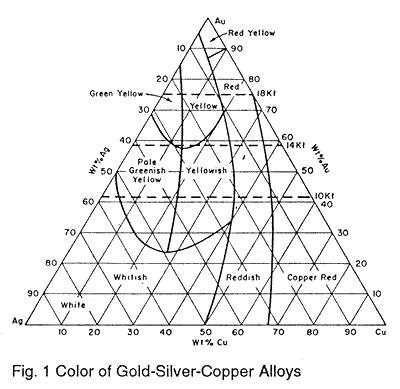
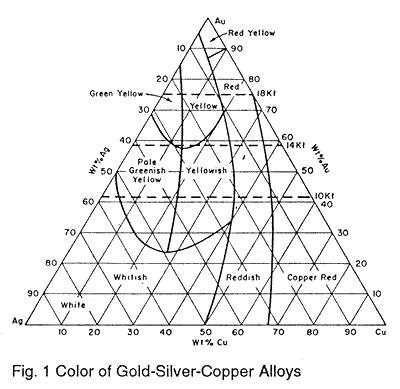
Metals Suitable for Enameling
The purpose of this article is two fold. First, we receive a number of inquiries as to whether or not certain metals can be enameled. This article will answer most of those questions. Second, we have all read statements such as, 'Gilding metal can be fired no more than two times,' or 'Platinum can not be enameled because it has a terrific expansion.' Such statements were based on observations of a limited range of materials. We will show why the statements are misleading.
35 Minute Read
The purpose of this article is two fold. First, we receive a number of inquiries as to whether or not certain metals can be enameled. This article will answer most of those questions. Second, we have all read statements such as, "Gilding metal can be fired no more than two times," or "Platinum can not be enameled because it has a terrific expansion." Such statements were based on observations of a limited range of materials. We will show why the statements are misleading.
We are not recommending any one switch to other metals. Nor, do we wish to infer one metal can replace another and the enameled product have the same characteristics. Actually each combination of metal and enamel will have their own unique properties, some interesting and some not so interesting. Our aim is to provide some fundamental information to those who may wish to experiment and extend their work. Most metals in general use can be coated with enamel.
This does not mean an enamel selected at random can be used successfully on a randomly selected metal. Nor, does it mean any particular property such as high gloss, color, acid resistance, etc. can always be provided by an enamel which can be applied to a given metal. Nevertheless a great number of metals have been enameled with custom made enamels to provide certain engineering properties as well as aesthetic values. The enamel, technique of application, and firing conditions must be carefully selected for each metal based on the following properties of the metal:
- Melting or solidus point.
- Coefficient of expansion.
- Modulus of elasticity.
- Oxidation characteristics.
- Solubility of its oxide in enamel.
- Strength at enameling temperature.
- Ability to absorb and give off gasses when heated to enameling temperature.
- Porosity.
It is obvious the melting point of a pure metal or the solidus (temperature at which an alloy has completed solidification) of an alloy must be somewhat higher than the firing temperature of the enamel. The expansion of the enamel must always be lower than that of the metal. However, there is a limit as to how much variation is permissible. The modulus of elasticity of the metal has much to do with how great this variation can be. The lower the modulus, the greater variation permissible. The rest of the properties will be discussed below for each metal.
GOLD
Melting Point 19480F
Coefficient of Expansion - 425 cm/cm/0C x 10-7
Modulus of Elasticity - 13,000,000 P.S.I.
Gold is an ideal metal for enameling. It shows no appreciable solubility for hydrogen, oxygen, or nitrogen. Because of its medium high melting point, medium coefficient of expansion, and low modulus of elasticity it is easy to formulate enamels which are compatible and still possess the excellent properties the artist desires. It does not form oxides which affect transparent enamels, allowing them to be more brilliant and clear than over any other metal.
Naturally the yellow color of the metal will have some affect on the color of transparents. The final product does not tarnish and the intrinsic value is unequaled. Opaque enamels work well over gold, but normally are used only for accent. Otherwise it appears wasteful since opaques look equally well on cheaper metals. The only complaint about gold, other than cost, is its softness. Uncoated areas scratch easily, therefore articles should be designed so all areas are protected from impact and abrasion.
Enamels which fire between 1300 and 16000F and having an expansion between about 250-350 are suitable.
The purity of gold is expressed in Karats. The term "Karat" means a 24th part and is used to express the weight proportion of pure gold in an alloy. Pure gold is 24 kt., 18 kt. alloy contains 18/24 or 75% gold, 12 kt. alloy contains 12/24 or 50% gold, etc.
Gold is frequently alloyed with silver, copper, zinc, platinum, palladium, cadmium, nickel, etc. to decrease its cost, increase its hardness, or to change its color. Normally only the alloys with silver, copper, and occasionally platinum or nickel are used for enameling.
Each alloy will have a different solidus point, coefficient of expansion, modulus of elasticity, oxidation characteristics, etc. The color of transparent enamels applied over the alloys will be affected by the change in oxidation characteristics and the amount of oxides dissolved.
