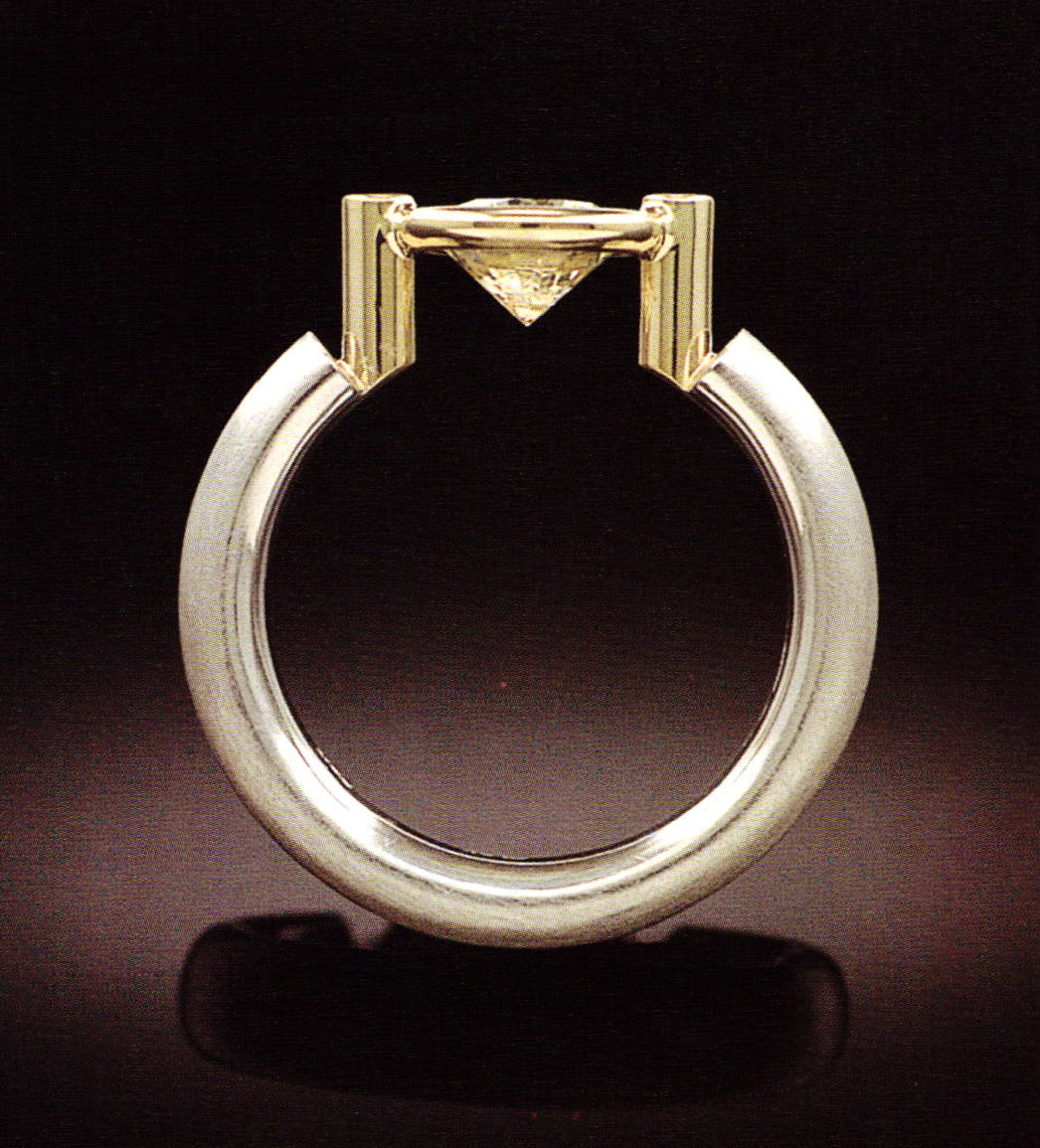
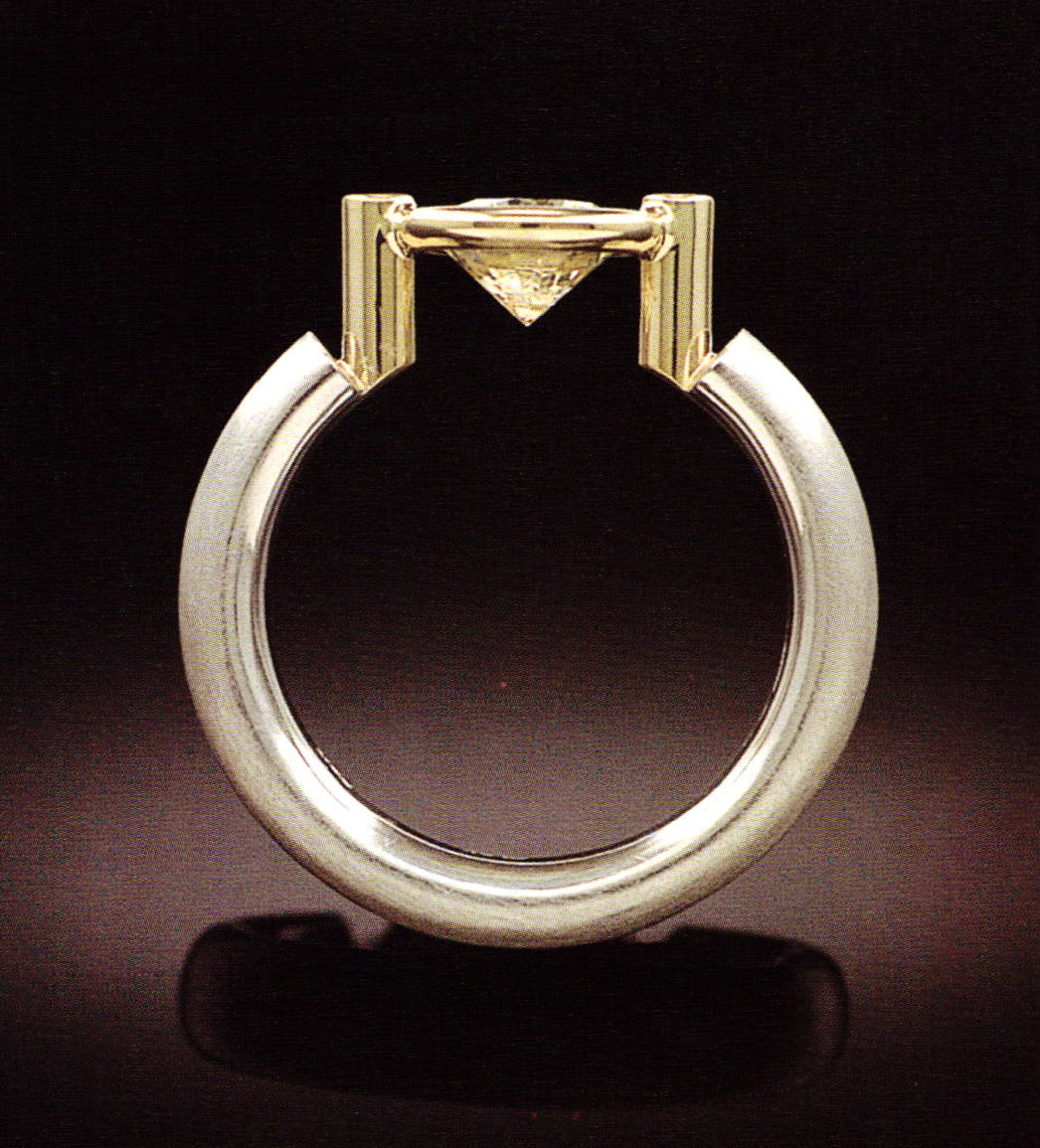
Metalsmith 1997 Exhibition
51 Minute Read
This article showcases various exhibitions published in the 1997 Exhibition issue of the Metalsmith Magazine. This features Greg Campbell, David Baird, Jim Kelso, and more!
