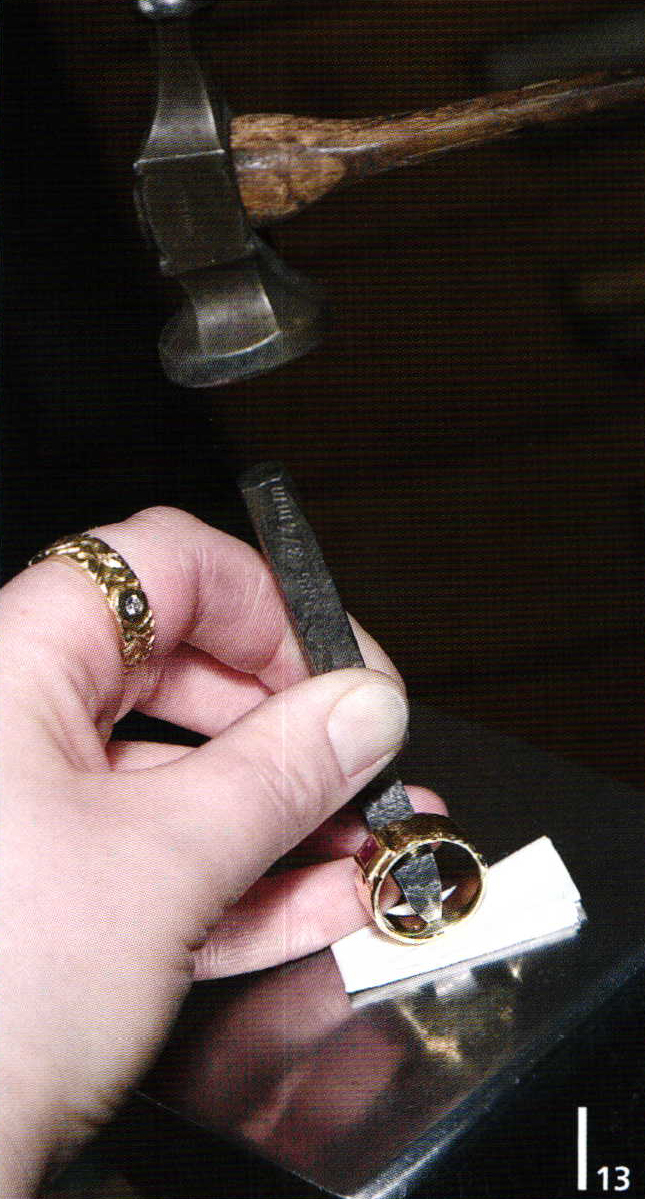
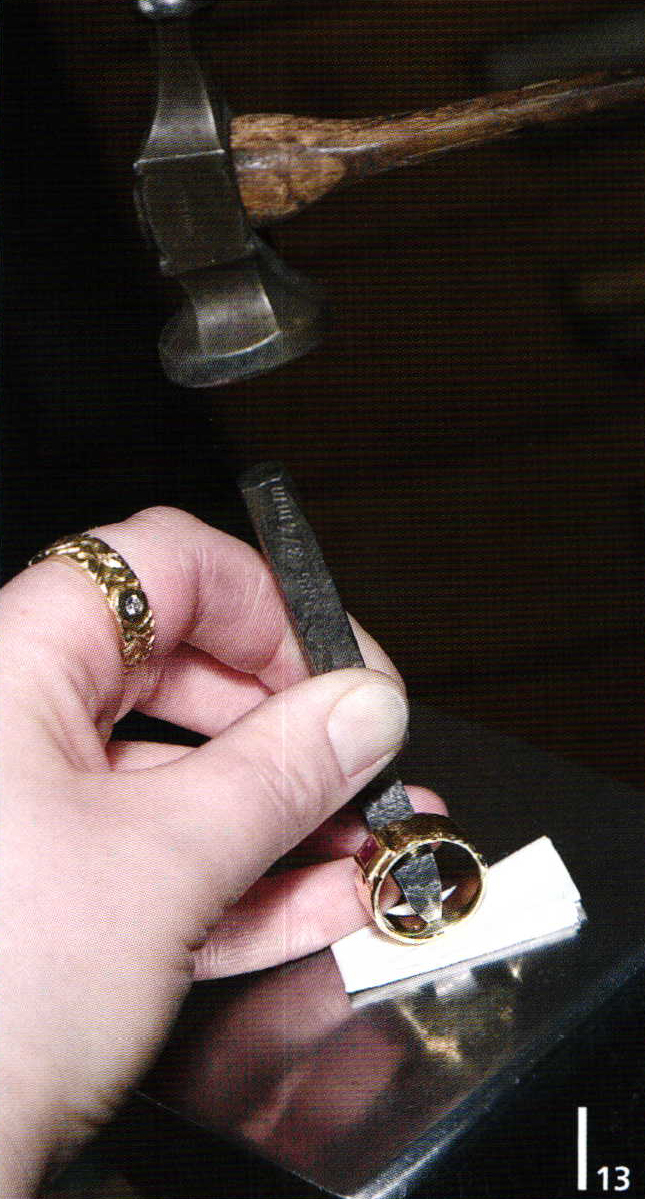
Precious Metal Alloys Part 1
7 Minute Read
In the Middle Ages, alchemy meant the art of fathoming natural substances in an experimental manner. The goal of the alchemists in this was to alter and refine matter. The process of melting and alloying precious alloys is similarly fascinating. Although today experience and natural sciences knowledge leads to good results without experimentation.
