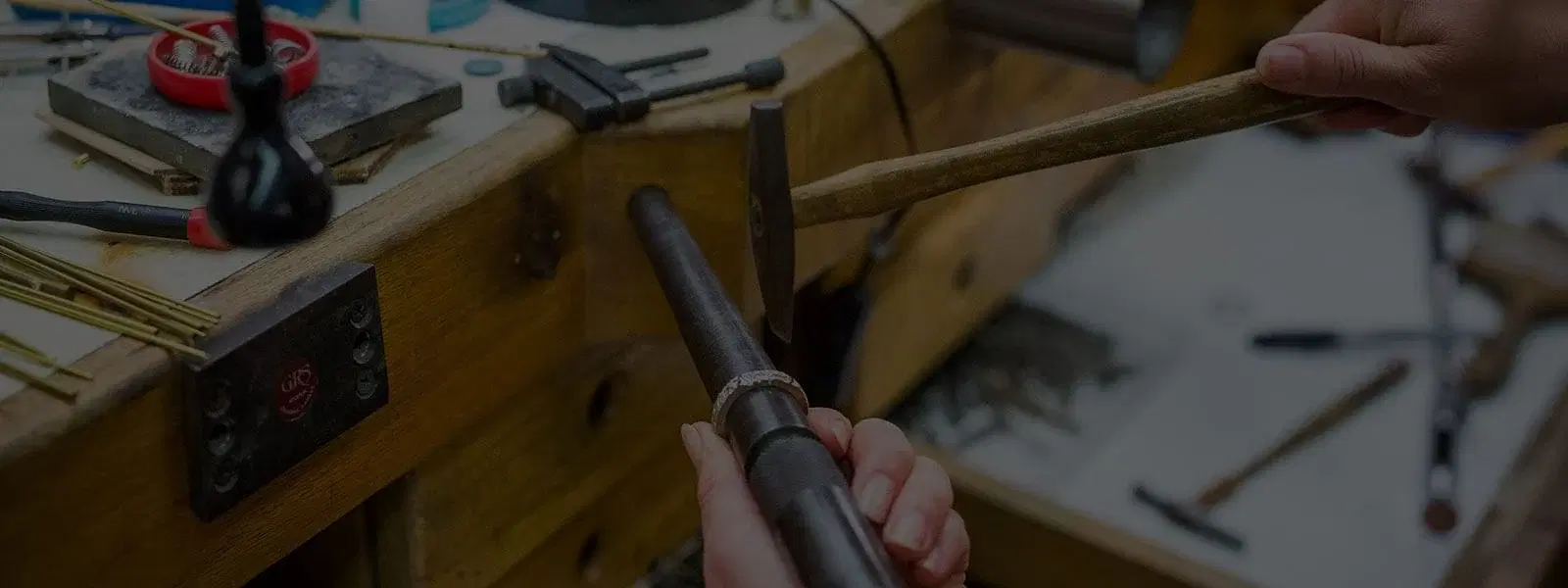
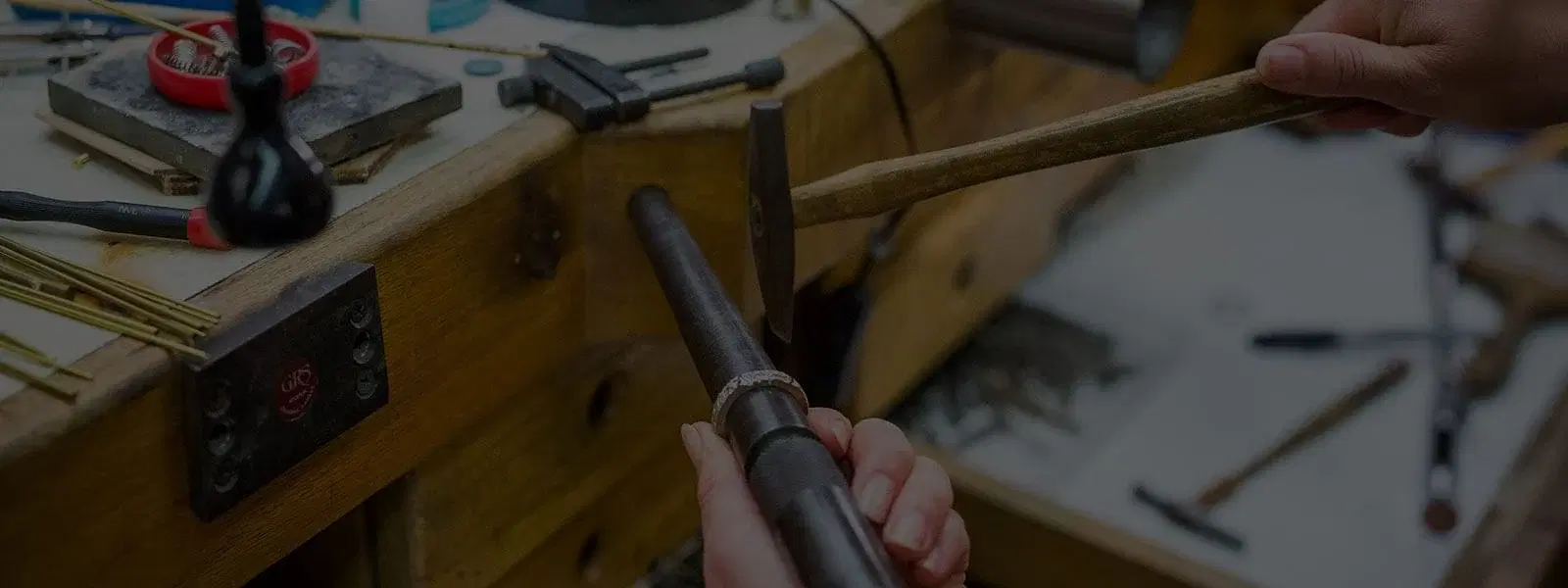
Setting Gemstone on Precious Metal Clay
PMC is not a traditional material, and so a few pioneers went about tentatively setting cubic zirconia's, and lab grown corundum into the clay. For almost a decade it has been believed that natural stones would be destroyed in the sintering process. And so nobody took the risk. A few brave souls attempted to "cast" diamonds in place in the kiln. Proving to not only be a costly experiment, but.
7 Minute Read
Somewhere along the way, humans felt the need to adorn themselves with the beautiful things they found around them. They first strung broken ostrich shells on whatever was handy, and wore them about their necks. Farther down the road, we discovered how to work simple metals. Farther still, we found a way to mine, and crudely polish beautiful gemstones. Eventually we set gems into our metals.
We found many methods to make our wearable art. We adorned ourselves with it for thousands of years prior to today. For the world, there was only one method of manufacture, and that was fabrication. A time consuming highly involved process where a master jeweler could make a single ring in a few days time. More recently, casting has come about. Scraps of metal are melted, and poured into a negative mold while the precious alloys are still molten. Over the course of half a dozen combined millennia, man found just about every way imaginable to work and create jewelry with these simple methods. Hammers, Saws, vices, anvils, acids and other assorted tools were necessary to make even the simplest of items.
Fast forward to 1991 a revolutionary material hit's the market. It requires not saws and hammers, but fingers and x-acto knifes. It feels like putty but turns into solid precious metal. PMC was born. For quite some time, only solid metal objects were created from this material. With no prior exposure to precious metal clay, many jewelers turned to fabrication techniques to aid in their creations. Soldering, riveting, and working the metal after it had been sintered to its final form. Mankind's love for precious gems could not be ignored and so it came to be findings and such were soldered on after the fact, and stones were set in traditional methods.