~~~~~~~~~~~~~~~~~~~~~~~~
Greg Campbell
San Francisco, California
Greg Campbell's desire for more direct and hands-on involvement with his artwork led him to leave the corporate advertising world where he worked as an art director and graphic designer to become a jeweler. Campbell casts his bold bracelets in epoxy resin. His forms are initially carved in wax and are then silicon-molded, and often, several molded elements are combined in one design.
The bracelets in the top photo are cast in two parts. When the two parts are joined together, a layer of metallic pigment is sandwiched between them. The reflective pigment reflects light back out, bringing a warm luminescence to the softly tinted plastic. By sensitivity mixing muted, transparent colors, and careful hand-finishing, Campbell avoids the industrial feeling so often associated with plastic.
The efficiency of the casting process allows Campbell to retail these pieces for $110. The light weight of the plastic allows the forms to be large and dramatic yet easy to wear.
DF
David Baird
Newton, Massachusetts
David Baird's work is unusual in that he makes traditional hollowware forms, not form sheet, but from wire. This work is a spin-off from his MFA these project at Rochester Institute of Technology, which took architectural structure as its subject. His fascination with suspension bridges led him to make a series of wire constructions, which have now been adapted to production.
His vases and low dishes start with a commercial glass cylinder or dish. He then assembles a composition in wire around the glass. Baird does not precisely reproduce each design, but sets up a system in which he can make endless variations within a given structure. Thus, no two of the metal constructions are exactly the same. Baird's system has the advantage of allowing him a great deal of creative leeway in his production, which presumably keeps boredom at bay. The overall look is constant, as is the size and relative complexity of the design. A wholesale buyer orders a basic size and style; if the buyer doesn't like what Baird sends, he will exchange one piece for another.
The net result is some of the freshest production metalwork in the craft marketplace.
BBM
Jim Kelso
Worcester, Vermont
Kelso is probably the best known as a maker of exquisite, netsuke, knife fittings and sword furniture. He started out studying wooden boat building, and made stringed instruments from 1972 to 1976. In the late 1970s, Kelso was engraving knives. Around 1981 he saw a collection of Japanese sword guards in the Smith College Museum in Northampton, Massachusetts, and was inspired to learn the traditional techniques. For a time he worked for blademaker Louis Mills and later studied with tsuba maker Masichi Sakai in Osaka, Japan. His own metalwork was initially quite derivative of Japanese work, but as he gained confidence his imagery has become more American, reflecting Vermont flora and fauna.
Recently, to gain wider exposure and reach a broader audience, he has begun to make production jewelry. The originals are carved in wax, cast, and molded. The production castings are chased and engraved to recover texture and detail. The intense detail and sense of craftsmanship of the original is maintained, as is the strong reference to traditional Japanese crafts. However, because Kelso employs Western conventions like the brooch or the bracelet, the final result is a hybrid of Japanese and Western.
BBM
Hiroko Pijanowski and Gene Pijanowski
Ann Arbor, Michigan
In her role as a university teacher Hiroko Pijanowski sees that college teaching is no longer a viable career option for most of her students. Instead, should she encourage her students to be artists, or should she show her students how to work as production-oriented jewelers, so their education might be put to good use? Pijanowski chose the latter.
She knew she could not adequately teach her students if she did not have firsthand knowledge of how the contemporary marketplace works, so she decided to make and market her own line of jewelry. This decision is rare among academic metalsmiths: it takes courage to enter an arena in which one might not be competent.
Her collection is based on orchids, and is made in 18k colored gold. The piece seen here can be worn as a brooch, as a pendant on a chain, or as the pearl strands alone.
Furthermore, the various petals used to construct the pendant can also be used to construct different sets of earrings. The experiment is still a work-in-progress, with difficulties in weight and pricing yet to be resolved. As Hiroko says, "The real world is very difficult."
BBM
John Iverson
New York, New York
Each of John Iverson's delicate leaf pins is individually cast from an actual leaf that has been carefully painted from behind with wax. Because no two leaves are identical, each piece is unique. In his selection of leaves which he will use in the casting process and in his gentle manipulation of the leaves in the execution process, Iverson maximizes this uniqueness. Nevertheless, the pins illustrate the production concept of working in a close, integrally connected series of designs.
By using a common image such as the leaf, an artist runs the risk of producing work that is trite. Iverson avoids this pitfall by resisting the temptation to rubber-mold these designs. The relatively small quantity of works that results is jewelry of great subtlety and fine detail that is anything but ordinary.
DF
Biba Schutz
New York, New York
Like many of the jewelers and metalsmiths in this Exhibition in Print, Biba Schutz is self-taught in her craft. About six years ago, she developed a process of wrapping wire over a constructed armature, starting with an anodized aluminum and silver basket (which she admits was awful). Since then Schutz has gradually refined the technique and developed it into a unique production line. She has given up the aluminum, and now works in silver, bronze, copper, and vermeil. These metals have historical associations that aluminum lacks and Schutz says her buyers respond positively to the more pure metal color.
Schutz operates a small shop with several full-time and part-time assistants. Schutz makes all the prototypes and one-of-a-kind pieces, while her assistants build frames, forge, and wrap the production work.
BBM
Reiko Ishiyama
New York, New York
Ishiyama was initially trained as a Japanese art historian, and then worked for ten years in Japan as a sculptor in metal. Frustrated by trying to be a maker of objects in an era that valued conceptual art, she eventually moved to the United States and took up jewelry making. Except for three months of study at F.I.T., she is a self-taught jeweler.
Her current ribbon-like bracelets and earrings grew from her interest in making very light jewelry and from her interest in making very light jewelry and from trying to recycle metal scraps from a series of pierced spirals she was making. The springy, work-hardened forms move as the body moves and the textured surfaces create a soft, natural reflection. The broken surface provides less contrast than a polished surface. The pebbly surface also complements both skin and clothing and thus doesn't dominate the wearer. Although most of her jewelry is sterling silver, these earrings are 18k.
BBM
Ted Muehling
New York, New York
Ted Muehling is best known for his beautiful, subtle jewelry, but lately he has been producing more housewares. The Snail Bowls and candlesticks are typical of his work: so simple as to seem obvious, but nearly impossible to imitate because they are so refined.