Both transparent and opaques will be affected by the change in expansion and modulus of elasticity of the metal. Additions of copper increases both the modulus of elasticity and expansion. Additions of silver reduces the modulus of elasticity and increases the expansion far more than copper additions. Thus as copper additions increase enamels with expansions in the lower ranges should be eliminated and total thickness of coating should be reduced.
As silver additions increase it is wise to use higher expansion enamels, however the lower modulus of elasticity resulting from the silver additions makes the system a little more forgiving as to thickness of application and range of permissible expansions. Even though an enamel color works well on gold there is no reason to assume it will work on a gold alloy. And one which fits a gold-silver alloy may chip off a gold-copper alloy. The reason is not an alloy which is no good, but an enameler who selects enamels by color with no attention to the primary properties, firing temperature and coefficient of expansion.
Fig. 1 shows a triaxial diagram of gold-silver-copper alloys.1 Each apex represents 100% of the metal indicated. As the percentages of the three metals change the resulting alloys vary in color. These variations in color will affect the color and brilliancy of transparent enamels, especially paler shades. The areas labeled "Red" and "Reddish" contain more copper and thus more oxidation takes place. The combination of enamel dissolving this oxide and the reflectance from the red metal results in dark muddy transparent colors. The "Green Yellow" area imparts a brownish tint to reds and mauves. The "Greenish Yellow" area produces good transparent colors, however the expansions of alloys in the area are high. Enamels with expansions lower than about 300 should be carefully observed. The areas producing the best transparent colors are "Red Yellow," Yellow," and "Yellowish." Obviously these colors are obtained by using approximately equal parts of silver and copper along with the appropriate amount of gold.
The solidus temperature of alloys must be considered in selecting a proper enamel. Considerable trouble may be encountered if the solidus temperature of an alloy is assumed to be proportional to the melting points of the individual metals used to make the alloy. The melting points of gold, silver, and copper are 19480F, 17610F and 19820F respectively, however the solidus temperature of most alloys containing these three metals is below the melting point of silver. Fig. 2 gives an indication of the solidus temperatures of gold-silver-copper alloys. Although constructed using data from a number of sources its accuracy is sufficient to illustrate the problem. 18 kt. alloys containing equal parts of silver and copper should be enameled with enamels which fire no higher than about 15000F. Lower karat alloys containing equal parts of silver and copper must be fired at lower temperatures. Thompson's Low Temperature - High Expansion enamels work well when fired at 10500F on the lower alloys.
WHITE GOLD. There has been very little information published concerning the enameling of white gold. Older literature describes white gold as alloys of gold and platinum. Today white gold usually contains nickel. The low coefficient of expansion of platinum indicates lower expansion enamels must be used. We have not enameled alloys of gold and platinum. If we were to try we would start with enamels with an expansion of no more than 300 for 18 kt. As more platinum is added we would decrease the expansion of our enamel, perhaps for 10 to 12 kt. we might use Thompson's Medium Temperature - Low Expansion enamels which have expansions just under 200 and fire at 1400-14500F.
See "Gold Alloy" under PREPARATION OF THE METAL, Thompson Enamel Workbook, pg. 16. This procedure is recommended for enameling gold alloys.
We have a limited experience enameling white gold containing gold, copper, and nickel. We see no reason why these alloys would be selected as a base for enameling. However, it is possible they might be selected as the best metal for certain jewelry because of other properties with which we are not familiar. Since there may be occasions where some enameling might be desired as an accent it is well to be familiar with the alloys.
Both nickel and copper will increase the modulus of elasticity. Nickel additions will increase the expansion slightly and copper additions will moderately increase the expansion. The solidus temperatures are well above 17000F. The normal enamels used on copper are compatible, however those with lower expansions should be carefully observed, especially when coating the lower alloys.
The amount of oxidation increases as the percentage of alloying metals, especially copper, increases. This affects the color and clearness of transparent enamels. For some reason, undetermined at this time, the affect is much more serious when lead bearing enamels are used. The oxide formed is difficult to remove by pickling. Thus, there is some problem removing fire scale from areas not covered with enamel.
One shipment of 14 kt. alloy, consisting of 58.33% gold, 12.00% nickel, and 29.67% copper produced an unusual problem. The first fire appeared to release considerable gas. When coated with a lead bearing flux, the entire surface flaked off in one piece. These flakes contained several small spherical areas as though bubbles of gas had tried to escape but the molten enamel was too viscous to allow it to escape. The surface of the metal was bright and free of oxide indicating the gas was probably reducing in nature, perhaps containing hydrogen. Recoating the surface with the same enamel, with no surface treatment, produced a good coat of enamel other than being an ugly dark gray. Thompson's lead free 2010 flux adhered well on the first fire but there were always a few small areas of oxide where apparently the gas had escaped, and the enamel could not flow back completely. These spots coated satisfactorily with a second coat. The enamel was clear and transparent. The metal surface seen through the enamel was copper colored.
