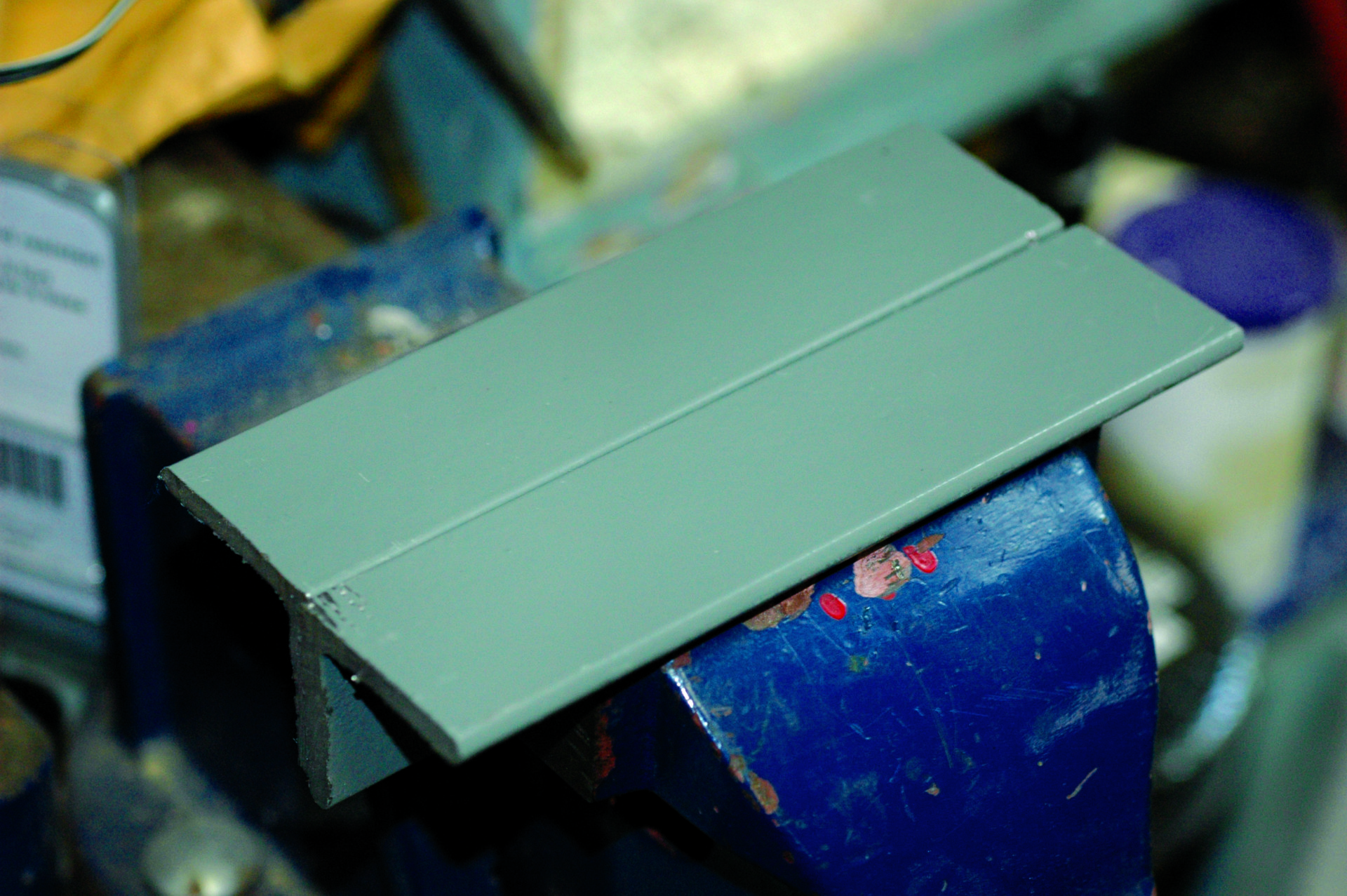
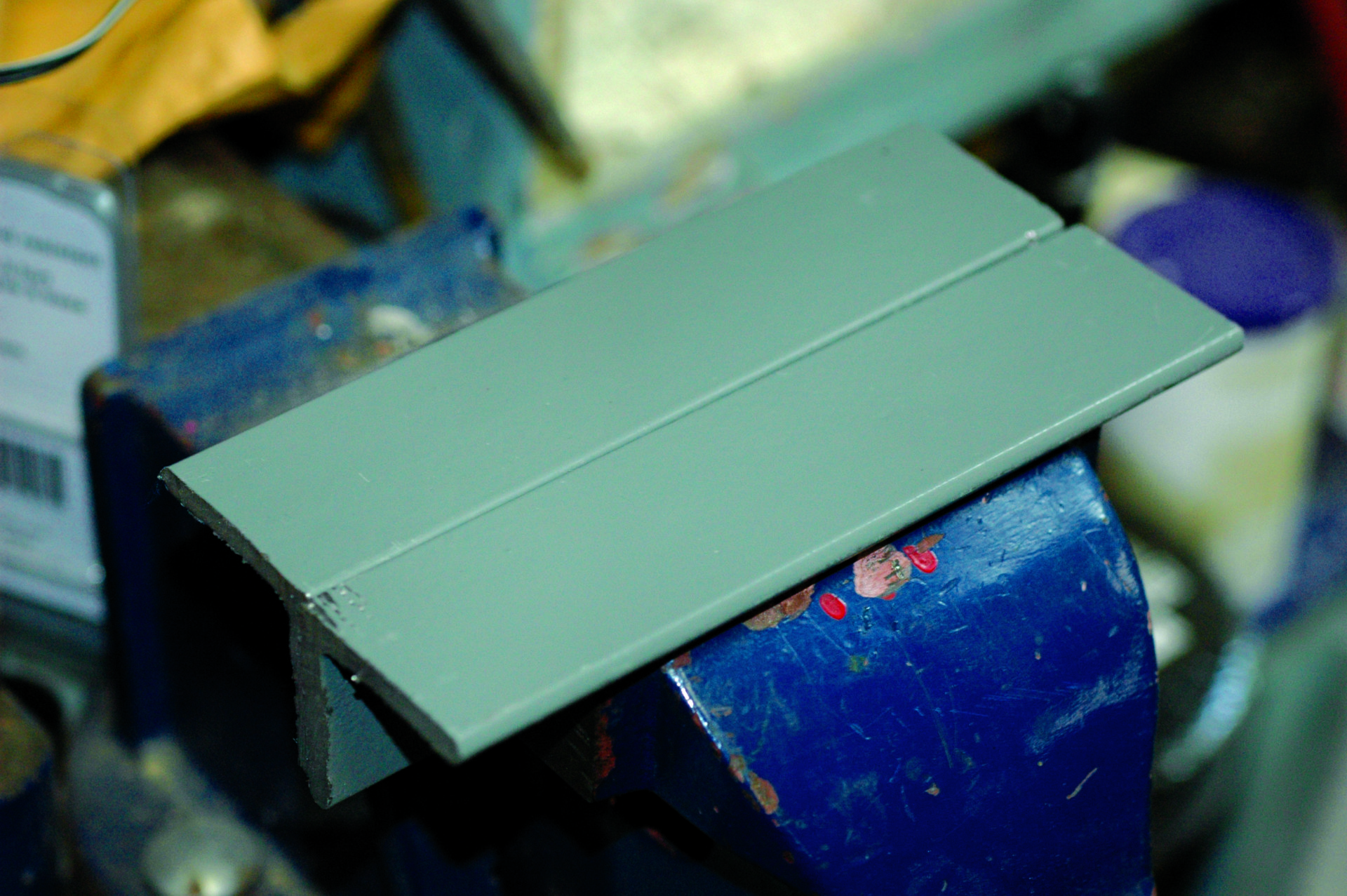
Tips for Modifying Vises
2 Minute Read

A good vise is a vital piece of equipment for any goldsmith because it can act as a third hand, securely holding onto a piece while the goldsmith uses both free hands to work on it. Given their usefulness, it's no surprise that many jewelers keep multiple vises in their studios.