Muehling says the spiral shell is the most beautiful shape he knows, and certainly he is not the only designer to be so inspired. He has the bowls cast by a local shop, but he has the castings cleaned up by assistants in his own studio and he tapers the edge and finishes the bowls himself. Muehling takes pleasure in performing some handwork, instead of remaining a strictly hands-off designer. Only by personally controlling the subtleties of form and surface can Muehling achieve the quality he desires. He has tried to shop our more of the labor, but has never been satisfied with the results.
Muehling is a direct descendant of the great Scandinavian-Modern designers of the 1940s and 1950s, such as Tapio Wirkkala and Henning Koppel. Like them, he is inspired by natural forms and like their work, his designs are elegant and understated.
BBM
Petra Class
San Francisco, California
Born and raised in Germany, Petra Class received her extensive formal training as a silversmith before she emigrated to the United States in 1991. The depth of Class's training is evident I both the technical and aesthetic character of her work. Because of her technical expertise, Class is able to fabricate the beads of this necklace from surprisingly thin sheet with the high degree of consistency demanded by her minimalist style. In addition, she is able to integrate the box clasp in an unobtrusive manner which allows the simple but elegant line of the piece to remain unbroken.
In this necklace two sides of each bead are sterling and the third side is a lamination of sterling and 22k. The commercially available laminant provides the rich color of 22k and the rigidity of sterling, is more durable than a plating, and costs only a fraction of solid gold sheet.
DF
Hilary Packard
McHenry, Illinois
The images in Hilary Packard's work range from playful stylized figures to abstract shapes, from poetic text to vegetables and kitchen implements. Packard's current line of jewelry and ornaments had their genesis early in her career with hand-pierced sheet metal forms. This approach was feasible for making five pieces, more difficult for making twenty and impossible for making 100. Thus, as Packard's sales increased, it became apparent that piercing was too time consuming, expensive, and difficult to subcontract in the volume she needed.
After a period of researching various alternatives, Packard decided that commercial photo-etching best suited her production needs and design sensibilities. She now cuts out her entire diverse collection of bold graphic shapes via the photo-etching process. In addition, the efficiency of the etching process permits her to retail most of her work for under $40.
DF
Helen Frady
Chapel Hill, North Carolina
Working alone in her tiny eight-foot square studio, Helen Frady fabricates sensitive abstract and naturalistic brooches and earrings from sterling and 18k. She employs few of the production economies discussed in this publication but has still managed to keep her small line quite affordable. Not fond of shows, Frady has chosen to exhibit annually at only one, the ACE craft fair in Baltimore. She has emphasized wholesale accounts and long-term consignment gallery relationships. Frady feels a small line and consignment relationships encourage flexibility, artistic growth, and personal satisfaction. Thanks to her solid returning accounts and new wholesale orders, Frady was booked for the year by doing this single show.
DF
Peggy Eng
St. Louis, Missouri
Wanting to get away from plain sheet metal, Peg Eng took a workshop from Ann Graham on anodizing aluminum. The color excited her. She already had some experience weaving precious metal, so she later tried the same with aluminum. But trying to anodize weavings would not work well: electricity will not conduct efficiently through the discontinuous structure of a weaving. The answer was to use a single continuous wire. Eng's solution was to wrap aluminum wire around a twisted madrel. In trying to solve a technical problem, Eng arrived at her own distinctive style.
Eng tries to keep most of her prices under $50 retail. She says that prices above that point discourage spontaneous spending, and trying to sell expensive jewelry made of aluminum, with its implication of being a cheap material, is difficult.
She operates a small shop with one part-time employee, so she does much of the labor herself. It is important for her to keep the labor interesting, so she always tried to add at least one new twist design per year and she will eliminate any design that she no longer likes to make. She also enjoys the adventure of working with aluminum, which has a number of odd (and therefore challenging) characteristics.
BBM
Barbara Minor
Baton Rouge, Louisiana
The bead is one of the earliest forms of jewelry. Because of its historic use as a repeated module, it is also one of the oldest objects to be systematically created in multiples. Drawing on much of this rich history, Barbara Minor began making her extensive line of dimensional enamel beads employing a hand process. Initially resisting the expense and effort of mechanizing the construction of the beads, Minor did not begin to use production techniques until she sensed a receptive market for her work and she felt comfortable devoting a significant amount of her time and energy to this particular aesthetic direction.
Together with her technically astute husband Christopher Hentz, Minor has developed hydraulic and pneumatic press tools to generate the deeply formed beads. The beads are strung on a cable designed and manufactured by Hentz which provides the precise degree of controlled rigidity required to present the beads to their best advantage.
DF
Rob Greene
Bristol, Vermont
Rob Greene combines goldsmithing and lapidary techniques to produce both one-of-a-kind and production jewelry. In most of his work, stones are the dominant visual element while gold work provides the settings and linkages.
In these bracelets, Greene employs a technique commonly used by production jewelers - the use of the same basic element in a variety of application. In this particular example, the cast gold setting and fabricated linkage system are used with three different stone variations. Greene also utilizes the same setting, singularity, in earrings and cufflinks.
Greene initially did the stonecutting for these designs himself but now finds it more productive to have the stones cut to his specifications in Idar-Oberstein, the German stonecutting center. This allows him more time for the demanding inlay work of his one-of-a-kind pieces.
DF
Michael Good
Rockport, Maine
Michael Good is well known for his adaptation of anticlastic forming to production jewelry. He has made elegant jewelry for years, and has been widely imitated for years, too. Rumor has it that a German manufacturer can now mechanize the production of Michael Good rip-offs with electroforming.
At any rate, Good continues to develop new variations, which keeps him a couple of steps ahead of his competition. The Spirit Sun Pendant uses one of Bernd Munsteizgfbxner's Spirit Sun® diamonds, a new faceting design which significantly increases the amount of light reflected by the stone. The stone is held in a gold hyperbolic paraboloid extension, in what appears to be a tension setting, but it is actually set in a hidden platinum mount.
Good sees the hyperbolic parabaloid extension as the opposite of a sphere, a kind of illusion or opposite of fixed geometry.
Thus, he sees the form as a metaphor for the awareness that all things are illusionary, an idea that has parallels in both Buddhist mysticism and in subatomic particle physics.
BBM
Sam Shaw
Northeast Harbor, Maine
This ring exemplifies Sam Shaw's credo, "work smarter, not harder." By combining a commercially manufactured hold and diamond ring with a gestural, hand-fabricated 22k liner, Shaw creates a dramatic juxtaposition that accentuates both the commercial and the handmade elements. The 14k and diamond band is employed not only for its visual effect, but also to provide structural support for the softer 22k liner. By using what amounts to an industrial found object, Shaw reduces the time required and level of skill needed to create this piece. Each of the three bench jewelers who currently works for Shaw can produce this ring in about one hour.
Working on the resort community of Northeast Harbor, Maine, Shaw has established a thriving, if seasonal, retail business. His elegant gallery shows both his work and the work of other artists. Wholesaling and retailing his work at several craft fairs during the years helps provide income during the winter months when sales at the gallery are slower.
