcrum pin (cupped by the left hand) and slowly bringing the cutting edge into contact with the edge of the disc. There are two positions for this. One is with the tool handle parallel to the floor and the flat of the tool on top, the diamond forming the relief to the cutting edge which makes a contact at right angles to the disc edge. The other is to turn the tool over so that the diamond faces up and holds the tool at an upwards angle on the tool rest so that the point of contact comes at the tangent of the tool's flat side and the disc's edge.
The second method is trickier, but affords greater control and safety from chips that fly from the spinner or a slip which may catch the tool, driving it backwards and down rather than kicking it up. On larger pieces and the harder metals, the lathe should be slowed to the slowest speed or jogged (turning the motor on and off in short bursts) while trimming. Sometimes commercial spinners will switch to a machine lathe for trimming. With the tool held in the proper position and moved slowly and steadily, there is little danger in trimming. Nevertheless safety guards, especially a face shield, should be worn as protection against flying chips.
The planishing tool is applied in a smooth firm stroke. Photo: Jean Baer O'Gorman
Removing Finished Shell
Although some special procedures may be required, removal of the finished shell can be done live or still by loosening the tail spindle and grasping the piece. On deep cylindrical forms where the metal has stayed in close contact with the chuck (no springback), it is usually necessary to break the vacuum caused by the plunger action of the chuck within the shell by grasping the piece as it spins. An alternative to this procedure would be to drill a small hole in the center of the disc before starting. If a shell resists loosening when being grasped live, even with leather gloves, the piece can be loosened by a final planishing stroke with the follow block removed.
Trimming tool in use
When making the chuck, care must be taken not to allow a backward taper which will permanently lock the shell on the chuck. Sometimes with a wood chuck the shell has been worked on so tightly that even live removal or extra planishing does not remove it. The even heating of the shell with a torch should expand the metal enough to allow its removal: at worst, the chuck may be slightly charred. Sometimes a burr will prevent the removal of the shell. A small, hooked cutting tool can then be used to remove the burr with little or no damage to the chuck.
Fine Spinning
Tangental position for trimming
Several specialized tools are appropriate for "fine spinning"—the work on a small scale that can add design interest or strength to a finished piece. These are generally made of smaller diameter round or square steel rod and have smaller handles than the forming tools. Small tools with the same shape as the larger ones can bring up details such as ogees and grooves.
One variation is the "knife," a flat tool with one edge tapered to make a varying radius so that different radii grooves can be made depending on the point of contact, either in bands, or by moving the tool laterally, in spirals. Screw threads may be formed at low speed over a threaded chuck: The lathe must be stopped and the shell unscrewed for removal. A flat piece of bar stock with a slot cut in one end to accept the thickness of the disc to a certain depth is used to bend over flaps near the edge to form a pan shape on air or in preparation for forming a bead—a rolled edge. The edges of the slot must be rounded and the inside surfaces smooth. The shaft may be bent to allow the proper angle of attack. Tool steel serrated cutters are used to score parallel bands around the finished piece.
Parallel position for trimming
A miniature version of the large wheel tools used to reduce friction on heavy work is the knurling wheel. Much the same as a machinist's knurling tool but with a single wheel and long handle, the decorative design of the wheel is embossed into the rotating shell. A concave wheel tool with a smooth surface is sometimes used to form a bead.
The finest tools of all are the abrasives: sandpaper or cloth, steel wool or buffing compound applied with a cloth. Some spinners do their final finish on the lathe, using holding chucks to finish the inside surfaces. A scrubbing motion made while applying pressure will help to eliminate parallel bands left by the various abrasives.
Rolling back a bead. Photo: Jean Baer O'Gorman
By spinning on air or by using successive chucks, a spinner can expand the vocabulary of forms available from a given set of chucks. Often it is possible to make one chuck perform many functions by varying the follow blocks or adding rings or other elements. The variations of chucks and followers will be covered in the next section, with particular emphasis on getting the most out of limited tooling.
James Seavey is a graduate of Rhode Island School of Design where he studied Metalsmithing with John Prip. He has worked as a designer-craftsman for Gorham Silver Co. and Old Newbury Crafters and as plant manager for Faithcraft International. Currently he makes and markets pewter holloware under the name Halibut Point Pewter in Gloucester, MA
Related Articles:
You assume all responsibility and risk for the use of the safety resources available on or through this web page. The International Gem Society LLC does not assume any liability for the materials, information and opinions provided on, or available through, this web page. No advice or information provided by this website shall create any warranty. Reliance on such advice, information or the content of this web page is solely at your own risk, including without limitation any safety guidelines, resources or precautions, or any other information related to safety that may be available on or through this web page. The International Gem Society LLC disclaims any liability for injury, death or damages resulting from the use thereof.
