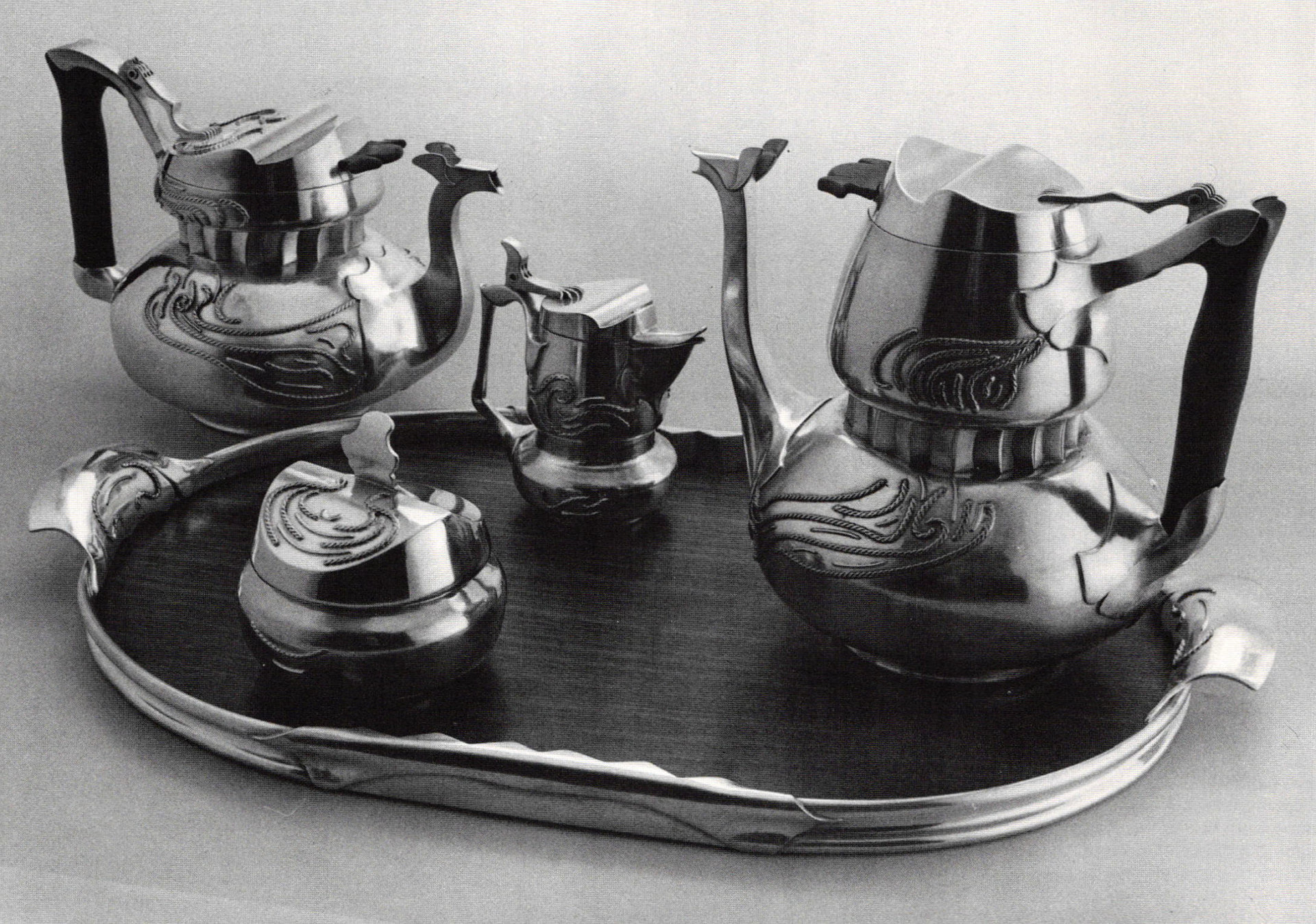
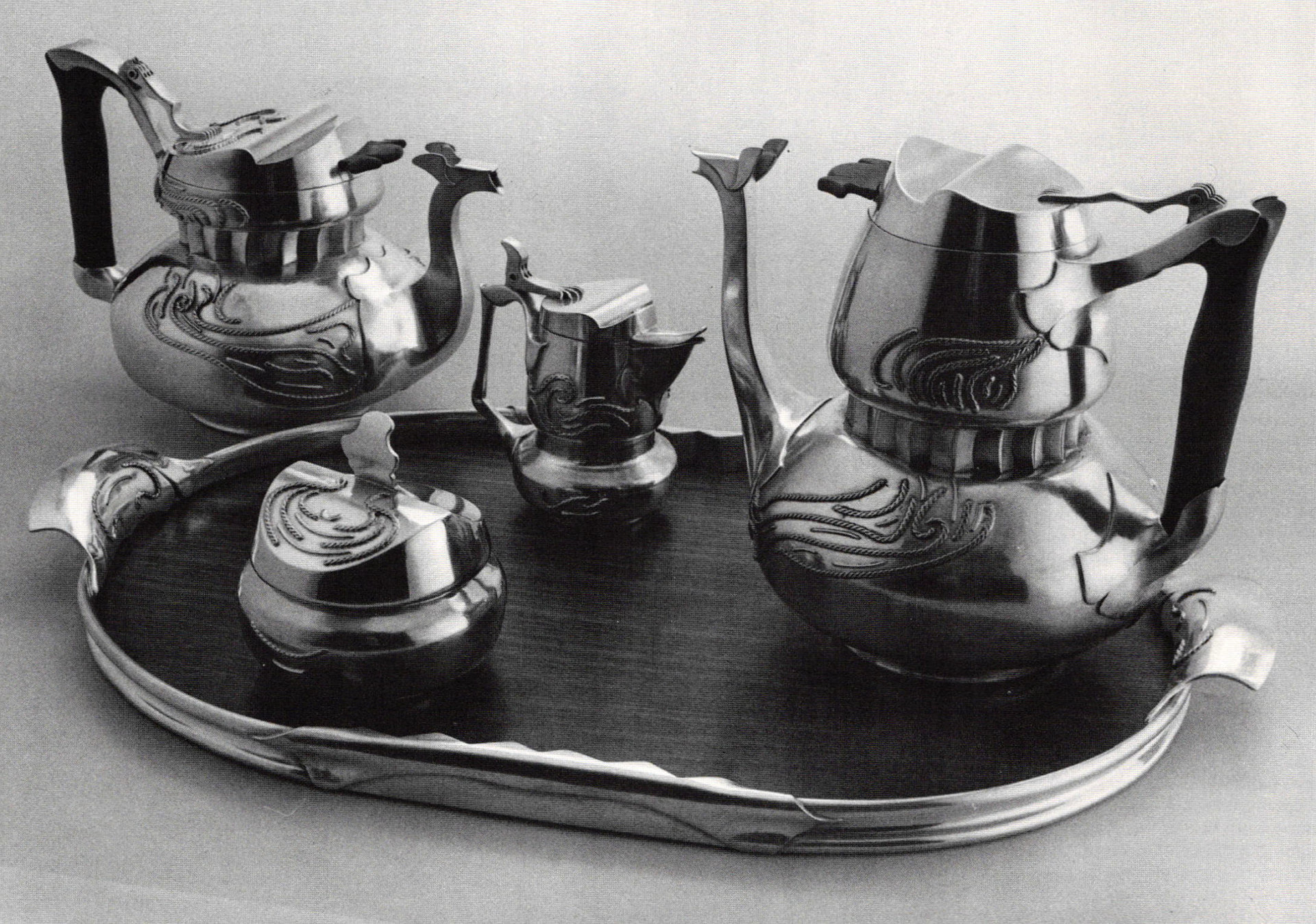
Metal Spinning Part 3: Tooling
11 Minute Read
As skill develops in spinning, it becomes more important to have a sense of what forms can be produced. To fully appreciate the range of shapes possible, a thorough knowledge of tooling is needed. "Tooling" denotes the specialized tools needed to perform a specific task, as opposed to "tools" which are the hand devices or machines capable of producing varied results in a variety of ways.
In spinning, the lathe and spinning tools are the tools and the chucks and follow blocks are the tooling. Because the process of spinning requires the skilled use of tools, the tooling can be used in a more varied way than can be expected from other processes. The chuck is actually a one-piece die, either male or female, whose counterpart is replaced partly by the follow block and partly by the movement of the spinning tool. By combining different chucks in sequence, varying the amount of metal "laid down" (in contact with the chuck), by adding or removing parts of the chuck, using a variety of follow (tail) blocks, and/or by spinning on air, it is possible to make a given chuck perform many functions.
The simplest form of chuck is a plain cylinder of any depth or diameter. Next in complexity is a truncated cone, then a cone with concave or convex sides and, finally, cones with combinations of curves and straights. As with any type of mold or die, undercuts must be handled in special ways which allow the removal of the shell without locking it onto the chuck.