DF
Martina Windels
Providence, Rhode Island
Martina Windels adheres to the two dominant designs tenets of the twentieth century: form follows function and less is more. Stripped of all ornamentation and relying heavily on repeated elements, Windel's designs are intentionally minimal.
Windels's bracelets demonstrate her strong feel for engineering. Through the use of just the right temper of metal, these continuous folded forms expand to fit over the hand without losing their shape. As a result, Windels eliminates the problem of sizing.
The repetition involved in making the identical elements Windels uses in her fluid necklaces makes outside assistance a necessity for the designer. Windels usually makes use of part-time studio assistant as well as an industrial casting company. Accordingly, during the design phase, Windels is mindful that the technical skill required to construct her necklaces needs to be within the range of her employees. While not every jeweler's work is conductive to hiring outside help, Windels's pieces are carefully designed to allow her to take advantage of the Rhode Island jewelry community.
DF
Robyn Nichols
Kansas City, Missouri
Robyn Nichols had originally hoped to be a botanical illustrator, but that field vanished under the onslaught of photography. Meanwhile, she taught herself silversmithing, first in a high school shop class and then later in art school. Her silverware combines the two disciplines. Her imagery is fairly accurate, the result of careful study. The Mangrove Candlesticks, for instance, stem from her observation of mangrove trees in the Grand Cayman Islands, where she has been teaching seasonally for the past ten years.
There are few silversmiths in the marketplace today. Nichols believes that people have become afraid of silver, perhaps because of the constant polishing required to maintain a bright finish. Even though she puts a high polish on all her work, Nichols talks to her clients about allowing the silverware to tarnish naturally. She occasionally shows some deeply oxidized objects, just to reinforce the idea. She is pleased that most of her work is really used, so her silver becomes a true helpmate in people's domestic lives. Nichols also says that her buyers find silversmithing quite exciting, and she is building a circle of committed collectors. She is confident that silversmithing has better days ahead.
BBM
Bruce MacDonald BRM Design
Burlington, Vermont
Focusing primarily on production, Bruce MacDonald says he "gets a kick out of seeing fifty of the same product laid out on a table." Although he sees himself primarily as a craftsperson interested in good design and hand techniques, MacDonald also takes advantage of subcontracted industrial manufacturing in producing his work.
MacDonald's Helios series initially appear to be constructed of spun components but he has actually utilized a subcontracted stamping process to generate the one-piece, three-quarter spherical, brass forms. MacDonald acquires the round threaded knobs that serve as feet and finials from a screw machine house. The finish, which is also done outside of MacDonald's studio, is a highly durable baked-on industrial powder paint. In total, five different subcontractors are involved in this one series. These varied processes are all tied together with extensive handwork that takes place in MacDonald's studio.
With a vigorous exhibition schedule that includes wholesale and retail craft shows as well as the gift markets, BRM Design has grown to five employees in a matter of six years. In 1996 BRM Design produced and sold over 300 Helios sets.
DF
Karen Pierce
Evergreen, Colorado
When she graduated from Arizona State University in 1993 with an MFA, Karen Pierce thought she "would make a killing selling one-of-a-kind pieces." This was not the case. After her first craft show, Pierce realized she had to develop a less expensive approach to hollowware.
While manufactured spun bowls offered a practical solution, Pierce, who was trained in raising, agonized over using them. "Spinning just didn't feel like metalsmithing," she says. Eventually, however, practicality won out.
The Double Walled Bowls are at the upper end of the line Pierce designed. They are constructed from two copper bowls joined to a pierced rim by low temperature solder. The use of low temperature solder minimizes warpage and prevents the annealing of the work-hardened copper. Now that Pierce has established herself via her production line, galleries have been encouraging her to return to her more expensive raised vessels, a development that very much pleases Pierce.
DF
Linda Hesh
Mt. Ranier, Maryland
Linda Hesh says that her secret agenda is to "…get people to wear something weird." Her work is frequently based on oddball stuff she finds in flea markets, which she then adapts into jewelry designs. She generally chooses old material: cheap throwaways that have been consigned to society's junkheap, but which people also remember fondly from their childhoods. One of her most popular earrings, Double Dutch, started life as a fleamarket find. Hesh then added the jump rope/earwire to complete both the image and the function.
Branch Out also started as found objects: a bead in the shape of a vase and prestrung beads in the shape of branches. The shelf, however, is her own design, carved from wax, cast, and molded.
While the outward emphasis is on fun, Hesh is also concerned about the usefulness and appearance of her jewelry. She makes sure each design complements the face, without being overpowering. Each pin or earring is designed so that it has a punchy, abstract presence from a distance, which then resolves into a clear image when seen up close. The close-up view is also intended to cause conversation, and thus to act as a social lubricant.
BBM
Sarah Flynn
Vail, Colorado
Sarah Flynn says she is inspired by the simplicity and beautiful proportions of classical Greek and Roman architecture, and these rings are the result. Just as in classical architecture, her rings and bracelets are made with sixteen, twenty, and twentyfour flutes. All of her work is carefully fabricated by hand. Flynn scores a sheet of silver and roughs the flutes out with a dapping tool, then constructs a tube. The flutes are further refined on a custom-made stake, the score lines filled with solder, and the construction completed. Flynn also makes bracelets, which are simpler, consisting of a fluted ring without sides. At present, Flynn does all the fabrication herself, and seeks no mechanized efficiencies.
Flynn received her MFA from Rhode Island School of Design in 1996, and is now working for jeweler Jim Cotter in Colorado. This kind of employment/apprenticeship experience is very useful for young jewelers, as it offers an easier transition into the craft market.
BBM
Chris Lowe
Los Angeles, California
These wall-mounted candleholders are some of the most innovative production work this juror saw. Lowe makes them in twelve basic shapes, but each one she produces has different details, textures, and colors. They are formed by chasing and repoussé, a fairly laborious process that is rarely used in production. Once formed, the Nuggets are sandblaster and tinted with patinas and colored pencil.
Lowe is typical of many younger production metalsmiths in that she allows for variations within a system of design and fabrication. This way she can maintain a sense of adventure and discovery while making every piece, instead of mechanically reproducing a fixed design. Having eliminated the most repetitive work, the craftsperson can have a better quality of labor.
The Wall Nuggets are also about Lowe's Abuelita, her grandmother. Each one is stamped with a word or phrase Lowe remembers her Abuelita once said. Like Mexican milagros, the Wall Nuggets are something like a personal prayer and aide-memoir for Lowe, but they also seem to have a much broader appeal as well.
BBM
Shellie Brooks
Cambridge, Massachusetts
This is the first production jewelry the curators have seen that exploits the properties of precious metal clay, or PMC. Brooks worked in ceramics for 12 years and then made jewelry from polymer clay for another five years. She attended a PMC workshop taught by Fred Woell in the summer of 1996 and immediately recognized the possibilities. She says that PMC is much more similar to ceramic clay than traditional polymer materials, and has the virtue of being much more durable. In addition, she uses the high shrinkage rate of PMC (which approaches 50%) to intensify the detail and texture of her modeled forms.
