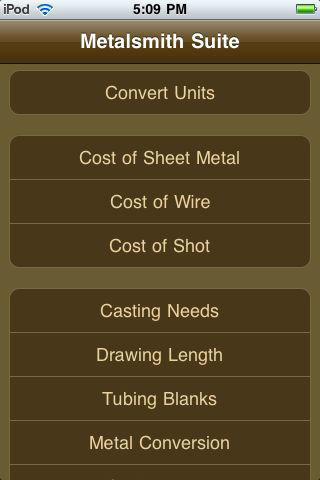
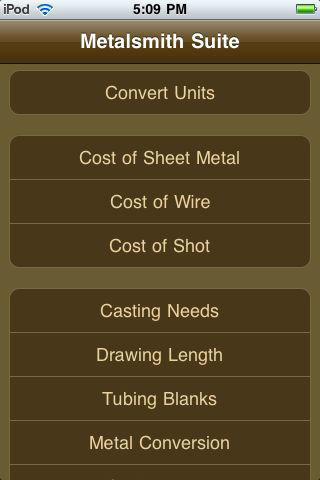
Metalsmith Suite iPhone App Test
7 Minute Read
The jewelry industry today is not what it was 15 or 20 years ago. From CAD/CAM to inventory control software, computers have changed the way we design and manufacture jewelry. The main benefits these and other new technologies offer is the ability to streamline our processes and improve quality. And since we all know time is money, working faster means being more profitable.
With smartphones, we can now have computers at our fingertips at all times. I recently had the opportunity to test a new application for the iPhone just for jewelry makers: Metalsmith Suite, which was developed by Tim McCreight of Brynmorgen Press.
Because there is a lot of math involved in being a jeweler, you need a calculator at hand and a good bit of reference material either memorized of stashed away in your shop. This app contains most of these necessities in one convenient place—and you can tote them around in your pocket for quick access.
Content Evaluation
The app's home page features an easy-to-use list of functions with good-size buttons for easy navigation. These are numerous calculation and information buttons, as well as an instructions button that explains the functions and gives directions. Here is a summary of how each works:
Unit conversion. This function is split up into four types of units: length, weight, volume, and temperature. Featuring a click-wheel design for easy navigation and selection of units, it allows you to quickly and easily convert inches to millimeters, Celsius to Fahrenheit, and so on.
Metal cost calculator. There are three buttons that allow you to calculate the cost of metals in three different forms: sheet, wire, and grain. Using the click-wheel, you choose how much you need of a particular alloy, and the app retrieves the daily spot price from the Kitco website. You then type in the daily spot price for a specific metal into a new window display, and the app calculates the cost of what's needed. This might be a little easier to use if the app had a button to automatically input the spot prices in these windows for you; however, it is still much faster and easier than my previous method of metal cost calculation, which involved going online to find the day's spot price and using several different calculations (and a little guesswork) to arrive at a price for each different form of metal.
Casting. There are two buttons that deal directly with casting calculations. With the "casting needs" button, you enter the weight of a wax model in grams or pennyweights, and the app calculates how much metal the object will require in any of seven metals or alloys. The "gold alloying" button helps with the conversion of gold alloys. For example, if you have some casting grain that is 14k and you want it to be 18k, the app calculates how much pure gold you need to add to the mix. Considering that I check my figures three times when I do this with a calculator, this is one of my favorite features.
Fabrication. There are two buttons primarily used for fabrication. The "drawing length" button tells you the length a wire will stretch to when drawn to a specific gauge. It enables a jeweler to figure an approximate length needed when ordering wire. The "tubing blanks" button is used for calculating the width of metal needed to fabricate a tube, taking into consideration the thickness and either the inside diameter or the outside diameter. Both of these buttons help reduce overspending on precious metals by doing the math for you. Considering how much money and time they can save the jeweler, I think these two tools are fantastic.
Metal conversion. Especially useful when pricing or putting together a quote, the "metal conversion" button calculates the weight of a piece by converting its weight in one alloy to its weight in another. For example, you can input the weight of a ring in sterling and find out what it would weigh in 18k. You can then take that weight and figure out how much the casting grain would cost to make the 18k ring.
Equivalent numbers. A great tool for comparing different number systems, the "equivalent numbers" button is a must-have quick reference for anyone working at the bench. It allows you to easily calculate such specifics as the drill bit size needed for a certain gauge of wire.
Metal properties. This button lists each jewelry metal's melting temperature in Celsius and Fahrenheit, as well as its specific gravity.
Gem properties. Providing very basic information about 50 different gemstones commonly used in jewelry, this button offers a pronunciation guide, hardness figures, heat sensitivity, and some background information. In addition to helping bench jewelers figure out if they can use a torch near a stone or not, this button can be a helpful sales tool when working with customers.
