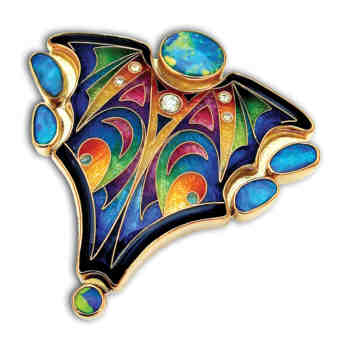
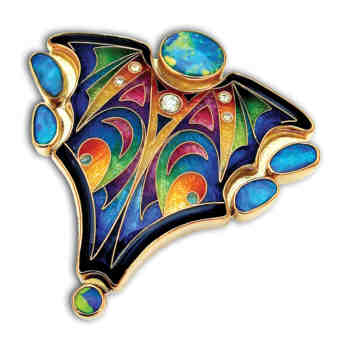
The Metal Underneath
In this article, I will discuss the basics of metal preparation for the enameling process. Some experienced enamelists may disagree with part of this. But remember, these are general rules from a metallurgist's point of view, not an enamelist's. The article is not intended to outline or recommend any particular preparation or enameling technique, but rather explain why we do certain things to precious metals during the process of enameling..
13 Minute Read
A mesmerizing pattern of rainbow-colored enamels catches your eye. The dynamic pendant is a wearable work of art. Its enamel coating tells a story. But if you dig a bit deeper, you'll find that the metal underneath has a tale all its own.
As a metallurgist working in the jewelry industry, I focus on the precious metal side of enameling. A decorative process, jewelry enameling can be explained simply as a technique that involves firing vitreous material (one or more layers) onto a precious metal base. The enamel, which is colored glass, bonds to the surface of the metal after being heated to the molten state and then being allowed to cool.
So it stands to reason that anything preventing this bonding needs to be removed. Dirt and grease on the surface, oxide and tarnish layers, and even metallic elements in the composition that volatilize at or below the enameling temperature are all detrimental to the process. In this article, I will discuss the basics of metal preparation for the enameling process.
Some experienced enamelists may disagree with part of this. But remember, these are general rules from a metallurgist's point of view, not an enamelist's. The article is not intended to outline or recommend any particular preparation or enameling technique, but rather explain why we do certain things to precious metals during the process of enameling.
Alloy Selection
Enameling on fine gold or fine silver has obvious advantages: These elements do not generate oxides that can interfere with enamel adhesion. Base metal additions, which form alloys of gold and silver, complicate matters. For example, copper oxide prevents enamel adhesion and also results in color problems. Worse yet are the complications that arise when enameling precious metal jewelry alloys that contain zinc, which may be present in both karat gold and deox sterling silver alloys.
There are two problems associated with zinc: The presence of zinc oxide on the metal surface prevents adhesion and leads to color problems. The metal volatilizes from the surface at enameling temperatures, even if the surface has been pre-cleaned. Ever wonder why you get those yellow/white deposits on the inside of an annealing furnace? That's where zinc has vaporized from the solid metal and then condensed on the furnace surface. If zinc volatilizes from the metal surface during the enameling process, it becomes trapped by the liquid enamel and leads to the formation of bubbles as it expands-something no enamelist wants.
Karat gold alloys nearly always contain copper, but do not necessarily contain zinc. Most 18k and 22k alloys-with the exception of the majority of white gold alloys-have three components: gold, silver, and copper. Varying the ratios of the latter two elements results in yellow, green, and pink gold. From an enameling point of view, the lack of zinc content in these alloys ensures a better product. Zinc may be added to these higher karat alloys up to about one percent by weight for deoxidation purposes, but otherwise it is not strictly necessary.
On the other hand, gold alloys in the lower karats (such as 8k, 9k, 10k, 12k, and some 14k alloys) usually contain zinc in quantities up to 10 percent. Here zinc has a more profound effect on gold color, giving yellow alloys a warmer feel. Omitting zinc from these alloys results in a yellow color that has a pale pink (high copper alloys) or green (high silver alloys) hue.