The above observations were made by running several samples with the same result on all samples. Although, we did not have enough of this particular shipment of alloy to determine the complete nature of the problem it definitely appeared transparent enamels would not produce the quality desired. Opaque enamels were satisfactory providing the metal was first out-gassed at 14500F.
We have not experimented with this same alloy made by another supplier. Therefore, we do not know whether the above is a characteristic of this alloy when obtained from all suppliers or if the problem is unique with this one supplier. Since this alloy is almost one third copper there may be a hydrogen diffusion problem as discussed below in the copper section.
Many proprietary casting alloys contain a small amount of zinc as a deoxidizer. It also produces a fine grain casting. If the zinc additions are appreciable the solidus temperature will be reduced quite rapidly. Fig. 3 shows the rather strange solidus curve of gold-zinc alloys. As little as 4% zinc lowers the solidus point enough to prohibit the use of normal enamels used on copper. More than about 27% zinc prohibits the use of any enamel normally available.
PLATINUM
Melting Point 32250F
Coefficient of Expansion - 270 cm/cm/0C x 10-7
Modulus of Elasticity - 24,000,000 P.S.I.
Several references indicate platinum can not be enameled because it has a terrific expansion. Actually it has a very low expansion. In general, metals with high melting points have low expansions and metals with low melting points have high expansions. The same is true for glass. Glasses with high softening points generally have low expansions, and glasses with low softening points generally have high expansions. Both Thompson's Medium Temperature - Low Expansion enamels fired at 14500F and their High Temperature - Medium Expansion enamels fired at 16000F work very well on platinum.
SILVER
Melting Point 17610F
Coefficient of Expansion - 600 cm/cm/0C x 10-7
Modulus of Elasticity - 10,500,000 P.S.I.
Fine silver, by definition contains at least 99.9% silver. "High" fine silver contains at least 99.95% silver. Laboratory refined or "spectroscopically pure" silver is at least 99.999% silver. Gas content, in particular oxygen, is not specified in any specification.
Fine silver is a popular metal with enamelers. There is no fire scale to contaminate the working area. The white color does not appreciably affect the true colors of transparent enamels which appears very clean and brilliant when properly fired. Transparent reds are normally fired over silver flux while other transparents are fired directly on the silver surface. Caution should be taken not to over fire transparent enamels on silver. Over fired fluxes may have a yellow tint. Other transparent colors may appear as though they were applied over a yellow base coat. The coefficient of expansion of silver is quite high and enamels with expansions less than 290 should be carefully observed for cracking.
Fortunately its modulus of elasticity is quite low, otherwise it would not be possible to use enamels normally used on copper. As pointed out in Vol. 2 No. 3, P. 30, enameled silver articles grow considerable with each fire, because of silver's high expansion and low modulus of elasticity. As a result it is difficult to construct and enamel silver boxes where a lid must fit a base, or other items which are to be fitted together.
If a silver ingot is chilled rapidly it becomes case hardened and a certain amount of free oxygen is imprisoned in the center of the ingot. When rolled into sheet the oxygen remains in the center. When the enamel is fired the oxygen is gradually driven off. It escapes from the surface of the silver which is not enameled, but is imprisoned at the interface of the metal and enamel. The metal oxidizes and the oxide can not decompose as it would if exposed to air. If the enamel is transparent a discoloration can be seen at the interface. After several fires the enamel may crack and perhaps break away. Fortunately, today this problem is rarely encountered.
STERLING SILVER
Melting Point 16700F
Solidus Temperature 14720F
Coefficient of Expansion - 540 cm/cm/0C x 10-7
Sterling contains 92.5% silver and 7.5% copper. Alloys with as little as 92.1% silver can be stamped "sterling" in the United States. The thermal expansion is lower than that of silver, and we suspect the modulus of elasticity is somewhat higher. This suspicion is based on reports that some lower expansion enamels which are barely suitable for fine silver are not compatible with sterling. It is far safer to use the high end of the expansion range of enamels normally used on copper. Due to the copper content the alloy will oxidize when heated, thus transparent enamels may lack some brightness and be less clear than when applied over fine silver. Frequently more desirable results are obtained by first applying a flux made especially for silver. Opaque enamels can be applied directly on sterling silver. See "Silver Alloy" under PREPARATION OF THE METAL, Thompson Enamel Workbook, pg. 16. We recommend this procedure for enameling silver alloys.
Fig. 4 shows the copper-silver phase diagram. Both metallurgists and ceramists use phase diagrams to record a large amount of data in visual form. The diagram shown has been simplified to show only the information which is important to the Art Enameler. The amount of each metal is represented along the bottom of the diagram with 100% silver on the left and 100% copper on the right. Temperature is indicated up the side. Three melting points are shown - A, B, and C. A is the melting point of silver at 1760.90F. C is the melting point of copper at 1981.40F. B is the melting point of an alloy at 1434.20F. This alloy consists of 71.9% silver and 28.1% copper. The line ABC is called the liquidus curve. Everything above this line is liquid. The line ADEC is called the solidus curve. Everything below this line is solid. There are two solid phases, alpha and beta. Alpha is a silver rich, solid solution of silver and copper. Beta is a copper rich, solid solution of silver and copper. The two triangles DAB, and BCE are mixtures of liquid and solid. Point B is called the eutectic point. The important information for Art Enamelers is the solidus curve. Firing temperatures should be lower than the solidus temperatures.
