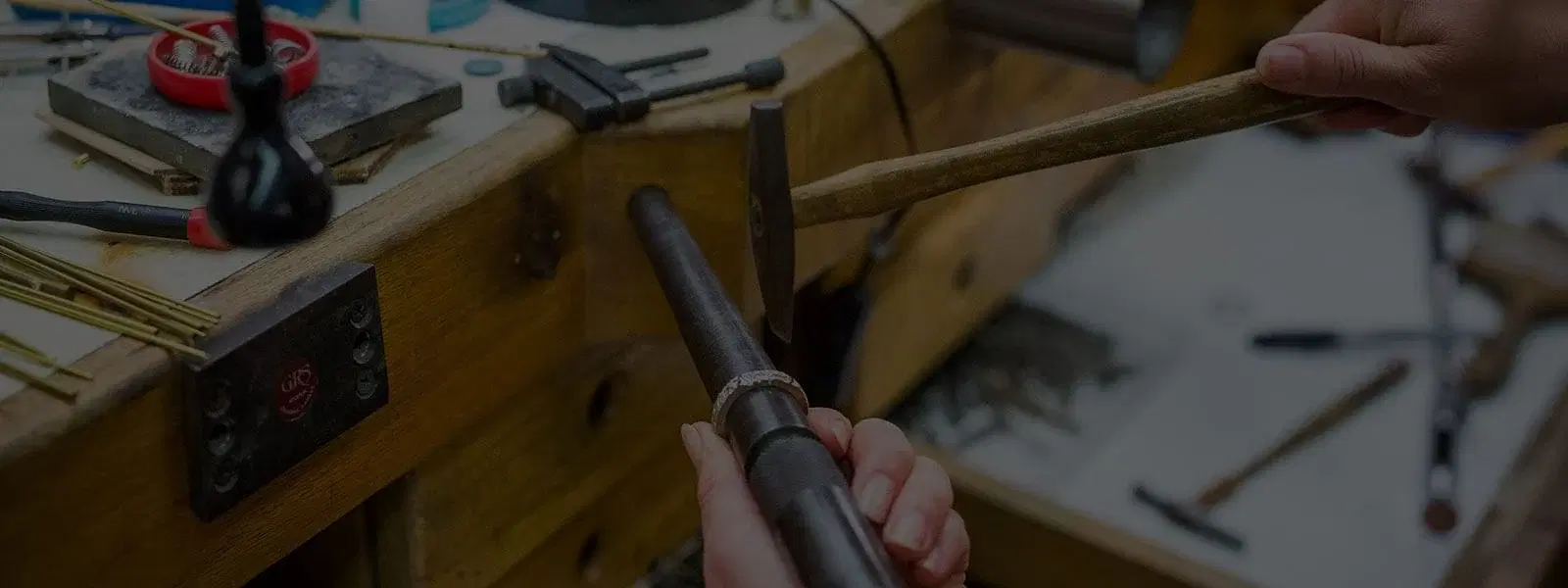
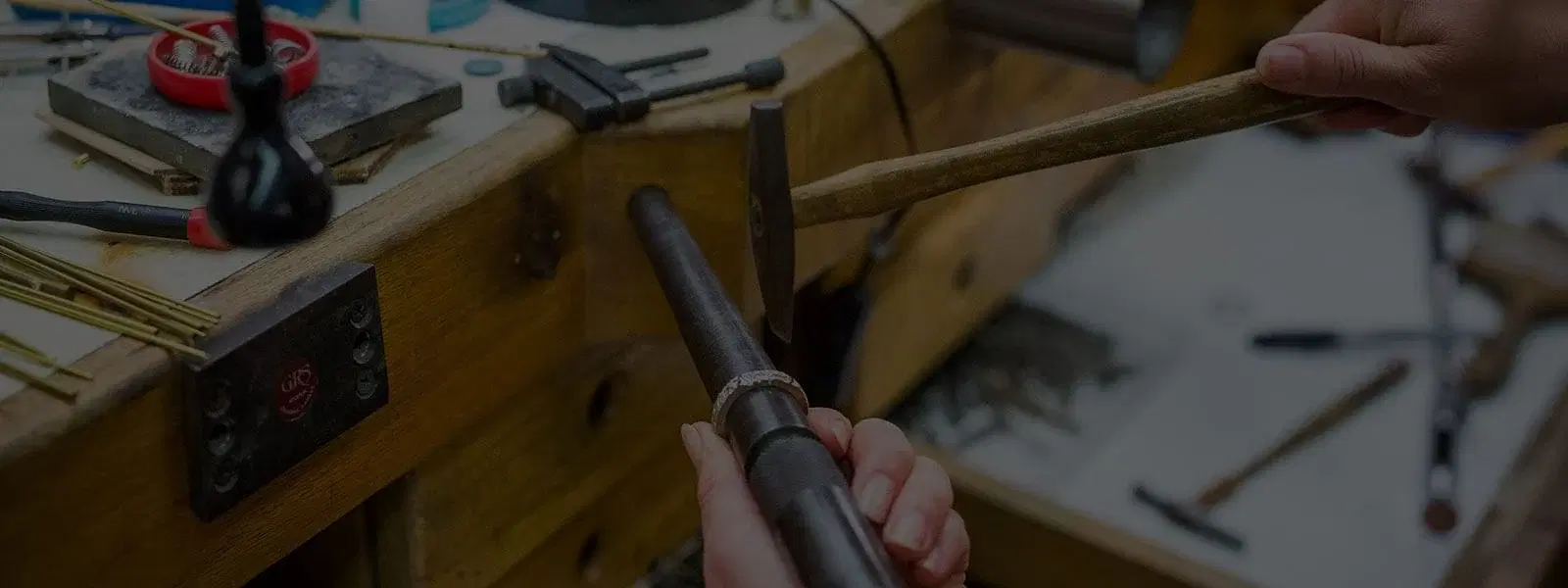
Metals For Enameling
The most commonly used metals for enameling are pure copper and fine silver. The fine silver is primarily used for jewelry because of its cost, color and the advantage of not producing a firescale coat like copper does when it is fired. The copper is the most used metal for enameling for many reasons.
8 Minute Read

This article lists the type of metals for enameling, as well as, how to clean or prepare them for use.
Copper
The most commonly used metals for enameling are pure copper and fine silver. The fine silver is primarily used for jewelry because of its cost, color and the advantage of not producing a firescale coat like copper does when it is fired. The copper is the most used metal for enameling for many reasons: its malleability, its color, availability, and cost. In addition, it usually maintains its shape in the firing process.
The appropriate gauge (thickness) of the metal depends on what is being made. Most plates and vessels are usually 18 ga while jewelry can range from 28 ga for a repousse piece to 14 ga for champleve. The smaller the gauge number, the thicker the metal. If pure copper is to be ordered from a mill, it is necessary to specify the form, such as sheet, wire, etc., the gauge and the end use (enamel on copper). The Thompson Enamel Workbook specifications are "oxygen free, high conductivity copper, conforming to ASTM specifications B 170." I do use the 20 ga sheet copper from a plumbing supply company for pieces up to 4 " x 10 " with about five firings and I have not had any problems. I have not used it for more firings because the need has not arisen.
Base Coated Steel
I have used steel in flat 12 " squares that came with their undercoat and base coat already fired. If I overfired them so that they warped, it sometimes was impossible to flatten them even though they were fired and weighted many times to try to correct the warping. Copper is more forgiving if it becomes warped. Steel needs a special undercoat before the base coat is applied. Purchased with the base coats, the pieces only need to be degreased with a detergent before enameling.