White gold alloys may or may not contain zinc. There are three main families of white gold: The first comprises gold-silver-copper-zinc, the second uses palladium as the primary bleaching agent, and the third uses nickel. For enameling purposes, the first family can be treated in a similar fashion to the low karat yellow gold alloys. The palladium alloys do not require the presence of zinc, although this does not mean an alloy manufacturer will automatically omit the element. There is also potential for oxidation with alloys that contain copper, including gold / copper / palladium and gold / copper / silver/ palladium alloys. (Some palladium white gold alloys do omit copper and consist of just gold, silver, and palladium.)
The nickel alloys usually include zinc-typically up to about six percent-for several reasons. Zinc bleaches gold and increases the malleability and ductility of the alloy during cold working operations, such as rolling and drawing. It can also act as a deoxidizer if the alloy is used for investment casting. While reducing the zinc content will improve enameling results as well as inhibit fire cracking, which can be a major problem with these alloys, it compromises the alloy's color and ductility.
Sterling silver alloys, another popular choice for enameling, typically include copper and sometimes zinc, which is used as a deoxidizer. (Deox sterling alloys may also contain germanium, which can cause problems during enameling because of its low melting point.) In addition to the potential complications associated with enameling on zinc-containing metals, sterling can be contaminated with trace amounts of the elements selenium and tellurium, which occur naturally in silver ore. As little as 5 parts per million combined of these elements will prevent enamel adhesion. I am unsure of the reason, but there are a number of compounds formed with these elements that may contribute to the problem. It's important to note that this problem occurs very rarely.
Considering the above complications, it's essential to discuss alloy content with your metal supplier when choosing a karat gold or silver alloy for enameling. Find out how much zinc is in the composition. If possible, choose alloys that are either zinc-free or contain very low zinc concentrations, typically less than 2 percent. Alloys containing higher zinc concentrations can be successfully enameled, but they require more care in the preparation stages. Precious metal alloys containing up to 10 percent zinc have been successfully enameled, particularly if opaque enamels are used, but they are not recommended if you are aiming for repeatable results.
Metal Preparation
The first step in preparing the metal for enameling is to stress relieve the workpiece to prevent any distortion that may occur during the enamel firing cycle. For both karat gold and sterling alloys, this step normally consists of heat-treating the metal at 660oF/349oC for one to two minutes.
The next step is surface enrichment, also known as depletion gilding. When used on karat golds, this process denudes the surface of silver, base metals, and oxides, leaving it enriched in fine gold. It also ensures that the work is completely stress relieved. The same process is used on silver to remove base metals and oxides, leaving an enriched fine silver surface.
To enrich the surface of a karat gold or silver piece, heat it with a torch or in a furnace without fire coat to allow the base metals-usually copper, zinc, and sometimes nickel-to oxidize. Heating to cherry red (about 1,100oF/593oC) is recommended, but most enamelists determine what works for them and stick to it. It sometimes speeds oxide removal if the workpiece is quenched in water once the red glow is no longer visible. (Use caution if you are working with a 14k or 18k nickel white alloy, since cracking can occur when quenching.)
The oxides can then be removed by pickling in 10 percent sulfuric acid, followed by silver and base metal removal by further pickling in 10 percent nitric acid, leaving an enriched fine gold or silver surface. Be wary of leaving the workpiece in nitric acid for too long, as all the base metals will be removed and your workpiece will disintegrate. There is no strict rule for timing; it comes from experience. However, if you are working with silver, the window of opportunity is lessened, as the nitric acid will start to attack the silver once the base metals are removed.
The initial heat-and-pickle cycle will remove oxides and base metals close to the surface; additional oxidizing heat treatments are necessary to get a deep, sub-surface enriched fine gold or silver layer. As a general rule, the lower the karat used, the more times it needs to be depletion gilded, since a higher content of base metals is present.