The solidus temperature for sterling is about 14700F which is almost 2000 lower than the melting point which enamelers have, for years, assumed was the critical temperature. To allow for inaccuracies in pyrometers and other variables in firing it is well to reduce the firing temperature to 1400-14500F. Our experience indicates enamel with expansions of about 290 or more can be fired many times at a firing temperature of 1400-14500F on both fine silver and sterling. There is also less warpage if the temperature is no higher than necessary. "Quick high fire" enamelers will have a lot of trouble enameling silver and its alloys.
Margaret Seeler2 states sterling casts have a white coating of fine silver which should be kept intact except for the area which is to be enameled in the next firing. Such casts do not tarnish except where the coating is damaged.
Silver alloys other than sterling may be encountered, especially in the form of castings. We find no published information on the enameling of silver alloys other than sterling. This may be due to the low solidus temperature of alloys between Points D and E in Fig. 4. This also shows graphically why a problem happens occasionally when doing cloisonn? with silver wire on copper. If the silver wire penetrates the enamel and touches the copper base a melt down can occur at temperatures of about 14340F and above.
Obviously there is a problem enameling the lower melting alloys with enamels normally used on copper. Thompson's Low Temperature - High Expansion enamels having expansions of about 450 and firing at 10500F are compatible. Various alloys of silver, copper, zinc, cadmium, tin and nickel can also be enameled with these enamels providing the solidus point of the alloy is not below about 12300F.
Many writers state sterling can be fired only one or two times before the enamel will crack, discolor, etc. We believe these observations were based upon one or more of the following:
- Applying enamels with expansions which were too low for sterling.
- Applying a high expansion enamel on top of a low expansion enamel.
- Firing too hot for sterling. No higher than 14000F is desirable-14500F at the most.
- Using sterling with absorbed oxygen.
GOLD AND SILVER FOIL
The use of gold and silver foil permits the enameler to obtain the brilliance and clarity of transparents over these precious metals at a much lower cost. Pure 24 karat gold and fine silver should be used. Both should remain bright and form no oxide when fired to adhere them to the enamel. If an oxide forms the foil probably contains a small amount of copper. In most cases the small amount of oxide will be dissolved by the enamel fired on top of the foil.
Mitzi Otten and Kathe Berl3 described the use of leaf gold. Apparently this is thinner than normal foil. It was applied to an enamel surface and judicially fired to produce a smooth gold texture. Apparently they did not put enamel on top of the gold leaf. Its hue and brilliance varied according to the background enamel color onto which it was applied.
It is interesting to note De Koningh4 as well as Otten and Berl5 use the word paillons only to describe small ornamental shapes stamped from foil with small steel punches. The larger shapes cut with small scissors or a sharp knife they merely call "thin sheets" or "cut outs
COPPER
Melting Point 19820F
Coefficient of Expansion - 500 cm/cm/0C x 10-7
Modulus of Elasticity - 16,000,000 p.s.i.
The most popular metal used by Art Enamelers is copper. It is compatible with enamels having expansions of about 250 to 375. Its melting point permits the use of enamels which fire as high as 16500F, however adequate supporting fixtures are a major design problem to prevent warpage at temperatures in excess of 15000F. A wide range of enamels, both transparent and opaque, with desirable properties are compatible with copper.
As copper comes from the smelter it is 99% pure. The impurities are removed by an electrolytic process where the impurities fall to the bottom of the tank and the 99.9+% copper deposits on a plate known as a cathode. The cathodes are then melted and cast into suitable shapes for processing. During this last operation some copper oxide forms and becomes distributed as inclusions between the copper crystals. This type copper is sold as electrolytic copper.
At temperatures higher than 7520F hydrogen will diffuse into copper containing copper oxide and reduce the oxide to copper and water vapor. The water vapor then diffuses to the surfaces of the copper. The water vapor which arrives at the interface between the copper and enamel will cause bubbles in the enamel and in extreme cases affect the adherence.
If during this last manufacturing process of melting and casting into suitable shapes a blanket of protective gas is present at all times to prevent the copper from coming into contact with air it will not oxidize. This product is sold as "oxygen free, high conductivity" copper, conforming to ASTM specifications B-170. The electronics industry uses this type for glass to metal seals, but they demand a certification which includes a scale adherence test and a composition stipulation as follows:
- Copper 99.96% minimum (silver counts as copper)
- Phosphorous 0.0003% maximum
- Sulfur 0.0040% maximum
- Zinc 0.0003% maximum
- Mercury 0.0001% maximum
- Lead 0.0010% maximum
The scale adherence test consists of heating a specimen for 20-30 minutes at 15620F and quenching in water. If the entire specimen retains red copper oxide the copper is accepted.