Fine Silver
I usually dome jewelry that I fabricate of 26 ga or 28 ga fine silver or oxygen free copper. Doming the thin gauge metal gives it added strength and keeps the piece of jewelry, especially pins, from being too heavy. I often leave the 18 ga and 20ga fine silver flat. I do counter enamel all of my enamels. Many enamelists say that there is less probability of the enamel cracking if the base coats have the same enamel.
Cloisonne Wire
I like to purchase both fine silver and fine gold cloisonn? wire that is not annealed because it is easier to make a straight line with the wire stiff and it is easy to anneal it for intricate lines. To anneal the wire, loosely and carefully wind it into a three to four inch roll and fire. To test whether the wire is annealed when you take it out of the kiln, bend back one end; if it stays bent, it is annealed and if it does not, it needs additional firing.
Foils
The only foils I have used are the standard 24K gold and fine silver and also a heavier fine silver foil known as "clutch" silver. Although many enamelists pierce the foil, I never do, even though I have used the full 3 " square sheets on enameled pieces. Jean Jenkins places the foil, after she cuts it, on an anti static sheet. I cut a sheet of foil between two pieces of tracing paper with various sized sharp scissors. I have a 10″ pair that I use for long diagonal cuts. The foil is placed on the enameled piece with a water dampened #1 liner brush. Additional water is added to the piece if the foil needs to be repositioned. The water is drawn off with a paper towel by pressing down on the towel. If the foil does not adhere to the enamel surface after the water dries, then add at 1:2 diluted gum and wait until it dries to fire the piece.