When it comes to technologies that enable us to speed production and make more money, the Metalsmith Suite iPhone App is a home run. It's a convenient tool that you can tote around to quickly access the calculations and information you need daily as a jeweler. Priced at $3.99, it's more than worth it. I found myself using the app a lot while I was testing it, and I continue to use it now that I've completed the review. For the tech-savvy modern metalsmith, it's a must-have.
Because the saw handles are of a slightly larger diameter than most, they allow for a comfortable position for your hand and reduce stress. The larger size appears to be possible because of the weight savings in the metal parts of the saw frame.
Performance
As I began to work with the saw frames, I knew I would have to unlearn some of my old habits in order to get the most out of the new saw design. The biggest issue I came across was with the blade installation and tensioning. The holes in the frames for inserting the blade are quite small. To enable easier insertion of the blade, I opened up the ends of the holes slightly with a bud bur to create a small taper. (It's important to do this with the saw upside down so that no debris falls into the bottom of the hole and impedes blade insertion.)
Also, the tightening nuts are less substantial than the ones I'm used to manipulating. With some practice, I got comfortable with them, and I realized that I did not have to tighten them as much as those on my old saw to secure the blade properly. Initially, I was actually breaking off blades at the friction points because I was over-tightening.
Tensioning also took a little getting used to. To tension the blade on the aluminum frames, you twist a nut on the top arm of the frame. It's easy to do and, with time, the amount of twist needed should become familiar. The nice thing about this is the ability to personalize how tight your blade is, since every bench jeweler likes his or her blade tightened to slightly different extents.
The titanium frame uses a more sophisticated cam system for tensioning. The cam is a lever that is attached to the top of the frame. Once you insert and tighten the blade, you pivot the lever from the open position to the closed position, tensioning the blade the exact same amount every time. This feature should be a great benefit to both the experienced jeweler and the novice who hasn't yet figured out the subtlety of blade tensioning.
Although installation and tensioning took a little getting used it, it didn't take long for me to fall in love with the real benefit of these saw frames—the stiffness of the spine and the resulting control and finesse it provides to cutting operations.
The saw frames gave me greater control of the saw for both straight and curved cuts, but they really shined in the tight cutback corners present in most pierced designs. My straight cuts did not weave from side to side as they can when using traditional-style saws. Also, the blade tracked well along the arc on curved cuts, staying closer to my guidelines.
That said, the stiffer frame does require you to use a lighter touch most of the time. When you catch a tooth of the saw blade and it hangs up momentarily, the lack of flex in the frame is less forgiving, which may cause you to break a few more blades when you're powering through metal and hit a snag. Another major benefit of this tool is the lightness of the saw frame, which allows for long periods of piercing without excessive fatigue or reduction in quality.
After a few weeks of working with these new saws, I quickly adjusted to them—and I'm not getting better results than I was with my faithful old saw. This is definitely my new favorite saw frame.
Mark Maxwell is owner of Mark Maxwell Designer/Goldsmith, mmgoldsmith.com.
Supplier's Note: In response to this product testing and user feedback, Knew Concepts is making a change to out machining process to add a small tapered entrance to the blade hole.
The award-winning Journal is published monthly by MJSA, the trade association for professional jewelry makers, designers, and related suppliers. It offers design ideas, fabrication and production techniques, bench tips, business and marketing insights, and trend and technology updates—the information crucial for business success. “More than other publications, MJSA Journal is oriented toward people like me: those trying to earn a living by designing and making jewelry,” says Jim Binnion of James Binnion Metal Arts.
Click here to read our latest articles
Click here to get a FREE four-month trial subscription.
You assume all responsibility and risk for the use of the safety resources available on or through this web page. The International Gem Society LLC does not assume any liability for the materials, information and opinions provided on, or available through, this web page. No advice or information provided by this website shall create any warranty. Reliance on such advice, information or the content of this web page is solely at your own risk, including without limitation any safety guidelines, resources or precautions, or any other information related to safety that may be available on or through this web page. The International Gem Society LLC disclaims any liability for injury, death or damages resulting from the use thereof.
Related Articles
The Enamelware of Bev Yokley
Structuring for Efficiency in the Studio
Getting to know Mark Loren
Full eBook: Practical Jewelry Rendering
The All-In-One Jewelry Making Solution At Your Fingertips
When you join the Ganoksin community, you get the tools you need to take your work to the next level.
Trusted Jewelry Making Information & Techniques
Sign up to receive the latest articles, techniques, and inspirations with our free newsletter.