The following incident shows the importance of selecting the proper copper. A customer who produces a line of giftware using fire scale as a major part of the design found several shipments of copper on which the scale would not adhere. Several changes in firing procedures were made but the results were the same. We sent the customer a few pieces of our stock copper and the scale adhered as in the past. We ran an analysis on both types of copper and found the following:
Pieces of each were heated to 15600F for 25 minutes and water quenched. The suitable copper retained a complete layer of red copper oxide with a few small areas of black oxide. The unsuitable material showed a bright copper surface where all of the scale had popped off. The test was repeated allowing the metal to air cool after being removed from the furnace. The suitable material retained a complete coat of black oxide. Underneath this black oxide was, of course, a layer of red oxide. The unsuitable material retained no scale, red or black. The difference in the two materials was the phosphorus content. Phosphorus was probably added as a deoxidizer. Both of the coppers appeared to enamel satisfactorily. We strongly suspect a further increase in the phosphorus would cause adherence problems.
Webster, Christie, and Pratt6 reports scale adheres firmly to OFHC copper when formed at 14700F or higher, and to tough-pitch copper when formed at 15600F, but has a tendency to come off the phosphorized copper. The difference between OFHC and electrolytic tough-pitch copper is in oxygen content.
It appears electrolytic copper is the least an enameler should specify. To be absolutely safe, oxygen free high conductivity should be specified. Roofing copper purchased from the local hardware store can produce serious problems for the enamelers.
BRASS AND BRONZE
Traditionally brass is an alloy of copper and zinc, while bronze is an alloy of copper and tin. In practice, it has been a tendency and nothing more. There are many examples in literature where the terms have been used interchangeably. Even today commercial bronze is an alloy of copper and zinc. In general brasses contain zinc in amounts varying from about 5% to about 45%, while alloys with aluminum, silicon, tin, and some other metals are called bronzes. Fig. 5 shows the solidus curves for copper-zinc and copper-tin alloys.
GILDING METAL
Gilding metal contains 95% copper and 5% zinc. De Koningh7 indicated the smelters and refiners were rather secretive in the 1920's and normal gilding metal at that time was probably 90% copper and 10% zinc when purchased from reputable smelters. Other smelters used 30 to 60% zinc, tin, antimony, etc. producing metal which was worthless. He classed tombac with gilding metal but gave no composition. Today gilding metal is controlled and widely used by badge makers. Enamel normally used on copper works well on gilding metal. The expansion of gilding metal is slightly greater than for copper. Therefore the lower expansion enamels used for copper may not always be suitable for gilding metal. Enamels with expansions of less than perhaps 275 should be carefully observed. Many references indicate gilding metal can be fired only two or three times. Our work does not confirm this. We believe the referenced problems were the result of not eliminating the lower expansion enamels from the palette.
The scale adherence test mentioned above shows the different oxidation behavior of gilding metal compared to copper. Heating at 15600F for 25 minutes and water quenching left a thin brown oxide with a slight reddish cast which adhered tightly. Heating at 15600F for 25 minutes and air cooling produced much the same type oxide layer, a thin light brown with a few small spots of black scale with a hint of reddish cast around the edges. This slower rate of oxidation and no doubt its chemical composition are responsible for the improved color and appearance of transparents when applied to gilding metal as compared to copper. Gold ruby red is considerably improved when applied to gilding metal.
COMMERCIAL BRONZE (90 Cu, 10 Zn) (89 Cu, 9.25 Zn, 1.75 Pb) and RED BRASS (85 Cu, 15 Zn) can be enameled with enamels normally used on copper if those with expansions of 300-350 are selected. Thompson's Low Temperature - High Expansion enamels, firing at 10500F for approximately 10 minutes have an excellent potential for enameling these two metals.
LOW BRASS (80 Cu, 20 Zn), CARTRIDGE BRASS (70 Cu, 30 Zn), MUNTZ (60 Cu, 40 Zn) and FORGING BRASS (60 Cu, 38 Zn, 2 Pb) can all be enameled with Thompson's Low Temperature - High Expansion enamels. In some instances the transparents will not be the standard experienced on pure copper, due to the dissolved metal oxides. When the scale adherence test is run on these metals the oxide flakes off both when water quenched or air cooled. The oxide is grayish black.
BRAZING ALLOY. Compositions vary from one manufacturer to another. We have worked with one having the following composition: Cu 56-60, Sn 0.8-1.1, Mn 0.01-0.5, Fe 0.251-0.2, Si 0.04-0.15, Al 0.01 max, Pb 0.05 max, balance Zn. The solidus temperature is 16200F and the expansion is 580. Normal enamels used on copper are not suitable on this alloy. Temperatures required to fire out these enamels causes an evolution of gas which produces a high concentration of bubbles in the enamel. The enamel flakes off as it cools to room temperature. Thompson's Low Temperature - High Expansion enamels work well. Pieces of copper can be brazed together and the entire assembly enameled with the low fire series at 10500F.