Combination cylinder/plug chuck with sleeve and two plugs used to form shell shown |
The chuck can be made of any machinable or castable material with sufficient strength and resiliency to hold up to the job at hand—one-time use or up to hundreds of thousands of repeat operations. The most common chuck materials are hard maple, aluminum, steel or compressed fiber. Also used are nylon, epoxy, plywood, masonite, fiber-reinforced polyester resin, hard rubber and so on. Hybrid chucks of more than one material are also used, particularly wood covered with brass or steel; steel, aluminum or wood with nylon or other plastic; and steel or aluminum with epoxy, polyester, flexible rubber or wood.
Typical Chuck Cross Section |
Material choice depends on availability, ease in forming, type of chuck, forming resistance of the material to be spun, amount of use, weight and surface finish or tolerances required. Soft materials are usually readily available and easy to shape and may be clad by spinning brass or mild steel over the surface: they are not very durable and may leave distinctive textures on the inside of the shell. Harder materials tend to be more expensive, harder to form and heavier, but are very durable and precise.
Chucks may either be threaded to accept the head spindle of the lathe (or adaptor), mounted on a faceplate, fit into a hole or collet, or fit over a pin or shaft. Sharp corners on a chuck will tend to cut through the metal being formed (the blank), especially near the center. A sharp corner on the shell can be formed by the proper use of the backstroke over a shoulder on a chuck with a fairly large radius. The chuck may be notched in a ring, or relieved, at the desired end-point of the shell, to act both as a guide in trimming and to allow the proper placement of the trimming tool. If the shell is to have a hole or holes in the bottom, appropriate pin(s) can be placed in the chuck and holes punched or drilled in the blank to match, thus eliminating the need to center. The follow block should be relieved to accept the pins.
Breakover Chuck Applications | |
In preparing material to be fashioned into a chuck, the first step, once the proper size has been achieved, is to drill and tap or machine female threads to accept the head spindle. An alternative is to drill an oversized hole in the chuck material, apply release agent to the head spindle, spread a catalyzed, epoxy-metal powder mixture to the spindle and in the hole in the chuck blank, and clamp the blank in place in the lathe with the tail stock. When the epoxy has set, if the chuck is of a soft material (wood, aluminum, some plastics), the chuck can be turned right on the lathe and removed by unscrewing (overtight chucks are removed by tapping a center punch placed in a predetermined spot on an unused surface of the chuck: the tighter the chuck is wedged on, the bigger the hammer).
Care must be taken to temporarily fill any undercuts with clay or wax on the spindle threads. Otherwise, when filled with epoxy, the chuck would become locked onto the spindle. Be sure there is enough material beyond the threaded hole in the chuck to turn the desired shape without cutting through. The chuck can be formed on a machine lathe as well, provided the area gripped by the lathe chuck is concentric with the threads cut in the material, or an adaptor is used that allows the direct mounting of the chuck blank onto the machine lathe spindle.
Follow blocks can also be made from a wide variety of materials, preferably light, tough materials such as nylon, hard rubber, compressed fiber, aluminum, hardwood or plywood. With flat-bottomed chucks, the block should be the same diameter as the bottom, and often the interior portion of both the block and the chuck are made concave, that is relieved, to aid in centering and to reduce marring of the blank.
On convex chucks, it is necessary to have a concave follower; sometimes it is possible to start with a small follower, then switch to a larger one which covers most of the area already laid down. In either case, marks left on the bottom area of the shell can be removed by planishing after the rest of the shell is complete and the follow block removed. Round-bottomed forms may also be made by using a breakover chuck. Specially shaped follow blocks are used to form shells with reverse curves. The convex shape is first spun with a normal follower; then a follower which conforms to the laid-down portion of the shell and the desired reverse curve is exchanged with the first: the follow block then acts as chuck, the spinning being done towards the tail stock.
Holding Chucks | |
Chucks used for preliminary forming are called breakover chucks. They are usually made of wood. As the surface quality can either be improved on a metal final chuck or will be out of sight on the finished shell, accuracy is also often less critical. Breakover chucks are most often used in conjunction with plug chucks and section chucks, or where it is necessary to have a thicker section on the finished shell in places which would normally tend to be thinned.
Other uses of breakover chucks are to provide predetermined annealing points, to form parts to be completed by other methods and to allow spinning deep forms on a gap-bed lathe. Concave breakover chucks are used to form shallow bowls: The blank is first locked into place over the rim by spinning; then the follow block is removed and the disc pressed in from edge to center, much as with dapping (sinking).
Section Chuck | |
Plug chucks are two-part chucks held together by a central pin and tail spindle pressure; they are used to form necked tubular shells. The parts are made to separate at the narrowest part of the neck—the bottom of the shell is cut off to allow the plug to be removed from the shell. The pin is usually set in the plug to allow other uses for the body of the chuck.