Related Articles
Additive Manufacturing in the Jewelry Scene
Choosing the Right White Gold
Electric Kiln Fired Mokume Gane Part 3
Electric Kiln Fired Mokume Gane Part 2
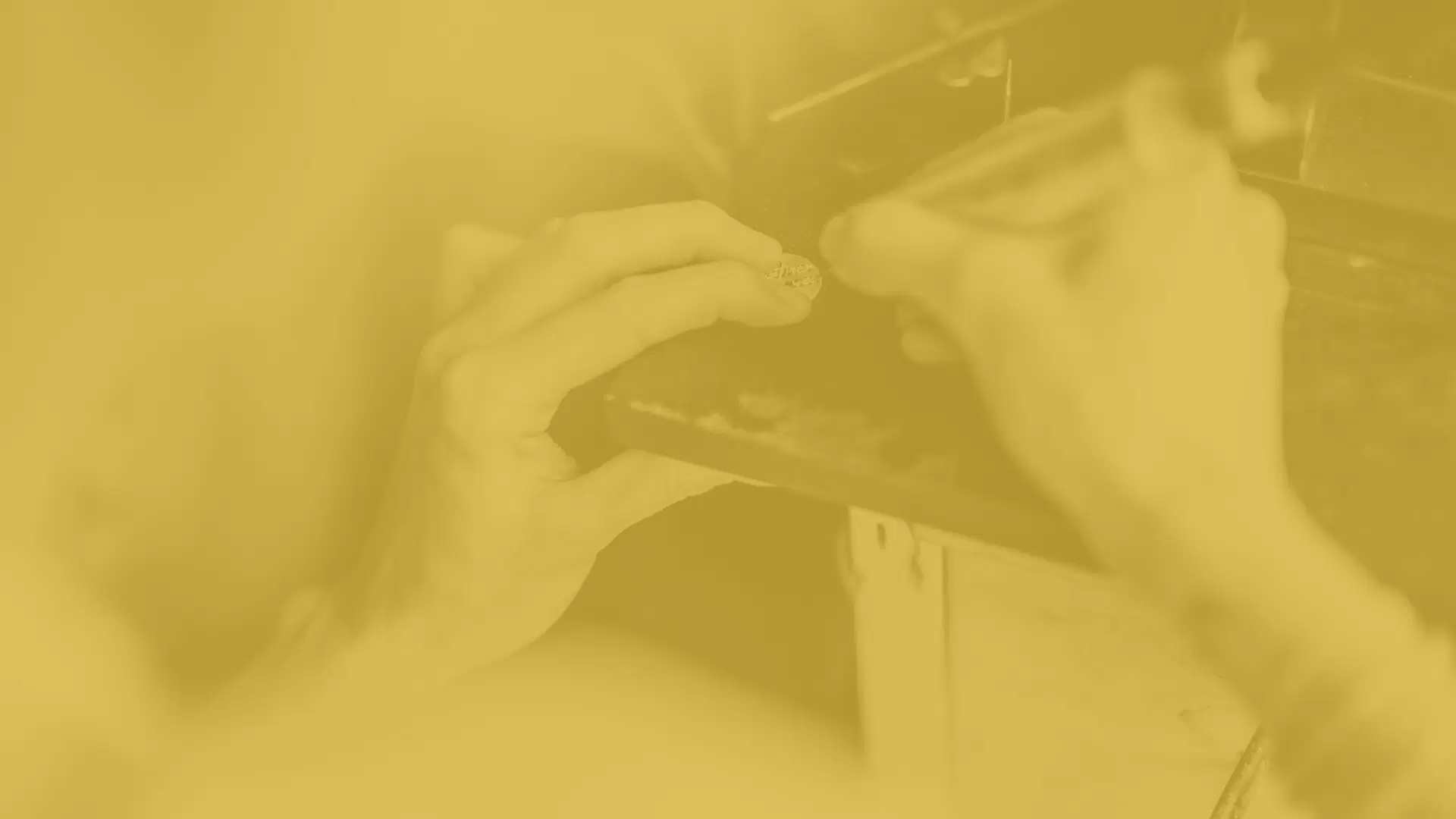
The All-In-One Jewelry Making Solution At Your Fingertips
When you join the Ganoksin community, you get the tools you need to take your work to the next level.