NICKEL SILVER (65 Cu, 18 Ni, 17 Zn) enamels well with both regular and low fire enamels. A second nickel silver (55 Cu, 18 Ni, 27 Zn) is not compatible with enamels normally used for copper, while the low fire series work very well.
PHOSPHORUS BRONZES. Phosphorus is often added, as a deoxidizer, to Copper-tin alloys. Two common phosphorus bronzes (94.8 Cu, 5 Sn, 0.2 P) and (88 Cu, 4 Zn, 4 P, 4 Sn) can be enameled with the higher expansion enamels normally applied to copper. Thompson's Low Temperature - High Expansion enamels also have an excellent potential.
NAVAL BRASS (60 Cu, 37.5 Zn, 1.75 Pb, 0.75 Sn) has an expansion of 642 which is not compatible with the usual copper enamels. The alloy can be enameled with Thompson's Low Temperature - High Expansion enamels.
MANGANESE BRONZE (58.5 Cu, 39 Zn, 1.4 Fe, 1.0 Sn, 0.1 Mn) is not compatible with normal copper enamels because of its high expansion and low solidus temperature. Thompson's Low Temperature - High Expansion enamels produce very good results.
ALUMINUM SILICON BRONZE (91.2 Cu, 7 Al, 1.8 Si) is a poor base for normal copper enamels due to the formation of pin holes. Thompson's Low Temperature - High Expansion enamels work very well.
CASTINGS. Bill Helwig reports good results have been obtained in his workshops with castings of the following compositions:
1 | 2 | 3 | |
Copper | 85 | 80 | 75 |
Tin | 5 | 12 | 12 |
Zinc | 5 | 3 | 8 |
Lead | 5 | 5 | 5 |
Thompson's Medium Temperature - Medium Expansion enamels were used on the above castings.
STEEL
Melting Point 27600F
Coefficient of Expansion - 400 cm/cm/0C x 10-7
Modulus of Elasticity 30,000,000 P.S.I.
The availability of suitable sheet steel was probably more responsible than any other single item for the industrial revolution of enameling. The enameling of steel grew steadily until World War II. Following the war growth was very rapid until the mid 1970's when 1-3/4 billion square feet of steel was being enameled per year, just in the United States. Since 1975 the industry has declined. More than 95% of enameled steel is for the appliance market.
Although steel is lower in cost and can be fabricated by mass production techniques it presents some new problems to the enameler. The carbon content causes adherence problems, blisters, pits, etc. The high modulus of elasticity of steel requires the enamel to have a narrow range of expansion values. Enamels which do not fall within the range of 275-330 should be carefully observed for cracking or chipping.
On the other hand steel has higher strength both at enameling temperature and at room temperature. This permits the use of larger size articles without deformation during the firing operation. Also the finished ware tends to be more durable.
A number of highly serviceable enameling iron products are available:
- Low-carbon enameling steels
- Decarburized steels
- Interstitial free steels
- Titanium-stabilized steels
Low carbon enameling steels contain 0.02-0.04% carbon, 0.03-0.07% aluminum and a few trace elements. A ground coat such as GC-16 or GC-17 is required as a first coat.
Decarburized steels are annealed under controlled conditions to eliminate all carbon. Medium Temperature-Medium Expansion Enamels and Liquid Form-Water Base Enamels, can be applied directly to this type steel.
Interstitial free steels are products in which all of the carbon and nitrogen contained in them are combined with an alloying element. Titanium or niobium (columbium) or a combination of the two are used to fully stabilize the steel. Vacuum degassing is used to produce the very low carbon versions. Medium Temperature - Medium Expansion enamels and Liquid Form - Water Base Enamels, can be applied directly to this type steel.
Titanium stabilized steels are a variation of interstitial free steel. Not being vacuum degassed, these steels are somewhat higher in carbon content than interstitial free steel. The carbon is stabilized as titanium carbide by the addition of titanium. Again, Medium Temperature-Medium Expansion enamels and Liquid Form - Water Base enamels, can be applied directly to this type steel.
The only metal preparation required is the removal of any grease, oil, or heavy rust areas. The grease or oil can be burned off at a low temperature and heavy rust removed with emery paper. Production enamelers use more complicated methods to clean and pickle sheet steel prior to enameling, but for small amounts the methods given above are very satisfactory.
Naturally transparents directly on the metal will not have the same appearance as when applied to copper. Generally opaque enamel and the use of foil under transparents would be the proper approach. The entire surface of the steel should be coated prior to the first fire. Any uncoated areas oxidize fairly rapidly at 800F and higher to form a tightly adhering oxide layer. This is more difficult to remove than copper oxide. Although enamel powder can be sifted on, it is easier to use liquid enamel such as Liquid Form - Water Base for the first coat. Both sides can be coated by spraying, dipping, or slushing and fired at the same time. Subsequent coats can be applied using normal techniques used on copper, silver, etc.
Unfortunately few steel warehouses around the country stock the above four steels. We strongly advise a cautious approach to using hot rolled steel, or even cold rolled if the carbon content exceeds 0.10%.