For the first firing of the foil, I often sift about a 1/4 " circle of soft flux on an area that has no foil. This spot of flux will tell me when the foil is fused. If you overfire the foil in the first firing, you will destroy it. After the first firing, I smooth the foil with a glass brush. The foil can be fired higher after there are two layers of transparents over it.
Cleaning Copper by Buffing Wheel
If you use primarily transparent enamels, any marks on the metal surface will show. A bright surface enhances the brilliance of transparent enamels. To achieve the surface on copper, I use the buffing wheel. Caution: Although I have an exhaust system, I wear a nose mask, a face mask, a shower cap and cotton or leather gloves. To be safe, you need to know how to use the equipment.
I use a 5 " cotton goblet buff charged with Lea Compound C, a greaseless compound for copper in a metal tube. Cut off about 2 " of the tube, remove the wrapping, and place the piece of compound in a small glass jar with just enough water to cover the compound. The jar needs to be tall enough for you to stir the compound after it is soft. Left overnight, the compound absorbs the water and is soft enough to be stirred into a smooth paste. I apply a thick coat of the compound paste to the goblet buff mounted on the spindle of the buffing wheel. A stiff, small, metal spatula works well for spreading the compound on the buff. I usually let it dry overnight to a hard, crusty state. I soften the cutting action of the buff by first giving a few swipes with a piece of scrap copper across the spinning charged buff. You can clean over twelve 6 pieces before the buff needs to be recharged.
You can also apply the Lea Compound C directly to a buff on a spinning spindle at 1725 rpm by holding the open end of the compound tube again the buff. This thin coating on the buff will dry within five minutes and then you can buff the piece. Charged this way, the buff will need to be recharged with the compound after a few pieces.
I buff the front of the piece first and the back second. By buffing the front first, the finger marks on the back will be removed when you hold the piece by the edge to but the back of the piece. If it is difficult to hold the piece by its edge, I wear clean white cotton gloves to buff the second side.
The Lea Compound C is stored with the cut end standing tightly inside a small, metal, frozen juice can with a wet paper towel in the bottom to prevent the compound from drying out.
Cleaning Copper in an Acid Bath
The first rule for using acids is ADD ACID TO WATER, NOT WATER TO ACID. The most commonly used acids for removing firescale from copper, sterling, and gold alloys are commercial grade nitric acid and Sparex 2, an acid type cleaning compound in granular form. Acid diluted in water is called a "pickle."
Jewelers often say, "pickle it." The solution can be used in a hard rubber photography tray, a Pyrex container, or an electric slow cooker. The pickle works best when warm, but it should not be allowed to boil. Although Sparex 2 is considered a "safe" acid, both the nitric acid solution and the Sparex 2 will cat holes in fabric. The weaker the solution, the slower the biting action.
The recommended solution for the Sparex 2 is 10 ounces by weight in warm water to make a quart of solution. I have only used the Sparex 2 in the electric slow cooker after soldering silver or gold jewelry. I do not clean the copper with acid, but other enamelists explain how they use it and dispose of the acid. The other rule when using an acid bath is use wooden or copper tongs. Tongs made of iron will contaminate If a deep container is used for the acid bath, wear special, long, heavy rubber gloves when you reach into the tank.
Cleaning Copper by Hand
Each enamelist has a preferred product for cleaning copper. Among the ones I have used are a liquid dish detergent, a rag soaked in vinegar and dipped in salt, and a scouring powder with a scouring pad. I prefer Penny Brite. I have used it for over twenty years. It is a copper cleaner with the right ph. I place a number of small pieces, or one 12 " plate, on the wooden board across the top of a set tub.
This board for cutting vegetables at the sink, is sold in kitchen supply stores. I rub one side of all the pieces with a scouring pad and Penny Brite, then turn them over, clean the other side, and rinse them well. The piece is grease free if the water sheets off (does not bead). Sometimes I wear rubber gloves. I place each piece in the dish strainer, dry them with a cotton towel, and if I am not coating the backs with liquid black enamel at the time, I wrap each piece in paper. If I am ready to brush on the crackle, I place each piece, back side up, on a bottle on the nearby table.
If the water, gum, or crackle pulls apart (coagulates) while you brush it on, you can clean the spot with a little enamel, crackle, or saliva to remove the grease from that small area.