Katrin Erben, goldsmith from Braunschweig, Germany explains why she is alloying gold. "The ability to alloy small quantities of gold alloys myself or to melt remnants to a new sheet or wire grants a degree of independence. Omitted forming costs and shipping costs incurred mean that alloying myself is an interesting proposition. The consequence is that there is no dead capital laying in the safe in the form of wire and sheet of unfrequent used alloys."
Alloys with master alloys, granules or old gold
Whether or not this is worthwhile from an economic viewpoint must be decided on a case-by-case basis. The separating works offer a broad range of colors and shapes of metal alloys, in many cases deliverable in 24 hours. Precious metals suppliers offer granules of precious metals, copper pivots and master alloys are often added to precious metal alloys. Master alloys are built of additives such as zinc or nickel. Depending on its intended purpose, a master alloy has its own composition for certain alloy properties such as hardness, elasticity or ductility. A master alloy can have a number of possible compositions depending on the requirements for casting, soldering, etc. It is not advisable to alloy with zinc in its pure form for example because it evaporates easily. Alloys melted with a number of different master alloys may not be mixed together; otherwise the properties of the alloys may cancel each other out in some circumstances. It is important to use chemically clean copper when alloying precious metals. When old gold is melted down it is first necessary to check that it is not only the surface that is gold. Dental gold should always be sent to the precious metal refinery to be separated, as it contains special alloys and additives that are unsuitable for jewelry because these alloys are hard and brittle.
Melting
A butane gas bottle and a large burner nozzle are adequate for melting gold. (For white gold with palladium (high melting point) and, especially, platinum, an oxygen bottle is necessary. Platinum may not be melted with acetylene or other carbon gases.) An alternative to melting with a flame is melting in a gas-powered electromelting furnace. The advantages of a melting furnace are that the temperatures can be controlled better, fuel residues avoided and the melting time reduced significantly. When alloying and melting an extractor removes unhealthy fumes from the metals and flux. (Protective goggles against ultraviolet and infra-red light are vital when melting platinum, as are gloves to protect against splashing metal.)
Alloying - the example of an 8k gold alloy
The quantities of gold, silver and copper are calculated first (Fig. 1). The proportions vary depending on whether fine gold or old gold is used, and which alloy the old gold has. The website of the Italian precious metals company Legor offers a facility for the automatic calculation of alloy compositions.
Alloying tools are a firebrick hearth, a ceramic crucible with lid, a mold for wire and sheet, a pan with a spout, crucible pincers and flux powder (Fig 2). The mold is oiled with machine oil in order to provide easier pouring and release of the cast (not too much oil) (Fig 3). With the mold illustrated it is possible to vary sheet or wire widths at will. With new crucibles the spout should be rounded off slightly with a file to facilitate the flow of the metal. For yellow gold and white gold different crucibles have to be used for not to mix components. To prevent the molten precious metal from sticking to the crucible a new ceramic crucible is glazed with melting powder.
Therefore it is positioned in the crucible pincer, filled with borax powder, heated until the powder melts (Fig. 4 and 5) and panned. The gold and silver is now added to the crucible and covered with flux, borax dust (mixture of borax, potash and common salt) in order to avoid or minimize oxidation and to lower the melting point of the alloy somewhat. The flux is heated carefully, to avoid disruption with boiling over. (Fig. 6) The tongs hold the lid of the crucible in place, enabling the heat to develop quicker inside the crucible. A low-oxygen flame is used for melting in order to avoid oxidation. The copper is only added when the gold and silver have melted. The mold is heated at the same time as the melting of the metal, at least until the condensation on the mold is evaporated (Fig. 7) but not too hot. It is poured quickly to avoid the molten liquid from becoming rigid and to reduce contact with oxygen (Fig. 8). Pincers or a hammer may be used if the metal cannot be removed from the mold. Excess metal forms on the edges of the cast which can be clipped off and rounded off with a file (Fig. 9). The cast is then pickled, removing the hard flux slag. The cast is then best forged with a heavy hammer, rolled and annealed and quenched, thus the metal structure being homogenized (Fig. 10 and 11).