Blacksmithing has become quite popular and several have expressed a desire to enamel some areas of their work using their forge to fire the enamel. A technique which should be ideal for them is one we describe on page 22 of the Thompson Enamel Workbook. We call the technique "hot dusting". It consists of applying dry enamel powder to a hot piece of metal using a sifter, or a small scoop and if necessary spread it around with an iron rod. An alternate method is to roll the hot piece into some enamel powder piled on a metal table top. Any scale on the hot piece should be knocked or scraped off prior to applying the enamel. After applying the enamel the piece is returned to an oxidizing portion of the flame to fire out the enamel.
Depending on the composition of the steel a ground coat may be required as a first coat. It would be applied as a dry powder as described above. A little thought will show how metal shields can be used to keep the enamel from falling on areas where a coating is not desired. Metal shields can be used in creating designs.
SILVER PLATED STEEL
This seems to be the best of both worlds in many ways. It provides the strength of steel to prevent warping during firing and a surface which is excellent for transparent enamels. An enameler planning a sizable run of an article should be able to work out the practical problems of fabricating and plating. We caution about too much aggressive cleaning and pickling which might remove most of the silver plating. Also, firing temperature should not exceed 14500F and the number of firings should be kept to a minimum.
CAST IRON
Melting Temperature 21500F
Coefficient of Expansion - 350 cm/cm/?C x 10-7
Modulus of Elasticity - 13,000,000 P.S.I.
We are not aware of any outstanding art enameling on cast iron, although enameled cast iron cook ware does sell for a good price in some markets. Cast iron used for enameling is classed as gray iron and should fall within the following composition:
Total Carbon 3.25 - 3.35%
Silicon 2.5 - 2.60
Manganese 0.45 - 0.60
Phosphorus 0.60 - 0.70
Sulfur Less than 0.09
Enamels normally used on copper work satisfactorily on good cast iron providing certain precautions are taken. Ideally the surface should be sandblasted, however in most instances it is sufficient to use an electric grinder to remove irregular surface areas such as lumps, projections, ridges, rust areas, etc. We do not recommend any casting whether it be cast iron, cast gold, cast silver, etc. be pickled. Castings usually have a few pores where the pickle solutions hide only to come out as blisters in the firing operation.
Best results are normally obtained if the firing temperature is as low as possible. Select enamels which will fire at 1300-13500F for 20 minutes or more. Sifting is not an ideal method of applying the first coat. At these low temperatures individual enamel grains do not flow out easily. If the surface of the cast iron is exposed between grains of enamel it will oxidize during the long firing cycle. Although a second coat may flow out and cover the entire surface the oxidized areas may produce blisters. The best practice is to use Liquid Form - Water Base enamels for the first coat.
For small articles Thompson's Overglaze Painting Enamel (dry powder) can be mixed with water and applied for the first coat. Cast iron does not require a cobalt bearing ground coat as described above for certain types of steel. Subsequent coats can be normal enamels used on copper if they fire at these lower temperatures. They may be applied by the usual methods. Enamels with expansions of about 240 to 340 are workable on cast iron.
STAINLESS STEELS
300 SERIES (Non-magnetic) This series contains 16-25% chromium, 6-22% nickel, small amounts of special metals, and the remainder iron. Their expansions range from 340 for type 330 S.S. to 520 for type 304 S.S. Their moduli of elasticity are 28,000,000 P.S.I. or slightly higher. These high moduli of elasticity limits the permissible difference in the expansions of the enamel and the alloy being coated. Enamels from the lower end of the expansion range of Medium Temperature - Medium Expansion enamels are suitable for 330 S.S. and those from the higher expansion range are suitable for 310 S.S. The rest of the 300 series requires enamels with higher expansions. Low Temperature - High Expansion enamels are excellent on these higher expansion stainless steels. This series of stainless produces very little oxide at enameling temperatures. Best results are obtained by prefiring the uncoated metal to develop some oxide. Then apply the enamel directly over the oxidized surface.
400 SERIES (Magnetic) This series contains 12-25% chromium, 0-2.5% nickel, and the remainder is iron. Their expansions range from 297 to 350 and their moduli of elasticity are 29,000,000. Enamels with an expansion of about 310 or less can be used on type 431 S.S. The other types of 400 series requires enamels with 270 or less in expansion. Medium Temperature - Low Expansion enamels work well on these other types of 400 series.
SUPER ALLOYS
Inconel contains approximately 77% nickel, 15% chromium, and 7% iron. It has an expansion of 350 and a modulus of elasticity of 31,000,000. Enamels used on copper works well on inconel, however their expansion should be less than about 320. Hastelloy contains 45-80% nickel with miscellaneous metals added for certain properties. They have expansions ranging from 305 to 440 and moduli of elasticity are 24,000,000 to 31,000,000. Hastelloys A, B, C, & D are compatible with enamels from the lower end of the expansion range of normal enamels used on copper, while Hastelloy F & X are compatible with enamels from the higher end. All of the alloys in this stainless steel section require no preparation other than the removal of grease, oil, and ordinary dirt. Grease and oil can be burned off at a low temperature. When cold, loose material can be brushed away. Other methods are washing with soap and water, or scrubbing with liquid enamel such as Liquid Form - Water Base enamel.