Brooks starts by making a number of objects in PMC, using familiar ceramic techniques like press-molding, hand-building, and tearing things apart. The PMC parts are fired, pieced together (or not), and rubber-molded. The actual production jewelry is cast by a commercial service. She can also use the castings as modules, assembling them in new configurations after they are cast. She has even experimented with inlaying polymer clay into the metal jewelry, for highlights of color.
BBM
Carrie Adell
Santa Fe, New Mexico
The hand is a critical element in both the creation and the wearing of Carrie Adell's touchstones. Rejecting the mechanization of the hydraulic press, Adell prefers the intimacy of hand hammering and dapping each bead individually. The fabric of metals and pattern of every bead is unique due to the variation inherent in the married metal overlay process. Allowing variations in her work not only makes production less exacting and less tedious for Adell, it also offers her customers a unique object - a win/win situation.
Adell mounts her beads on her patented Mount-eze pin system. The same bead can be worn as an earring with a similar system. In both cases, the geometric mechanism provides a visual foil to the organic bead while minimizing visual interference with the bead's presentation.
Because one end of the pin system is threaded, the wearer can replace the bead with another, thus, the wearer is encouraged to purchase multiple beads and to participate actively in the design process. Adell's pin system allows her to retain a measure of control over this collaboration between designer and customer.
DF
Barbara Cieslicki and Virginia Cieslicki Luna
Monkton, Maryland
The Planet pin is one of a large number of designs being produced by Luna, a team of two sisters. The production process is an example of cleverly applying current technologies to the problem of making inexpensive jewelry. Planet, for instance, retails for only $38.
The design starts as a simple line drawing. The drawing is scanned into a computer, and cleaned up in Adobe Streamline®. It is then converted to a format readable by a laser-cutting machine, and gang-cut in opaque white Plexiglas®. The parts are then tumble-finished, colored with special resin dyes created for the toy and medical equipment industries, and assembled. The result is strongly graphic, light, durable, non-toxic, and cheap.
Barbara and Virginia Cieslicki work as a team designing and producing jewelry. While Barbara Cieslicki has been making jewelry for twentyfive years, the two have been producing the plastic jewelry for only the past five years. They insist on designing jewelry that is light and easily wearable, and subordinate to the people wearing it. As Barbara says, "People are not pedestals for jewelry."
BBM
Claire Sanford Top Dog Studio
Gloucester, Massachuesetts
Like many artists, Claire Sanford's one-of-a-kind work feeds her production line artistically while the production line feeds the one-of-a-kind work financially. With the help of one assistant who works exclusively on production items, Sanford is able to spend about ⅔ of her studio time on her unique work.
Both the forms and the patination of Sanford's newest series of production brooches are inspired by the lids of her one-of-a-kind vessels. Her approach to construction is direct, with a minimum of time-consuming fitting and cleanup. Exhibiting production along with aesthetically related one-of-a-kind work allows Sanford to provide her customers with a broad range of prices to choose from without sacrificing impact or quality of presentation.
DF
Thomas Mann
New Orleans, Louisiana
Thomas Mann's career illustrates how the American craft movement has evolved over the last thirty years. Like many artists in the 1960s and '70s Mann became a craftsperson not because he saw it as a lucrative business opportunity but because he was interested in a counter-culture lifestyle that emphasized simplicity, pleasure in one's work, and egalitarianism.
It was Mann's egalitarian philosophy that lead him to make nonprecious collage and assemblage-based work that everyone could afford. Although this decision was aesthetically and politically motivated, it turned out to be a path towards success in the market as well.
Mann's jewelry business currently employs between twelve and eighteen full-time assistants. In addition, Mann owns two galleries in New Orleans which show his work and the work of other artists. He also sells to approximately 200 stores and galleries throughout the United States and abroad. In 1996 Mann's operation produced and sold about 20,000 objects.
Initially establishing his wholesale clientele through the American Craft Enterprises (ACE) craft shows, Mann rode the crest of the growing wave that was the postwar American craft movement. Like that movement, Mann began with modest ambitions that have lead him into a complex and demanding business he never would have imagined in his early days.
DF
Judy Vilmain and David Klinger Vilmain & Klinger
Providence, Rhode Island
When Vilmain and Klinger formed their partnership three years ago, their goal was to provide good design at very affordable prices. Their aluminum box and stainless steel salt and pepper shakers successfully meet the challenge they set for themselves.
In designing the box Vilmain and Klinger sought a mechanized system of simple joinery that would not require complicated machining. Their clever solution was to use a table saw to cut grooves and slots into the aluminum, allowing the sides of the three-inch cube simply to slide together. Multiple sheets of metal are stacked on end and run through the sawblade simultaneously. Vilmain and Klinger match the thickness of the circular sawblade to the thickness of the metal, thereby ensuring a perfect fit for the slots. As an additional production economy, Vilmain and Klinger purchase three-inch wide aluminum stock which must be cut only to length, not width, thus further minimizing wasted time and material.
Exhibiting in the gift markets, Vilmain and Klinger have come to realize the importance of packaging. Their box is presented in a cardboard container with the product name, Aluminum 13, on the outside. Inside is a paper cube on which scientific information and assembly schematics are printed. The slender shakers are packaged in a graphically bold black and white box, the colors taken from the colors of pepper and salt.
DF
Jeanne Atkin and Herbert Atkin
Haverstraw, New York
In this affordable piece, the father and daughter team of Herbert and Jeanne Atkin bring a contemporary twist to traditional Judaica. Not only does this piece work as a menorah at Chanukah, its individual elements which move independently can function as candle sticks throughout the rest of the year. In addition, the various components are designed to fit snugly against each other in a small square box, making its packaging both economical and attractive for sales purposes.
The Atkins developed the models for the design in brass using a milling machine. The models were then molded and cast in pewter by an industrial casting company. Like many production artists, the Atkins find using subcontractors for some production processes vital to their business.
DF
Shiang-Shin Yeh
San Diego, California
The Platonic Brooch series by Shiang-Shin Yeh is an interesting hybrid between the high-tech and the handmade. Yeh, who has an undergraduate degree in mechanical engineering, is trained in both computer-aided design (CAD) and numerically-controlled (CNC) machining. So, he is quite aware of the limitations of both handwork and computer technologies.
Pieces such as the Brooch PLAT 5C #2 CL are designed in AutoCAD®, a popular CAD program. The precise tolerances of the various cuts and profiles are worked out on the computer screen, as are the subtle differences between parts. But instead of fabricating the brooches with laser-cutting or CNC, he cuts out the aluminum parts on a bandsaw, and shapes the leading edges on a disc sander. It takes Yeh only two or three hours to make each brooch by hand. He points out that, for his purposes, the setup costs of many high-tech fabrication systems remain prohibitive, and at the same time, many operations can be easily done by hand with simple equipment. By insisting on using the most effective fabrication process - in this case, handwork - Yeh critiques those enthusiasts of computer technologies who are content only with computer-generated virtuals.