PMC is not a traditional material, and so a few pioneers went about tentatively setting cubic zirconia's, and lab grown corundum into the clay. For almost a decade it has been believed that natural stones would be destroyed in the sintering process. And so nobody took the risk. A few brave souls attempted to "cast" diamonds in place in the kiln. Proving to not only be a costly experiment, but an unsuccessful one.
Present day. This book will teach you about the different ways to set stones, without traditional fabrication methods. Not only can diamonds be sintered in place, but also a myriad of other wonderful and precious gemstones can be utilized. …
Created Moissanite
I found out unwittingly that Moissanite doesn't have a lovely appearance when it comes out of the kiln. It basically looks like graphite and has the luster of corduroy. I believe I was the first artisan to attempt the firing of Created Moissanite, or the first person to admit I screwed up. Whatever the case may be, I found out the hard way it cannot be put through the kiln. But it CAN be sintered in place. This is where torch firing comes in handy.
Create your piece as normal and embed the stone. Do NOT create a light hole, you'll find out why in a bit. After the piece is fully dry, insulate the stone with some high heat shielding material like Chill Gel. Cover the entire exposed table. Be careful not to allow the gel to come into contact with the green (unfired) PMC. When the PMC sinters, you'll have major trouble on your hands because the gel will be absorbed by the porous silver. It is near impossible to polish and looks like you managed to burn the silver as if it were a piece of charcoal. It cant be removed… I've tried.
Place the piece face down on a fiber slumping pad. Any soldering pad that is fibrous and easily moldable will work, but I prefer the slumping pad the best. Press the piece down into the pad until the back of the item is level with the surface of the pad. Dim the lights so you can best see and gauge the color of the metal later and begin.