Cleaning Fine Silver
I clean fine silver in the kiln. I first put a number of fine silver, jewelry size pieces, on trivets into a 1500 F kiln to remove any grease or discoloration. I peek into the kiln to check whether they arc clean. Fine silver is silvery white when clean. When the pieces are cool, I rub one piece at a time with 000 steel wool. A piece is placed on a small sheet of typing paper, and one corner of the paper is turned over a small part of the piece to keep the oil from my finger off the metal. My finger keeps the piece from moving. I rub in one direction over the face of the piece, usually from top to bottom. The clean pieces are placed face side down on a clean sheet of paper about 2 " apart for a base coat of very thin crackle. I use the fine silver for cloisonn? pins and pendants.
You assume all responsibility and risk for the use of the safety resources available on or through this web page. The International Gem Society LLC does not assume any liability for the materials, information and opinions provided on, or available through, this web page. No advice or information provided by this website shall create any warranty. Reliance on such advice, information or the content of this web page is solely at your own risk, including without limitation any safety guidelines, resources or precautions, or any other information related to safety that may be available on or through this web page. The International Gem Society LLC disclaims any liability for injury, death or damages resulting from the use thereof.
Related Articles
The Metal Corrugation Project
Enamel is Glass — But, What is Glass?
Pickling Notes
The Influence of Enameling
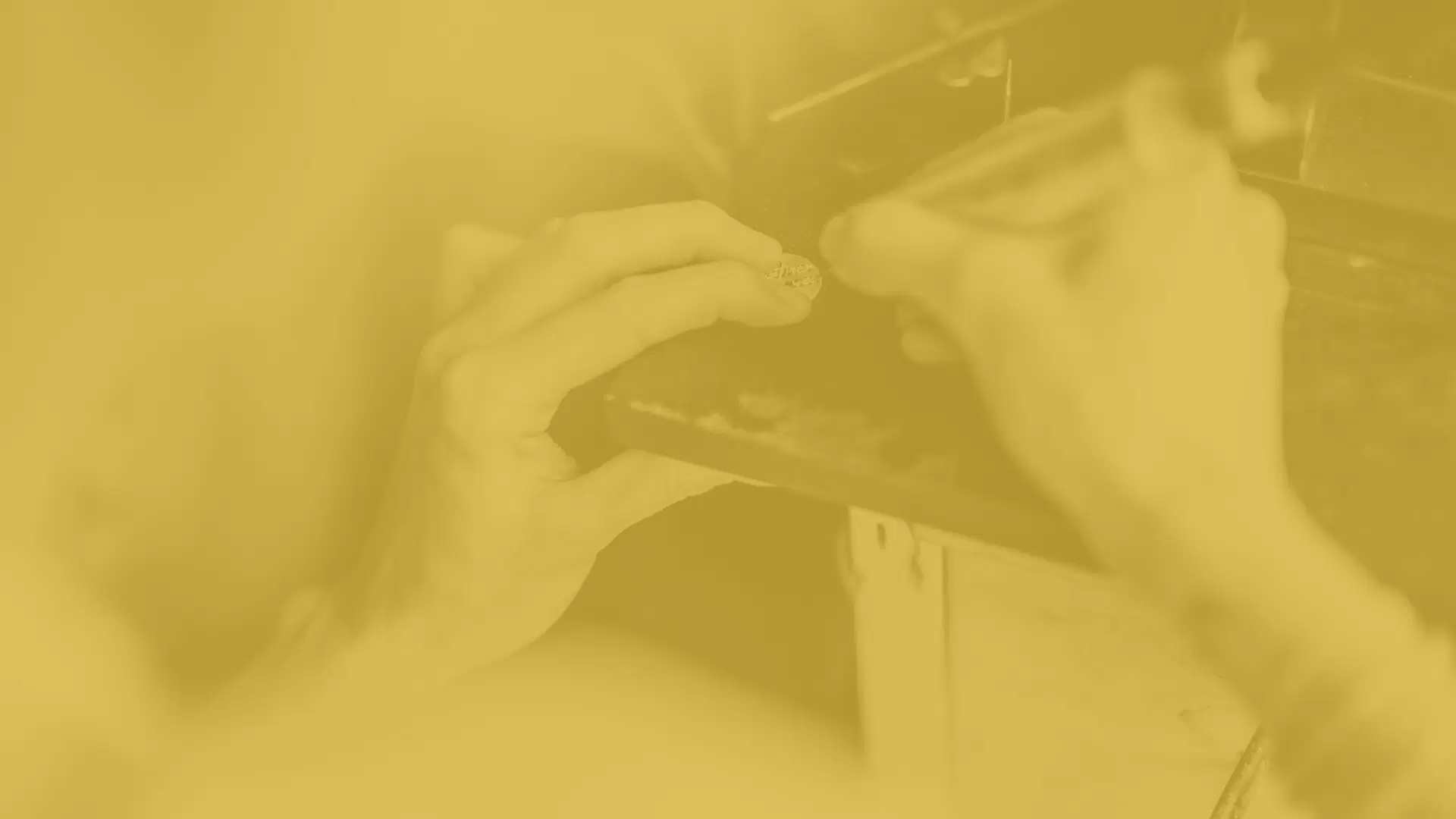
The All-In-One Jewelry Making Solution At Your Fingertips
When you join the Ganoksin community, you get the tools you need to take your work to the next level.