It is recommended to repeat the surface enrichment process at least three or four times to ensure that no base metals remain at the surface. Keep in mind that this is a case of better too many than too few. (Note: Some enamelists like to fuse fine gold over the workpiece to negate the need for surface enrichment of karat gold alloys. This provides a pure gold surface on which to enamel.) Once the piece has been adequately surface enriched, it must be meticulously cleaned. Most enamelists I've spoken to pickle in warm 10 percent nitric acid to remove any final traces of oxides, base metals, grease, and dirt. Some prefer to use 10 percent sulfuric acid because it is less reactive and results in a suitably clean surface. However, using nitric acid provides a superior surface. Whichever acid you choose for pickling, finish by neutralizing in an alkali bath, such as 10 percent sodium bicarbonate, to remove any traces of pickling acid. If there is potential for the acids to remain in surface porosity or areas where liquids may become entrapped by capillary action, perform the neutralizing process in an ultrasonic bath. Any residual acids will eventually result in corrosion products and lead to discoloration. (An alternative cleaning method is electrolytic stripping, which provides an excellent surface finish for enameling, but involves significant equipment costs.)
When metal preparation is complete, the enamel layers can be applied. I will not go into the details of this process, but the basics are as follows: Enamels usually come in powder form and are wetted with distilled water to make a thick slurry. The first layer of enamel slurry is applied, with care taken to ensure that all the metal surfaces in the area to be enameled are covered to prevent further oxide formation during firing. The slurry is allowed to dry, then fired with a torch or in a kiln. Since firing temperatures for each enamel vary (generally around 1,500oF/816oC), it is important to follow the manufacturer's instructions.
Once the piece is fired, it is removed from the heat source and allowed to cool slowly. Sometimes small pieces "ping off" the enamel; this is okay, since they can be filled during the next application. The enamel application and firing process is repeated until the desired enamel depth is reached. With most designs, this process is complete when the enamel is level with the surface of the metal used to contain it. At that point, the piece is pickled to remove any oxides that have formed on the exposed metal parts. It is then finished by abrading the surface of the metal and enamel to be flush, then polishing with successively finer grades of abrasives to achieve the desired finish.
Points of Note
Solders. It is advisable to perform all necessary soldering operations before the firing cycle to prevent heat damage to the enamel. In addition, solders used on enameled pieces must be of a grade that has a solidus (melting point) higher than the enameling temperature, or the workpiece will fall apart as the solder re-melts during firing.
It's also advisable to keep solder joints to a minimum, since karat gold solders often contain high concentrations of zinc to lower the melting range, as well as cadmium to increase wetting. This second element behaves like zinc when heated and will have similar associated problems. In addition, be sure the joint area is properly depletion gilded, while still maintaining its integrity.
Pink and red karat gold alloys. Enameling on lower karat pink and red gold alloys isn't usually a problem, although the heavy oxides generated by the alloys' increased copper content must be accommodated. However, the higher karat red alloys, such as 18k and 22k, can pose problems.
A phenomenon known as the "order/disorder transformation" occurs at temperatures below about 750oF/400oC with high copper concentrations in 14k, 18k, and 22k alloys. This transformation is dependent upon the metallurgical relationship between gold and copper when present in atomic ratios of 1:1 (18k) 1:3 (14k) and 3:1 (approaching 22k).
Atomic movement generates internal strains when the metal is cooled from annealing-in this case enameling-temperatures. These internal strains make the metals hard and can also distort the workpiece, and in extreme cases can lead to cracking. The strains are greatest in 18k red gold alloys and lead to significant hardening. Although ordering can also occur in 14k red alloys and 22k red alloys, atomic movement is such that far less strain and distortion occurs, making enameling somewhat easier.
Quenching from above 770oF/410oC will reduce the problem in 18k red gold, but this is not possible once the first coat of enamel has been applied. As a result, 18k red alloys are probably the most difficult to successfully enamel.