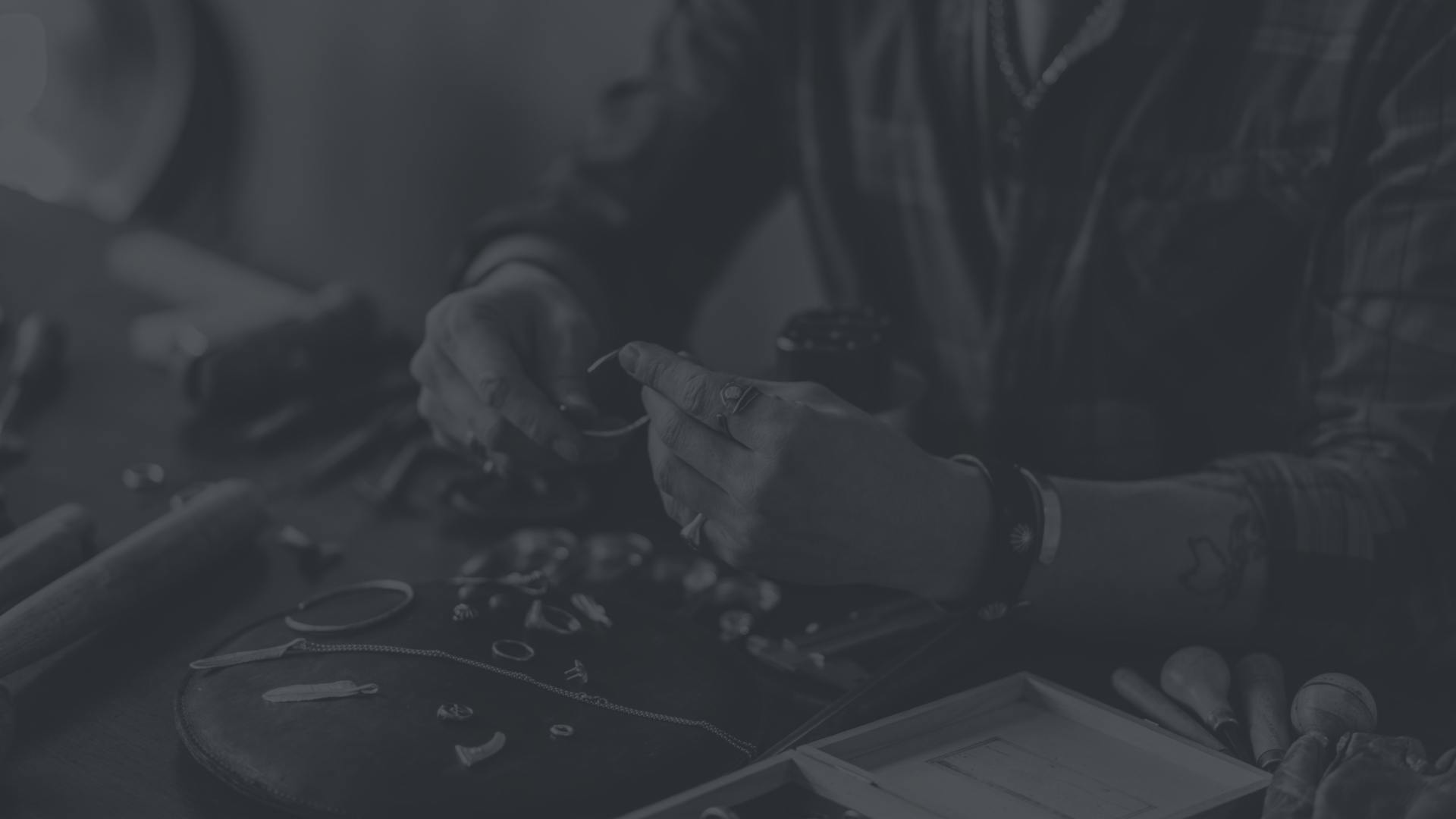
Trusted Jewelry Making Information & Techniques
Sign up to receive the latest articles, techniques, and inspirations with our free newsletter.