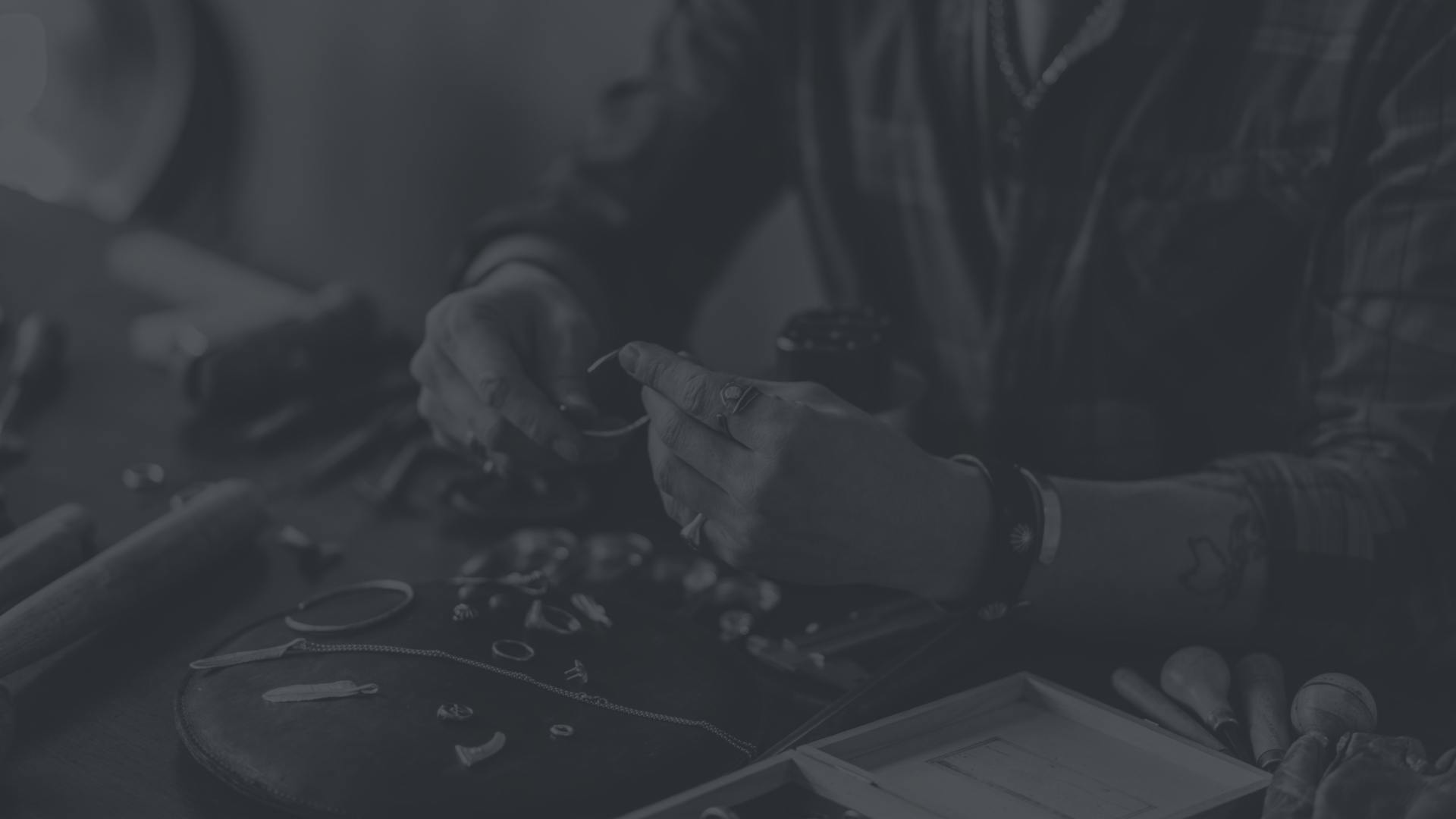
Trusted Jewelry Making Information & Techniques
Sign up to receive the latest articles, techniques, and inspirations with our free newsletter.