Sleeve/Ring Chuck | |
Section chucks are used when large production runs of precision necked forms are needed. They are usually made of hard maple or maple sections on a steel mandrel. For high production they are occasionally made with nylon or steel sections. Considerable preliminary work is required to prefabricate the sections and temporarily join them in order to machine, shape and fit the mandrel. Unlike with the plug chuck, here the sections part from the mandrel (which also forms the upper part of the chuck) anywhere on or above the narrowest point of the neck. The sections have a tab which fits into a ring recessed into the face of the mandrel at the separation point. The mandrel may be cylindrical, but is most often slightly tapered.
In order to form the sections from maple, they are formed all at once to the proper shape and to fit on the mandrel. The entire piece of wood is removed from the mandrel and then split lengthwise to form the sections. The key section, removed first from the shell (after the shell and sections have been removed from the mandrel), is made with edges angled wider at the center and narrower at the outer diameter. The key section must be small enough to allow for removal from the shell with all the other sections in place, yet large enough to allow the removal of the second section (which is not usually next to the key section). This limits the relative diameters of neck and belly for shells formed, although necks can be further reduced on a holding chuck.
Usually the sections are held in place at the bottom by a previously formed shell which conforms to the sections up to the widest point and continues from there a straight cylinder of sufficient length to form the neck. A small ring, able to fit through the neck of the finished shell, can be used to hold the sections together at the bottom by fitting into a groove at the inner edge of the sections. This eliminates the need for a breakover chuck. Because section chucks are complicated and time consuming to make and use, they are avoided whenever possible. While several standard alternatives are available, I have designed a sleeve or ring chuck which is particularly flexible.
As already mentioned, holding chucks can be used to neck or completely close straight-sided shells, and are often used in conjunction with special follow blocks. Holding chucks are usually concave and either fit the entire shell snugly or at stress points only. Often slotted radially to provide spring-like fingers for a tighter fit, they are sometimes lined with felt for the same reason and to minimize marring the shell. The areas of the shell protruding from the chuck can be worked to almost any shape, usually on air, sometimes with specially shaped followers. Other uses include turning under rims, assembling two or more parts and holding expendable chucks.
Rings for Support in On-Air Spinning | |
Waste, or expendable, chucks are usually made of cheap, easily formed or molded materials and are included as part of the final product. Of course expensive, finely finished materials can be used. They are used when the shell is of extremely complex design or when some property of the waste chuck itself is desirable.
Rubber Rings for Ridges |
The cylindrical chuck is the most versatile when used as a mandrel. With this chuck the position of sleeves or rings can be changed during the course of the spinning to form a great variety of shells. The sleeves can be held in place with bands of masking tape on either side, set screws or a simple friction fit. One sleeve may act as a mandrel for another and may have any contour, the only rule being not to lock the ring into the shell by spinning into an undercut (unless, of course, the ring is a waste chuck). Rings can be made of an elastic material, locked in, and then removed after the shell has been removed from the mandrel. The rings act as integral backsticks to support the work in progress. The use of concave follow blocks to act as holding chucks can aid in maintaining control while using sleeves or rings (or, when the rings are removed, spinning on air).
To fully utilize this system, it is necessary to have mastered the skill of spinning on air. In a sense, all spinning is spinning on air in that the workpiece is not in contact with most of the chuck during much of the forming process.
Note: new source of used lathes: Hayden Machinery, Meriden, CT 06450
James Seavey is a graduate of the Rhode Island School of Design where he studied with John Prip. He has worked as a designer-craftsman for Gorham Silver and Old Newbury Crafters and as a plant manager for Faithcraft International. Currently he makes and markets Pewter holloware under the name Halibut Point Pewter in Gloucester, MA
Related Articles:
You assume all responsibility and risk for the use of the safety resources available on or through this web page. The International Gem Society LLC does not assume any liability for the materials, information and opinions provided on, or available through, this web page. No advice or information provided by this website shall create any warranty. Reliance on such advice, information or the content of this web page is solely at your own risk, including without limitation any safety guidelines, resources or precautions, or any other information related to safety that may be available on or through this web page. The International Gem Society LLC disclaims any liability for injury, death or damages resulting from the use thereof.
Related Articles
Heat-Induced Web Textures on Anodized Aluminum
Maximizing Refining Returns
Inquartation and Parting Refining Process
Refining Gold Jewelry Scraps
The All-In-One Jewelry Making Solution At Your Fingertips
When you join the Ganoksin community, you get the tools you need to take your work to the next level.
Trusted Jewelry Making Information & Techniques
Sign up to receive the latest articles, techniques, and inspirations with our free newsletter.