Mass Production
Choosing the best alloy for enameling and properly preparing the metal surface are essential steps to successful enameling, whether you are making a one-of-a-kind piece or a high volume production line. The major difference in mass production is scale: When doing a single item, a mistake is costly-but not nearly as costly as ruining a batch of 100 or more. To improve the odds of success when enameling in high volumes, keep the following suggestions in mind:
Choose an alloy that enamels easily. Enameling 18k red gold can be difficult-but achievable-for a one-off. Enameling hundreds is asking for trouble.
Whenever possible, use enameling-friendly techniques for manufacturing. There are thousands of perfectly good enameled products that use investment castings as a base, so obviously it can be done. But shrinkage and gas porosity are known defects from the investment casting process, and a porous surface can present problems. Although some argue that the "rough" surface will help the enamel adhere, I have seen more harm than good come from porous surfaces. For example, I have dealt with problems where the surface porosity has entrapped acids during the numerous pickling operations, which in turn led to discoloration that was often only noticeable after the item was finished.
Manufacturing the item from mill and die-struck products is a better route when enameling, although it's not always cost-effective. If investment casting is the only feasible method, meticulous surface preparation is essential. Once again, failure is never good-but it's a lot easier to take if you're doing one piece versus a thousand.
Control the temperature. Make sure you have accurate temperature control. Some enamels have melting points close to that of sterling silver or the lower-melting-point karat gold alloys. If your firing temperature goes above the solidus of the metal, the result is often a poor and sometimes porous surface. This is particularly true with sterling silver, due to the large temperature gap between the solidus and liquidus. In sterling, you can also get localized melting, called incipient fusion, without the whole piece melting.
Happy Ending
In general, when choosing a silver alloy for enameling, the simpler the better: Copper/silver alloys that don't contain zinc provide the best results. When choosing a karat gold alloy for enameling, the higher the karat the better. As the karat level decreases, the base metal concentration-including zinc-increases. Decreased base metals equal an easier process, which in turn results in less potential for failure.
Yellow gold alloys pose fewer problems than whites and reds, but even red and white karat gold alloys can be enameled if the technique is correct. If red alloys are used, be aware that they will oxidize more heavily and may distort, particularly in 18k. That doesn't mean these alloys can't be enameled, only that they need to be treated with care.
These points must all be considered when deciding which gold alloy to use. When ordering, ask your supplier if the alloy you are choosing can be enameled, and if any special considerations are required. By following the steps outlined in this article for metal choice and preparation, you're on your way to telling an enameling story with a happy ending.
The award-winning Journal is published monthly by MJSA, the trade association for professional jewelry makers, designers, and related suppliers. It offers design ideas, fabrication and production techniques, bench tips, business and marketing insights, and trend and technology updates—the information crucial for business success. “More than other publications, MJSA Journal is oriented toward people like me: those trying to earn a living by designing and making jewelry,” says Jim Binnion of James Binnion Metal Arts.
Click here to read our latest articles
Click here to get a FREE four-month trial subscription.
You assume all responsibility and risk for the use of the safety resources available on or through this web page. The International Gem Society LLC does not assume any liability for the materials, information and opinions provided on, or available through, this web page. No advice or information provided by this website shall create any warranty. Reliance on such advice, information or the content of this web page is solely at your own risk, including without limitation any safety guidelines, resources or precautions, or any other information related to safety that may be available on or through this web page. The International Gem Society LLC disclaims any liability for injury, death or damages resulting from the use thereof.
Related Articles
Carat Gold Solders for Jewellery Making
Different Coloured Gold Alloys
De-oxidized Sterling Silver Alloys
Electric Kiln Fired Mokume Gane Part 1
The All-In-One Jewelry Making Solution At Your Fingertips
When you join the Ganoksin community, you get the tools you need to take your work to the next level.
Trusted Jewelry Making Information & Techniques
Sign up to receive the latest articles, techniques, and inspirations with our free newsletter.