BBM
Boo Poulin
Rochester, New York
While studying to receive her MFA from Rochester Institute of Technology, Boo Poulin was encouraged to explore a broad range of traditional and nontraditional materials. Since graduating in the early 1980s, Poulin's palette has included aluminum, rubber, plastic, steel, and sterling. Stylistically her work has remained quite minimal and formal. It is often graphic and always pared down to the bare essentials.
In designing this bracelet, Poulin wanted the lines to remain unbroken by a clasp. She accomplished this by stringing the cast sterling elements on two lengths of strong elastic. As a result, the bracelet expands to slide over the hand and then resumes its original form to sit comfortably on the wrist. Two difficult elements in the production of bracelets - clasp design and sizing - are thus eliminated.
DF
Carol Webb
Santa Cruz, California
Through an innovative combination of techniques, Carol Webb has developed a production approach that delivers the graphic quality of married metal and inlay but does not require laborious fitting and soldering. Webb begins with a laminate composed of a thin layer of copper fused over fine silver sheet. Webb initially produced this material in her studio but now has it manufactured to her specifications. Patterns are photocopied onto acetate with a copying machine. The toner from the acetate is then transferred to the bi-metal which is etched in ferric chloride. The chemical attacks the exposed copper but not the silver, revealing a two-color graphic pattern. This process permits a degree of detail and complexity that would be nearly impossible to achieve by means of normal married metal techniques.
Determined to add impact to her bold patterns, Webb utilizes a hydraulic press as well as fold forming techniques to produce three- dimensional forms. She integrates the forms with the graphic patterns in a manner that accentuates and complements both. The efficiency of her processes allows her to sell what appears to be quite elaborate work for a surprisingly reasonable price.
DF
Lilly Fitzgerald
Spencer, Massachusetts
While touring shops in Paris, Lily Fitzgerald happened upon a piece of late 17th century French jewelry incorporating butterfly wings. Fascinated by the piece's delicate beauty and vibrant color, Fitzgerald decided to use this unique material in her own work. Her initial fears concerning the wings' fragility were allayed after Fitzgerald made a test brooch which she wore daily for four years. The brooch withstood the test of time and she has been making butterfly wing brooches and pendants ever since.
Fitzgerald acquires the broken wings of endangered species from a store in New York. She sandwiches the wings between a watch crystal and a sheet of gold. These three layers are then set from behind in a cast 22k frame.
Fitzgerald does not wholesale any of her work through galleries, but focuses her marketing efforts entirely on direct sales to retail customers and she has built a loyal following of clients. This approach gives her the freedom to indulge her creativity in a wide variety of gold work. Her butterfly wings series falls somewhere between her complex, fabricated, one-of-a-kind pieces and her simpler, classical production earrings. Fitzgerald believes that maintaining a range of prices and styles has been important to the growth of her business.
DF
Dennis Arsenis
Walnut Creek, California
Dennis Arsenis used to be a banker on Wall Street, but he liked neither the work nor the political infighting. He took up jewelry almost by accident, and learned most of his craft in trade shops. As he says, the process "took a lot of years doing things I didn't like." Now, he sees small studio production as vitally important to his quality of life.
Arsenis produces a line of gold jewelry, most of which is granulated. Much of it is conservative design that recalls Greek and Roman jewelry, similar to most granulated work in the marketplace. Arsenis admits this work sells well: people seem to be more comfortable with the classic look, and usually avoid more experimental work. One such experiment is this cast and enameled pendant. The enameled pattern has the illusion of being made of colored stones, and plays off against the secondary pattern of gold granules. Both curators were impressed with this design.
BBM
Cheiko Akagi
New York, New York
These earrings are but one version of several Peel variations. Originally inspired by a twist of lemon in a martini, Akagi carved the original model in wax. Once the mold was made, Akagi could add set stones or drop pearls to the commercial castings. She is very interested in creating a soft look, which Akagi sees as a metaphor for the feminine. Consequently, there are no hard edges in her jewelry.
Akagi came to New York in the late 1970s to "absorb the new." She took several jewelry courses at the Fashion Institute of Technology, feeling that American jewelry was more sophisticated and technically advanced than Japanese jewelry at the time. However, a strong sense of the East still permeates Akagi's designs. For instance, she chooses her stones through her own sense of Ki, a Chinese concept related to Feng-Shui. Presumably, the Biwa pearls in these earrings were chosen this way.
BBM
Dennis Nahabetian
Kent, Ohio
Dennis Nahabetian received his MFA in metalsmithing from Southern Illinois University in 1996. In addition to his interest in the visual arts, Nahabetian is an accomplished musician whose credits include a position as co-principal bass with the Detroit Civic Symphony Orchestra.
Nahabetian's jewelry combines his affinity for both art and music. His brooches explore the visual language of rhythm and musical notation. His Finale Chord brooch depicts a large resounding chord while Harmonic Resonance has an overlapping wave pattern derived from an oscilloscope.
These brooches are initially formed in fine bronze mesh by careful manipulation of a grid pattern. The established patterns are then thickened and secured in place through several courses of electroforming. The transparency of the pieces allows for an interaction between the brooches and the fabrics to which they are pinned.
DF
Carly Wright
Altamont, New York
There are few production enamelists these days. This is quite a contrast to the late 1950s, the heyday of the Trinkit kiln, when the marketplace was flooded with mediocre enamel jewelry.
Carly Wright has learned, through long experience, that you can break some of the rules. All her production jewelry is enameled on castings. She enamels on sterling silver instead of fine silver, which makes the jewelry much more durable. Furthermore, she no longer uses counter-enamel. Doing either of these things was supposed to cause your enamel to chip, but she has had very few returns for this reason. She also uses lead-bearing enamels, but she's very careful to use safe practices when firing or grinding her pieces. Her designs are inspired by rock forms and glacial fissures, which she sketches near her home in upstate New York.
BBM
Valerie Hector
Chicago, Illinois
Beaded artifacts have been found in archeological sites dating back thousands of years. Valerie Hector studies and makes extensive use of this rich and varied history in her elaborate vibrant beaded necklaces and earrings. In fact, many of the European glass beads she uses are themselves rare antiques.
Hector begins each piece with a painted wooden armature which is then laboriously wrapped with tiny beads that have been strung or woven in various ancient patterns. Some beads are so small that they must be strung using an eight inch needle that is as fine as a human hair. Because the supply of these antique glass beads is limited and the work involved in making them so labor intensive, Hector would be unable to pay her employees adequately were she to wholesale them at anything but prohibitive prices. Accordingly, she has made the business decision to sell her work only at retail prices. To reach her audience, Hector exhibits at ten to twelve retail craft shows annually.
DF
Peter Handler
Philadelphia, Pennsylvania
The Calamari Chair is another example of an object made with both hand and computer-aided technologies. Handler first develops the forms of the legs, seat, and back support in Form-Z®, a solid modeling program. Switching to drafting mode, Handler prints out measured drawings, which he takes to his modelmaker. The modelmaker then makes life-size patterns in wood or resin. Because the initial drawing is done in the 2-D space of the computer screen, Handler must make some adjustments at this stage to account for the three dimensionality of the patterns. The aluminum parts are then sand-cast at a local foundry. Handler drills, grinds, and welds the cast parts in his own studio before having the metal powder-coated and the seat upholstered.