I myself keep small ones on the right and left sides of my bench, as well as a number of larger ones around my workshop. And I always have one next to my torch so it can hold metal while I heat it.
Vises are available in a variety of sizes and styles, and you can often pick up quality antique ones from places such as eBay. If your budget is limited, there are ways to modify a basic machinist's vise, which is the most commonly available type, to get it to do more than originally intended.
Smooth Top
If you do want to do any fold-forming work, a flat-topped vise is essential, as it permits working with larger pieces. It's possible to find an antique one that was built with a flat top, but if you don't have any luck on eBay, you can create your own. Take a machinist's vise and grind the projecting vise jaws flat using an angle grinder. This will take about an hour or so, and watch out for flying sparks in your studio. If you don't have the time or ability to alter the vise, you can clamp two pieces of angle iron into the vise to create a perfectly flat work surface.
Jaw Replacement
In your search for vises for your workshop, you may come across one with damaged jaws but in otherwise perfect condition. It's still a good buy, as the vise jaws themselves can be unscrewed and replaced with other materials, such as smooth steel, hardwood, Delrin, or nylon. You'll just need to drill holes to match the screws holding the vise jaws on. Screw on the replacement jaws and your vise will be as good as new.
Adding Protection
Vises are critical pieces of equipment because they can clamp down and hold onto materials tightly. But the strength that makes them so useful at the bench can also result in damage to the piece being held. One way to add protection is to wrap a sheet of 24 gauge copper onto the vise's jaws. Fold the middle portion of the sheet over the jaws first, then use a mallet to tuck in the ends (as if you are making "hospital corners"). This copper shield will make the vise jaws soft enough to protect the object you're working on, but still hard enough to clamp it securely.
Increasing Speed
One way to speed up a machinist's vise is to bend the handle. Heat the handle about a quarter of the way down with a torch. Once the handle is red hot, hammer it over. The bent handle will make the vise easier and faster to use. You can also replace the handle with a wheel, such as the kind you would find on a lathe.
Vises are vital in the workshop, but you don't have to use them the way they were supplied. Small changes such as the ones I've described here can make a daily difference in your efficiency, speed, and capabilities.
The award-winning Journal is published monthly by MJSA, the trade association for professional jewelry makers, designers, and related suppliers. It offers design ideas, fabrication and production techniques, bench tips, business and marketing insights, and trend and technology updates—the information crucial for business success. “More than other publications, MJSA Journal is oriented toward people like me: those trying to earn a living by designing and making jewelry,” says Jim Binnion of James Binnion Metal Arts.
Click here to read our latest articles
Click here to get a FREE four-month trial subscription.
You assume all responsibility and risk for the use of the safety resources available on or through this web page. The International Gem Society LLC does not assume any liability for the materials, information and opinions provided on, or available through, this web page. No advice or information provided by this website shall create any warranty. Reliance on such advice, information or the content of this web page is solely at your own risk, including without limitation any safety guidelines, resources or precautions, or any other information related to safety that may be available on or through this web page. The International Gem Society LLC disclaims any liability for injury, death or damages resulting from the use thereof.

Charles Lewton-Brain
Master goldsmith Charles Lewton-Brain trained, studied and worked in Germany, Canada and the United States to learn the skills he uses. Charles Lewton-Brain is one of the original creators of Ganoksin.