The finished sheet can then be worked in any number of different ways (Fig. 12) Sufficient ventilation or extraction is a prerequisite for melting.
Gold and silver are only soluble with copper to a limited extent in a solid state. They exsolve the more they solidify. After annealing the bars or rods are plunged into cold water to interrupt this exsolving process and "freeze" a specific combination ratio and associated properties. (White gold alloys containing nickel may not be quenched, this will make them brittle.)
Precious metal supliers
The use of modern casting plants and forming tools, the use of inert gases, etc. enables precious metal suppliers to guarantee outstanding and reliable properties for their semi-finished products (plate, wire, tube, square and triangle forms, etc.) When ordering semi-finished products it is important to state tolerances, as well as clarifying whether it is necessary to anneal the precious metal to a completely soft state or whether it is to be stretched (10-15% cold formed and consequently somewhat harder). Alloys can be ordered specifically for a set purpose. For example, the elasticity of white gold containing iridium is used for designs requiring a maximum of elasticity. Most precious metal suppliers offer product data sheets for their alloys, containing detailed information.
Hallmarking laws
Hallmarking is best performed using a leather underlay to ensure, for example, that a rounded ring band does not acquire a flat point from the steel underlay (Fig. 13). An alloy is generally named after the metal that occurs within it to the greatest extent. An exception may be 333 yellow gold, as here the greatest proportion is not always made up by gold. Internationally accepted alloys are listed on the web site of the World Gold Council**. CIBJO, the international confederation of national jewelry trade organizations, authors "The Blue Books", a set of standards for diamonds, colored gemstones and pearls. In March 2007 the first meeting of the CIBJO Precious Metals Commission took place and the basic parameters for a precious metals "Blue Book" were established. This is an important step toward transparency in the field of international precious metals standards. The necessity for a guide for international precious metals standards is constantly increasing as the markets are growing together.
Advice on alloy calculation
Precision scales are used in order to achieve a precise, reproducible result. The higher the proportion of copper, the redder and harder the yellow gold alloy will be; the higher the share of silver, the brighter and softer the alloy. Jewelry alloys are stated in karat or fineness in parts per thousand. For not reducing the fineness of the alloy when using old gold all solder residues have to be cut off. An 18k white gold for example contains 750 parts yellow gold, expressed in parts per thousand. The remaining 250 parts are either exclusively palladium (very soft alloy) or are made up of palladium, silver and nickel (harder alloy, e.g. for claw settings). It is advisable to alloy slightly higher in order to stay with n the fine tolerances of statutory regulations. Images taken in the Workshop of Katrin Erben, Braunschweig, Germany.
Alloying 13.8 g of 8k yellow gold alloy (333 parts pure gold, 445 parts pure silver, 222 parts pure copper, of 1000) - percentages are dependent on required color and properties:
Pure gold weight = weight of alloy x percentage of pure gold
Added weight = weight of alloy x percentage of added metal
Added single weight = percentage of added metal x weight of pure gold : percentage of pure gold
Gold 24k: 13.8 g x 0.333 = 4.6 g
Added metal (silver and copper): 13.8 g x 0.667 = 9.2 g
Silver: 0.445 x 4.6 g : 0.333 = 6.1 g
Copper: 0.222 x 4.6 g : 0.333 = 3.1 g
Alloying 14k yellow gold (585 parts of 1000) from 8k yellow gold (333 parts of 1000):
Weight of new alloy (14k) = weight of old alloy (8k) x percentage of added metal, old : percentage of added metal, new (1000 - 333 = 667; 1000 - 585 = 415)
Weight of added pure gold = new weight of alloy - old weight of alloy
Weight of 14k yellow gold = 13.8 g x 0.667 : 0.415 = 22.18 g
Added pure gold = 22.18 - 13.8 g = 8.38 g
*www.legor.com (maths for gold jewelry)
**www.gold.org/jewellery (hallmarkings)
**www.thegoldsmiths.co.uk/assayoffice/currenthallmarks
by Christine Patrich
You assume all responsibility and risk for the use of the safety resources available on or through this web page. The International Gem Society LLC does not assume any liability for the materials, information and opinions provided on, or available through, this web page. No advice or information provided by this website shall create any warranty. Reliance on such advice, information or the content of this web page is solely at your own risk, including without limitation any safety guidelines, resources or precautions, or any other information related to safety that may be available on or through this web page. The International Gem Society LLC disclaims any liability for injury, death or damages resulting from the use thereof.
Related Articles
A Legacy in American Metalworking
Metals For Enameling
Additive Manufacturing in the Jewelry Scene
Goldsmithing in the Future
The All-In-One Jewelry Making Solution At Your Fingertips
When you join the Ganoksin community, you get the tools you need to take your work to the next level.
Trusted Jewelry Making Information & Techniques
Sign up to receive the latest articles, techniques, and inspirations with our free newsletter.