Handler is making inroads into the hospitality furniture field, which serves businesses like hotels, restaurants, and time-share condominiums. For instance, he is bidding for an order of 300 Calamari chairs. The scale of such production means that Handler must search for every possible economy, including the possibility of having some parts fabricated by a computer numerically-controlled router.
BBM
Charles Crowley
Gloucester, Massachusetts
These two cocoa pots are two of a set of five portraits of Charles Crowley's family: Crowley himself; his wife Clair Sanford; his two children; and their dog. The finials represent each character. Here, the star is Crowley's son, and the dog is, of course, the dog.
The truncated cone is a traditional cocoa pot shape, as well as the form of the familiar Italian oil can. But the cone is also related to the demonstration that Crowley does for his hollowware workshops, where he shows how to make a seamed and tapered form. The finials are carved from solid metal. (Crowley finds carving faster and more direct than casting.) The handles are bent up from solid pieces of tapered aluminum, given a filed finish, and waxed. Since Crowley prefers the subtle warmth of the metal's color he does not anodize the handles. The spout is partially formed and decked with a bent sheet. These pots show how silver hollowware can be made simply and efficiently and still have a lot of character.
BBM
Robin Quigley
Providence, Rhode Island
Robin Quigley teaches full-time, so she doesn't have to make production jewelry to pay the bills. Every five years or so, however, she designs and produces a production line. Wheel and Leg is an example from her latest effort, her fifth line since 1975.
When she makes unique objects, Quigley will invest quite a bit of time and effort on each piece. The result is that the one-of-a-kind work is expensive, and there aren't very many of them. Thus, her production work is intended to generate work that is easier to make, much more affordable, and more widely distributed. In fact, Quigley sees each production line as a unified work. She carefully works out each design so that it is light, so that findings are integrated into the design in unexpected ways, and so she can make a number of variations from each part. For instance, the parts of Wheel and Leg are also made into earrings.
BBM
Brian Hagiwara and Bret Baughman Doghaus
New York, New York
Dohhaus was created by two photographers who had become frustrated by the lack of good housewares they could buy, so they started their own business, beginning with lamps. Their specialty is a modern play on classical forms and using two dimensions to interpret three-dimensional shapes. Since neither partner has experience in hand fabrication, all their work is fabricated in a variety of materials by industrial contractors.
The Baroque Candelabra started its life as a model made of foamcore and cardboard. The final profile was designed in a CAD program on a Mac. The file was then reformatted for PC, and sent to a shop where it was laser-cut from cold rolled steel. Laser-cutting has the virtue of having very low setup costs, so experiments and short runs can be made inexpensively. The profiles were then finished with an electrostatic powder coating. By taking full advantage of new technologies, Doghaus can retail this candelabra for only $65.
BBM
Steven Ford and David Forlano City Zen Cane
Philadelphia, Pennsylvania
Of all the work being done in polymer clay, some of the most interesting is by the two partners of City Zen Cane. Their earlier designs were inspired by the glass technique of caning (sometimes called murini), in which threads of color are gathered into a single stick, sliced into wafers, and reassembled. More recent designs like the Coral Necklace exploit polymer clay's ability to pick up graphic images. Original drawings are transferred onto a sheet of clay, which is then baked and punched into circles, which are in turn inlaid into unbaked beads. The complexity of the process results in surprisingly original jewelry design, which can be replicated in many variations.
City Zen Cane is a collaboration of two different sensibilities. Typically, David Forlano will mix colors and arrange a palette, Steven Ford will fabricate the first stage of the canes, Forlano will gather several canes together, and Ford will cut them and make the final assembly. While each partner specializes, one will occasionally work in the other's role, and much of their innovation comes from trading jobs back and forth.
BBM
Mary Kanda
Gloucester, Massachusetts
At different times, Mary Kanda has worked in ceramics, etching glass, glassblowing, torch-firing enamels, lapidary, glass mosaic, and production jewelry. This varied background represents more than twenty years of searching for the medium that suited her best. Five or six years ago, she first combined glass mosaic with metal jewelry. In true mosaic, each chip must be laboriously cut and fitted in place, so as a substitute, she decided to place glass seed beads cemented with colored tile grout in silver frames. The result is something like the traditional micro-mosaic. Her innovation is unique in the production marketplace, allowing her to make colorful earrings, brooches, and bracelets.
While the metal backs for earrings are cast, most other frames are fabricated of sheet and wire. Each bead must be placed in the frame by hand. Kanda presently employs three people part-time to help with different aspects of the production, but she does not seek any further mechanization of the process. Because she likes her labor - probably because it's a complex, multidisciplinary process - Kanda seeks no improvements. Like many production jewelers, she sees handwork as necessary to a good quality of life.
BBM
Peter Diepenbrock TROY
Providence, Rhode Island
After graduating from Rhode Island School of Design in 1984 with a degree in industrial design, Peter Diepenbrock spent several years primarily producing large objects such as abstract sculpture and, later, limited edition furniture. In 1993, however, a surprisingly strong response to a bronze bottle opener that Diepenbrock cast in a whimsical dinosaur-like form caused him to start his company TROY. Diepenbrock describes TROY as a "creative development studio devoted to the manufacture of high quality table top products." He now makes sculpture under the business name.
In producing objects for TROY Diepenbrock utilizes an exceptionally broad range of subcontracted industrial manufacturing processes. For example, his fanciful picture frames are made from resin cast by one company them, after the raw plastic castings are cleaned up in Diepenbrock's studio they are electroformed in silver by another industrial company. His aluminum centerpiece candle holder and Saladmanders salad servers are foundry sand cast by still another company which also polishes them. Having this work done out of house reduces the investment in equipment while maximizing Diepenbrock's design range and freedom.
DF
Wendy Stevens Alloy Design
Boyertown, Pennsylvania
In the early 1980s Wendy Stevens was living on the periphery of New York City's art and fashion worlds. Tending bar at night, studying dance in the morning, Stevens experimented with designs for metal handbags and belts in the afternoon. The tools in her small apartment's work space consisted of a pop riveter, tin snips, a file, and a soldering iron she bought for a dollar.
With no formal training in metals, but with a great deal of tenacity and passion, Stevens has produced a sophisticated, well-crafted line of handbags, picture frames, lighting, barrettes, and home and office accessories. Starting tentatively and gradually building technical resources and markets, she has accomplished something quite unusual - a product line embraced by four primary markets.
It was Steven's early, fruitful relationships with sales representatives that helped her enter three of those markets - the fashion market, design and gift shows, and museum store shows. Later, encouraged by metal furniture maker Will Stone who would become her husband and business partner, Stevens was also well-received at the leading retail and wholesale craft shows. By intentionally avoiding jewelry and instead following a much less travelled route, Stevens has distinguished herself from the crowd.