Related Articles
Homemade Flex-Shaft Guard
Laser Welding Replacing Soldering
Cardboard Disc Sander Tool
Pollution Control / Metal Recovery
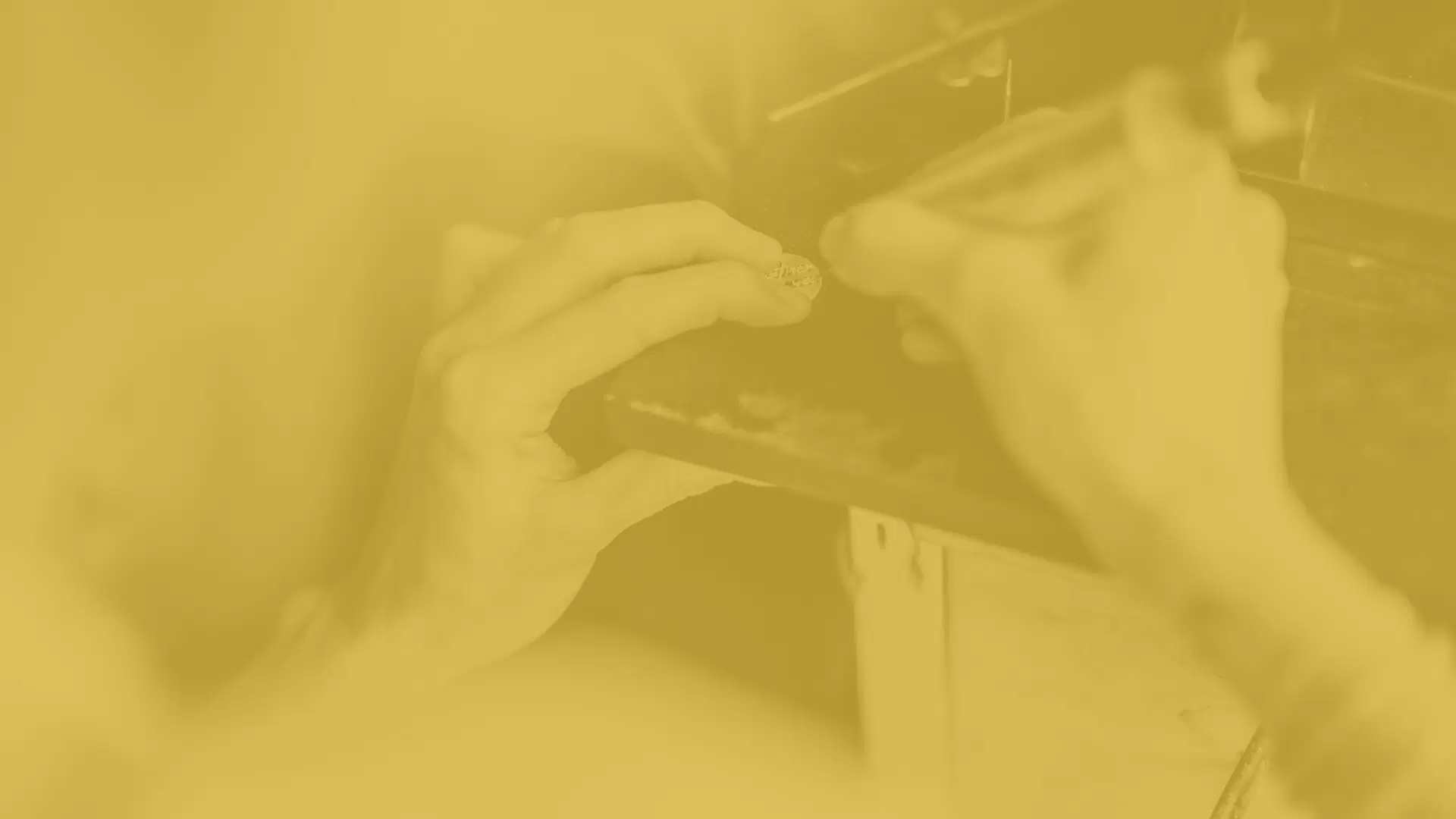
The All-In-One Jewelry Making Solution At Your Fingertips
When you join the Ganoksin community, you get the tools you need to take your work to the next level.