Sandblasting is used in production shops. Remember it is advisable to prefire the 300 series to develop an oxide layer. Color enamels go directly on the metal surface without a ground coat as used for cold rolled steel. Some transparents look surprisingly good.
ALUMINUM
Melting Point 12210F
Coefficient of Expansion - 690 cm/cm/?C x 10-7
Modulus of Elasticity - 10,000,000 P.S.I.
The oxidation characteristics of aluminum differ from the metals already discussed. Immediately upon exposure to air aluminum forms a thin transparent oxide film which protects it from further oxidation. As a result pure aluminum does not oxidize further when heated. This means no scale to flake off and contaminate the working area. The oxide has no affect on the appearance of transparent colors.
We recommend enamelers start with alloy 3003. It remains bright and white when heated which is desirable when using transparents. Alloy 1100 also remains bright and white when heated, but it is softer and tends to deform more during firing. Alloy 6061 darkens when heated and thus affects transparent colors, however it normally coats well with opaques. If the alloy contains excessive magnesium spalling is a possibility. Casting alloy 43 is generally suitable for enameling, however its solidus temperature is approximately 11000F and extreme care must be taken.
Low Temperature - High Expansion enamels are used with a firing temperature of 10500F , or slightly lower. Care must be used when the firing temperature approaches 11000F . Ordinary aluminum foil used in the kitchen can be used similar to silver foil when enameling copper. All of the alloys mentioned above require very simple metal preparation. Just pre-fire the metal at 10500F for 5-10 minutes. Alloys other than those mentioned above require special pickling operations.
TITANIUM
Melting Point 30200F
Coefficient of Expansion - 246 cm/cm/?C x 10-7
Modulus of Elasticity - 16,000,000 P.S.I.
Titanium metal was a laboratory curiosity until the late 1940's when suitable production techniques were developed. When exposed to air or moisture a thin film of oxide forms instantly and continues to grow slowly in thickness. The oxide film is transparent in its normal thin configuration and not detectable by visual means. The composition of this film varies from TiO2 at the surface, to Ti2O3, to TiO at the metal interface. The oxides are soluble in enamel causing flux to turn gray. Other transparents are also affected by the dissolved oxides. In general opaque enamels are more suitable for the first coat on titanium. Because of its low expansion titanium can be coated only with enamels having an expansion of about 230 or less. Medium Temperature - Low Expansion enamels work well when fired at approximately 14500F , and High Temperature - Medium Expansion enamels when fired at 16000F .
SUMMARY
The world of enameling is quite large. We know of no metal having a melting point of 11000F or higher which cannot be enameled. The arsenal of enamels provide expansions from about 175 to 450. This provides a "fit" for all metals and alloys with melting or solidus points of 11000F or higher. The interesting and sometimes frustrating thing is to obtain the exact property desired. Today's technology makes it far more possible than ever before. No doubt a hundred years from now it will be even more possible, but every bit as difficult to change the old habits.
REFERENCES:
- Edmund M. Wise. GOLD - Recovery, Properties, and Applications. D. Van Nostrand Co., Inc. New York 1964 P. 262.
- Margaret Seeler. THE ART OF ENAMELING. Van Nostrand Reinhold Co. New York 1969 P. 30.
- Mitzi Otten and Kathe Berl. THE ART OF ENAMELING or ENAMELING CAN BE FUN. Pub. by the authors. 1950 P. 32-33.
- H. De Koningh. THE PREPARATION OF PRECIOUS AND OTHER METAL WORK FOR ENAMELING. Crosby Lockwood & Son. London 1927 P. 19. Ref. #3, P. 31.
- W.R. Webster, J.L. Christie, and R.S. Pratt. "Comparative Properties of Oxygen - Free, High Conductivity, Phosphorized, and Tough-Pitch Coppers." AIME Trans. Vol. 104, 1933. Ref. #4 P. 35-38.
You assume all responsibility and risk for the use of the safety resources available on or through this web page. The International Gem Society LLC does not assume any liability for the materials, information and opinions provided on, or available through, this web page. No advice or information provided by this website shall create any warranty. Reliance on such advice, information or the content of this web page is solely at your own risk, including without limitation any safety guidelines, resources or precautions, or any other information related to safety that may be available on or through this web page. The International Gem Society LLC disclaims any liability for injury, death or damages resulting from the use thereof.
Related Articles
Heat Treating Metals
Martha Glowacki & Fields of Reference
Cloisonne Jewelry with 24k Wires
Kliar Vibrant Colors for Metal Jewelry
The All-In-One Jewelry Making Solution At Your Fingertips
When you join the Ganoksin community, you get the tools you need to take your work to the next level.
Trusted Jewelry Making Information & Techniques
Sign up to receive the latest articles, techniques, and inspirations with our free newsletter.