Several years ago, a pregnant Stevens became concerned about the toxicity of soldering fumes. She began producing work using only cold connections. Because her cold connected designs were more cost effective, they turned out to be better for both her health and her business. In Steven's case it can truly be said that motherhood is the mother of invention.
DF
Kim Rawdin
Scottsdale, Arizona
While teaching in the public school system in Chinle, Arizona, Kim Rawdin started working with Navajo jeweler Gene Jackson. From Jackson, Rawdin learned the technique for making shadow-box bracelets, in which stones project through the upper surface of a hollow bracelet. Traditionally, such bracelets are usually symmetrical; and are set only with the stones typically used by Navajo jewelers. Rawdin stretches the formula a bit by placing the stones asymmetrically, and by using a wide range of colors and shapes. For some bracelets, he replaces the stones with irregular silver forms, making an exuberant biomorphic bracelet.
In another personal touch, Rawdin composes a short Haiku verse for every design, and stamps it inside each bracelet.
BBM
Joan Parcher
Providence, Rhode Island
Joan Parcher has designed some of the most restrained, and most innovative production jewelry of the past decade. Her Mica necklace and Ball and Hoop necklace are particularly memorable. These Mica earrings are typical of her recent work. Mica works well with Parcher's taste for functional simplicity. Mica can't be forced into baroque extravaganzas of form, but does seem to be perfectly suited for simple geometric shapes.
Parcher made her first mica jewelry some years ago, never figuring it would become a suitable material for production jewelry. However, the material is very light, making large forms possible. It also sparkles, and it has a seductive iridescent quality, too. Here, Parcher uses the translucence of mica to build up the color density, as if the material was washed of watercolor.
BBM
Abrasha
San Francisco, California
Before he moved to the United States in 1977, the Dutch-born jeweler Abrasha received his formal training in the German jewelry center of Pforzheim. This training is evident in these skillfully crafted pendants. Originally hand-ground from two mild steel hardware store washers, the two stainless steel halves that form the pendants are not cut and tapered on a lathe by a machinist. This is the only major timesaving step in making the pendants, however. Despite the fact that the 24k gold rivets and most of the other details are cold connected, the degree of precision demanded by Abrasha's aesthetic and training makes these pieces quite time consuming. It takes Abrasha four to six hours to assemble the seventeen components of the largest pendant.
Abrasha currently markets his own through various wholesale and retail venues including consignment galleries and craft shows. He also receives a substantial amount of local commission work.
DF
Cathleen Bunt
Kihei, Maui, Hawaii
When Cathleen Bunt graduated with a BFA from New York State University at New Paltz in 1979 she knew she wanted to make a living at her work but she wasn't sure how to go about it. "Coming out of school you don't have a clue what to do," Bunt says.
Fortunately, Bunt got a job in New York City working for production jeweler Larry Seegers. This experience not only improved her bench skills but also introduced her to the craft show circuit and exposed her to Seeger's marketing skills and business acumen. With Seeger's encouragement, Bunt eventually exhibited at her first craft show. She remained in Seeger's employ for another year until her business could stand on its own.
In the years since, Bunt's work has evolved in a manner often seen in the world of production jewelry. She began her career working in sterling combined with aluminum and other nonprecious materials, but as her skills and confidence grew she moved to gold and gems. When her work consists of precious materials, Bunt finds the public more willing to compensate her adequately for the substantial amount of time and care she expends in making her complex and technically challenging jewelry.
DF
Whitney Boin
New York, New York
The diamond engagement ring is one of the most traditional and emotionally charged forms of jewelry. Couples who normally would not give precious jewelry a second look often spend a great deal of time and money on their engagement rings. The societal expectations and associations for these rings plus the classical simplicity of the engagement ring format make coming up with a truly new engagement ring one of the most difficult design challenges in the precious jewelry world.
Whitney Boin's Post Engagement Ring is his award-winning response to this challenge. Always an innovator, the prolific Boin has won more design awards than any other jeweler of his generation. Marketing his work primarily through JCK's Las Vegas show, Boin has substantially trimmed his line to focus on his Post Ring design and on variations on this one, signature concept. Because the wholesale fine jewelry market is relatively conservative, Boin has to constantly try to find the most successful balancing point between the market's need for consistency and his own need for innovation.
DF
Stephen Dixon
Corbett, Oregon
The largest components of the retail fine jewelry market are rings and earrings. As his business has grown, rings have become Stephen Dixon's primary focus. Dixon maintains, "there is a different psychology in the sale of rings, a built-in market with less price resistance. It doesn't matter if we're in The Gulf War or whatever - people still get married."
Many of Dixon's design choices come from his desire to maximize the color contrast of 14k yellow and white gold. The sandblasted finish as well as the slight beveling between the layers of gold are important in achieving this contrast. Initially, Dixon found the public reluctant to accept a matte finish but over time his audience has become far more receptive.
In this series of rings, Dixon does much of the initial wax work on a lathe and then costs the waxes in three parts. Unlike most production jewelers, Dixon prefers the control and expediency of in-house molding and casting.
DF
Joseph Pozycinski and Georgia Pozycinski Pozycinski Studios
Sparta, Missouri
Joseph and Georgia Pozycinski specialize in decorative cast bronze vessels. Joseph had trained as an electrical engineer but had taken up wood-turning; Georgia's degree was in zoology, but she worked as a potter. Around 1992, they started collaborating on bronze vessels, which meant they had to teach themselves all the required techniques. Joseph set up their sand-casting foundry. He is responsible for the designs of vessels and bases, for making patterns, and for pouring the large castings. His woodworking experience serves him well when he makes the patterns. Georgia, with her background in zoology, designs and models the animals that serve as the focus of each piece, and specializes in patination. She points out that patination resembles raku firing, in that both processes use heated metal oxides to develop colors.
Because of the difficulty of casting and coloring bronze, the work of Pozycinski Studios is hard to imitate. Nonetheless, their designs are copyrighted and registered, and they constantly introduce new designs into their line. Their work, in its plain geometry and in the decorative flourish of the animal imagery, call to mind some of the lacquered metal vases of the French Art Deco designer, Jean Dunand.
BBM
You assume all responsibility and risk for the use of the safety resources available on or through this web page. The International Gem Society LLC does not assume any liability for the materials, information and opinions provided on, or available through, this web page. No advice or information provided by this website shall create any warranty. Reliance on such advice, information or the content of this web page is solely at your own risk, including without limitation any safety guidelines, resources or precautions, or any other information related to safety that may be available on or through this web page. The International Gem Society LLC disclaims any liability for injury, death or damages resulting from the use thereof.
Related Articles
Ornamentum Gallery: A Jewel in Constant Transition
35 Years of Electrum Gallery
Metalsmith ’83 Fall: Exhibition Reviews
Samuel Yellin, Metalworker
The All-In-One Jewelry Making Solution At Your Fingertips
When you join the Ganoksin community, you get the tools you need to take your work to the next level.
Trusted Jewelry Making Information & Techniques
Sign up to receive the latest articles, techniques, and inspirations with our free newsletter.