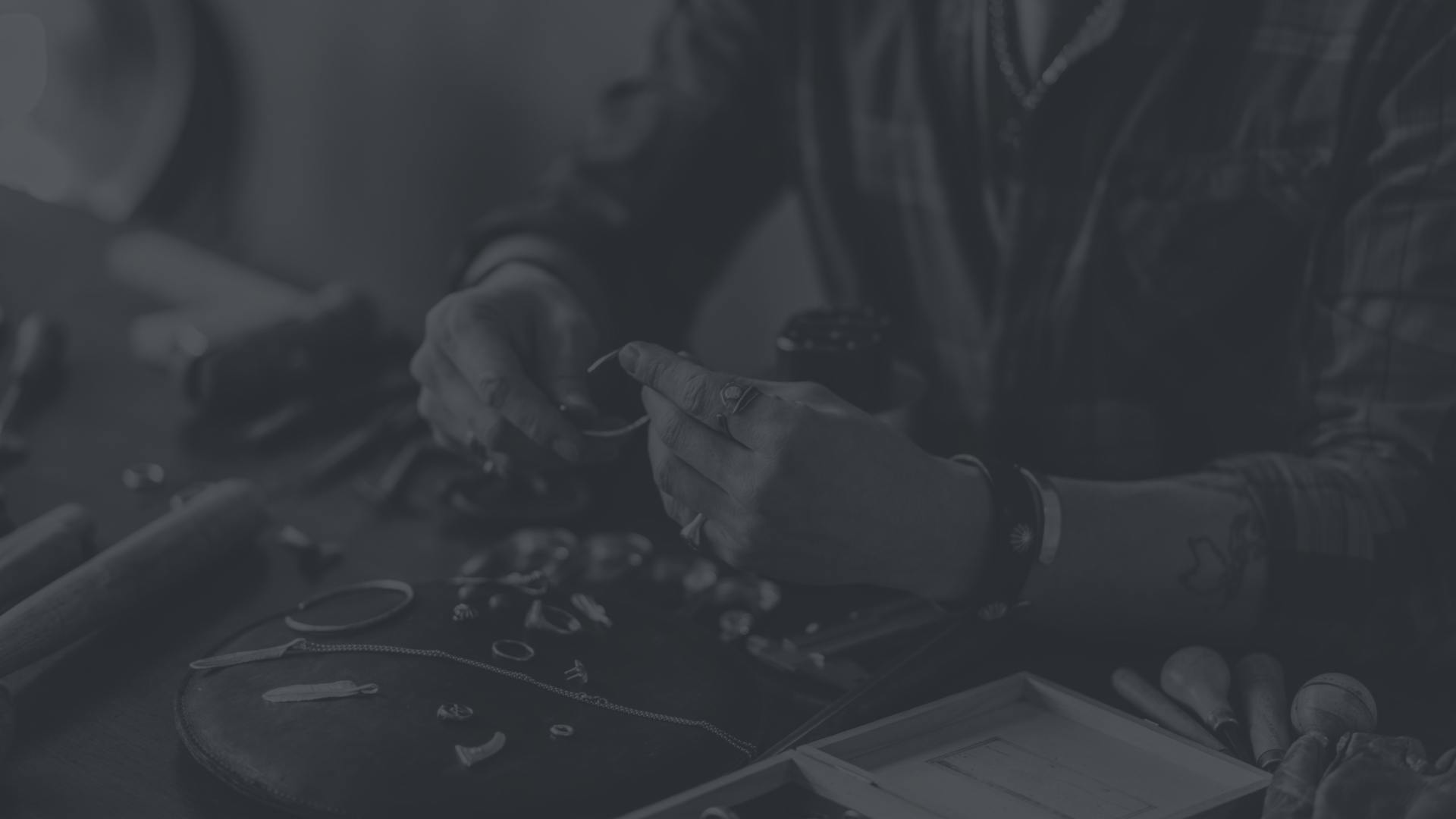
Trusted Jewelry Making Information & Techniques
Sign up to receive the latest articles, techniques, and inspirations with our free newsletter.