Light up your torch of choice. It doesn't have to be anything fancy. I prefer to use a 7 dollar hand held pencil torch that operates on butane fuel. Run the flame along the piece. Always keep the torch moving. Never let it rest in one spot. Think reticulation when you are torch firing Moissanite. Keep this up until the binder burns off. It will look like a candle flame. You can turn off the torch and let it burn away completely. After it peters out, let the piece cool down. don't touch it, the silver is basically just sitting there. It isn't fused by any means.
Now begin to reheat the piece. Move the flame along the piece in a reticulation style sweeping motion. Never let the flame rest in one spot. you'll achieve the best results if you concentrate the tip of the blue part of your flame right on the back of the piece. don't let the flame "bend" or "split" because your pressing it to hard against the jewelry. Keep this up until the piece glows a warm cherry orange red. If you start to see the metal "sweat", then you are heating it to much, back off a little bit. This is why you dimmed the lights earlier so you can control the color accurately. Once it hits that color of red-orange, start timing. One minute for PMC3 and two minutes for PMC+. Its best to use the 3 in these situations. After you have maintained that color for the allotted time, back off and let the piece cool face down. Finish as desired.
Some Things to Watch Out For
Near colorless created Moissanite is actually a light golden green in appearance when formed in the lab. a lot of money and effort has been put into making it near colorless. When the stone is heated it will have a tendency to want to revert back to this color.
TIME is more crucial them TEMPERATURE. Moissanite can withstand temperatures high enough to vaporize a diamond, and come out unharmed. However for some as of yet unknown reason, when in contact with PMC, Moissanite will usually cloud and discolor. However I have found through extensive experimentation that the shorter amount of time Moissanite is subjected to heat while in PMC, the more successful the results tend to be. It will take the heat, just keep it brief.
Open flames are NOT your friend. The point for not piercing a light hole behind the stone is to insulate it form the flame. In a kiln atmosphere, without any PMC touching Moissanite. There is an even blanket of heat. For some reason, the torch tends to char the stone when it comes into contact with it.
At the time of this publication, I am the only known PMC artist to have successfully fired Created Moissanite in place. I can report success in both PMC Plus and Three. I cannot say unequivocally that every attempt will be successful. I have had mixed success with both green and near colorless created Moissanite. To improve the chances of success you can employ a technique pioneered by Toshihide Ueeda. This involves sweating the surface of the PMC all over and leaving it at that. On a small pendant this technique could take about 10 seconds after the binder is burned away. Perfect for Moissanite, it will compromise the structural integrity of your piece. It will be metal, but not fully sintered. You basically pass a high heat flame over the piece after the binder has burned off. The heat form the flame should be enough to melt the outer layer of metal. This intense heat fluctuation will create a skin of metal that has the density of cast fine silver, and an inner layer of silver that is the density of PMC standard. This technique works best on PMC3.
Attempt this firing technique at your own risk. Your results may vary. If you are unsure about how successful you may be, or cannot afford to take the chance with your stone or your work, then don't do it. Period. Set it after the fact and save yourself the potential frustration.
Diamonds
sure the gem in question is 100% natural. Heat will mutate the irradiation process and cause irreparable harm to the stone. It is also wise to note that if you have any question about a diamonds enhancements, to set it afterwards. It is rare but some diamonds may be fracture filled with glass that boasts a similar Refractive Index to that of its host diamond. It will explode. If your diamond has natural inclusions from other gem species, or other colored particles of diamond itself, be aware that they may discolor or explode. "Bearded" diamonds are particularly tricky to set into PMC properly. Bearding occurs during the bruiting process of the stone where tiny fractures form along the girdle of the stone and cause a near opaque ring around the girdle of the stone. This seriously affects the diamonds structural integrity and should be noted that such fractures may expand during the heating process and cause further harm
Once again, attempt this at your own risk. The author assumes no liability for any harm you may cause to yourself, your stone, or your possible eviction from your place of residency for the foul language that may emanate from your home if you are unsuccessful.
You assume all responsibility and risk for the use of the safety resources available on or through this web page. The International Gem Society LLC does not assume any liability for the materials, information and opinions provided on, or available through, this web page. No advice or information provided by this website shall create any warranty. Reliance on such advice, information or the content of this web page is solely at your own risk, including without limitation any safety guidelines, resources or precautions, or any other information related to safety that may be available on or through this web page. The International Gem Society LLC disclaims any liability for injury, death or damages resulting from the use thereof.
Related Articles
The Use of Pearls in Cosmetics
World Mining Report 2005 – Australia
Handling Colored Stones at the Bench Part 2
Amber – Frozen Moments in Time
The All-In-One Jewelry Making Solution At Your Fingertips
When you join the Ganoksin community, you get the tools you need to take your work to the next level.
Trusted Jewelry Making Information & Techniques
Sign up to receive the latest articles, techniques, and inspirations with our free newsletter.